La poudre métallique pour l’impression 3D est coûteuse et une grande quantité de poudre reste inutilisée au cours d’un travail d’impression. Toutefois, avant d’être réutilisés, les agglomérats de poudre fusionnée doivent d’abord être séparés. Dans le cadre du projet de recherche IDAM 1), VOLKMANN a développé une station de recyclage de poudre à cette fin et l’a intégrée dans un processus entièrement automatisé d’impression 3D, de déballage et de recyclage de poudre chez BMW AG.
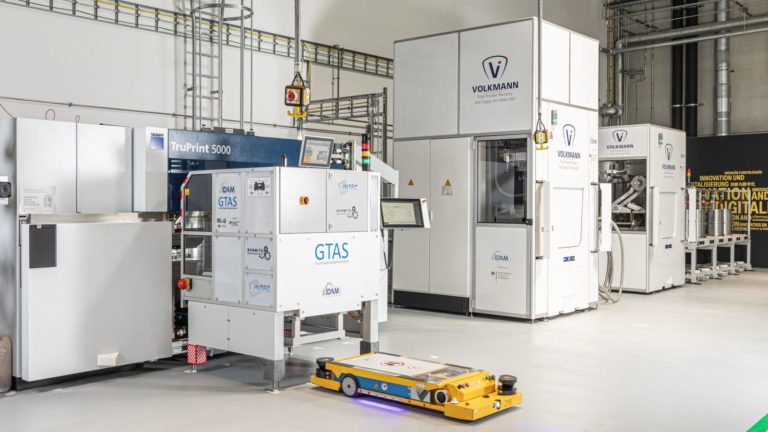
L’impression 3D industrielle avec des poudres métalliques produit également – en plus des composants souhaités – de nombreux petits agglomérats de particules de poudre fondue. Des structures de support brisées peuvent également se trouver dans la poudre utilisée. Ces agglomérats de particules et ces corps étrangers doivent être éliminés de manière fiable avant que la poudre ne soit réintroduite dans un processus d’impression.
La poudre recyclée est généralement mélangée à de la poudre vierge. La quantité de nouvelle poudre compense celle qui a été traitée précédemment dans les composants imprimés. Le rapport de mélange entre la poudre vierge et la poudre recyclée peut affecter la qualité des composants, c’est pourquoi le développement des produits et l’assurance qualité imposent souvent des spécifications strictes. En outre, il faut veiller à ce que le mélange soit homogène.
Le projet IDAM (industrialisation et numérisation de la fabrication additive) a été financé par le ministère fédéral allemand de l’éducation et de la recherche (BMBF). La ligne de démonstration du projet de recherche IDAM est une ligne de production d’impression 3D entièrement automatisée, en réseau numérique, destinée à la production automobile en série. Sous la direction du BMW Group, un total de 12 entreprises et instituts de recherche ont participé au projet de 2019 à 2022, y compris VOLKMANN GmbH. Des essais pratiques ont été réalisés avec succès sur une ligne de démonstration chez BMW AG (Munich, Allemagne) et sur une deuxième ligne chez GKN Additive (Bonn, Allemagne). La préparation de la poudre métallique usagée et le mélange avec de la poudre vierge ont été effectués dans la ligne de démonstration de BMW AG par une station centrale de recyclage de la poudre. Chez GKN, le recyclage de la poudre a été effectué par un système PowTReX de VOLKMANN.
La station centrale de recyclage des poudres de BMW a été développée et construite par VOLKMANN, qui y a intégré l’expérience opérationnelle précieuse du système de recyclage des poudres PowTReX. En outre, la station permet de stocker séparément la poudre usagée et la poudre vierge, ainsi que de mélanger ces poudres métalliques dans un rapport spécifié par l’utilisateur. La station s’occupe également du séchage de la poudre métallique – nous y reviendrons plus tard.
Le très haut degré d’automatisation de la ligne de démonstration IDAM se retrouve également dans la station de recyclage des poudres. La poudre métallique usagée est transférée pneumatiquement de la station de dépoussiérage VOLKMANN en amont par transport sous vide dans un tuyau jusqu’à la station de préparation de la poudre où elle est stockée dans une trémie. Dans cette station, toutes les étapes du processus de préparation, y compris le mélange avec la poudre métallique vierge, se déroulent automatiquement.
La poudre métallique finie est versée dans un cylindre d’alimentation, scellée par un couvercle, chargée automatiquement et transportée par un module de transfert (GTAS / AGV) jusqu’à la station suivante.
Dans cette usine prototype, seul le remplissage avec de la poudre vierge est encore effectué manuellement. La nouvelle poudre est extraite sous vide des bouteilles à large col à l’aide d’une lance d’aspiration et transportée vers le conteneur de stockage par un convoyeur à vide. Dans les futures lignes de production, cette étape pourra également être automatisée.
Le haut degré d’automatisation de la station de préparation des poudres protège le personnel de l’exposition directe aux poudres et poussières métalliques. Les étapes de travail manuel avec EPI complet sont largement éliminées. La préparation de la poudre s’effectue dans des conteneurs scellés et le transport de la poudre en pression négative empêche les poussières de s’échapper.
Meilleure qualité des composants grâce à la poudre métallique séchée
La station de recyclage des poudres VOLKMANN peut faire encore plus : elle sèche également la poudre métallique. Dans le cadre du projet de recherche IDAM, le séchage n’était pas prévu au départ. Au lieu de cela, la poudre métallique devait être protégée de l’oxydation par un gaz inerte. Cependant, des recherches ultérieures menées par le Fraunhofer-ILT (Institut de technologie laser, Aix-la-Chapelle, Allemagne, https://www.ilt.fraunhofer.de/en.html) ont montré que l’utilisation d’un gaz inerte lors de la manipulation de la poudre métallique n’entraînait pas d’amélioration significative de la qualité des composants.
Parallèlement, il a été prouvé que l’humidité contenue dans la poudre métallique a une influence considérable sur le résultat de l’impression. Une poudre métallique humide a de mauvaises propriétés d’écoulement et des imperfections peuvent donc se produire dans le lit de poudre lorsqu’une nouvelle couche de poudre est appliquée. Dans le cas de certains métaux et alliages (l’aluminium, par exemple), l’eau liée crée également des pores dans le composant pendant l’impression.
La cause de l’humidité des poudres métalliques réside dans les surfaces souvent très hydrophiles des métaux. La fine poudre métallique présente une grande surface et peut donc adsorber une grande quantité d’eau provenant de l’environnement. Il suffit de quelques minutes d’exposition pour que la poudre métallique absorbe suffisamment de vapeur d’eau de l’air ou d’une autre atmosphère gazeuse pour avoir un impact sur le résultat de l’impression. Même si l’on utilise des gaz inertes tels que l’azote, il convient de noter que certaines sources de gaz ont une teneur en humidité trop élevée, ce qui peut encore compromettre la qualité de la poudre métallique.
Des études ont également montré que le séchage peut restaurer les propriétés d’origine de la poudre métallique. Le séchage sous vide est particulièrement bien adapté à cette fin : il peut être mis en œuvre très facilement, dans un espace réduit, et est très efficace. En outre, cette technologie ne nécessite pas de source de chaleur, ce qui est un grand avantage pour les poussières métalliques potentiellement explosives. Il est possible d’obtenir une faible teneur en humidité résiduelle constante, même en cas de variations importantes de la teneur en humidité initiale de la poudre fournie. Le séchage sous vide peut également être utilisé pour les poudres métalliques vierges afin d’éliminer toute humidité qui aurait pu être absorbée dans la chaîne logistique.
Le séchage sous vide peut facilement être associé à un système de transport sous vide. Dans la ligne de démonstration de BMW, le séchage sous vide a été intégré dans la station centrale de préparation de la poudre, le processus de séchage ayant lieu après le criblage et le mélange avec la poudre vierge.
L’élimination de l’utilisation de gaz inerte dans la manipulation des poudres permet de réaliser des économies considérables, tant au niveau de l’équipement technique que des coûts d’exploitation. Le séchage sous vide peut être mis en œuvre de manière plus rentable qu’un système utilisant un gaz inerte et l’équipement de manutention de gaz inerte associé. Dans le cas de l’usine de préparation des poudres de BMW, l’utilisation du séchage sous vide a permis d’économiser environ 30 % des coûts d’investissement initialement prévus.
Préparation centrale de poudre pour plusieurs imprimantes 3D
La station de recyclage des poudres a une capacité suffisante pour répondre aux besoins de préparation des poudres de quatre imprimantes 3D ou plus. Elle peut également être combinée à une station de dépouillement automatique, créant ainsi une solution très économique pour le déballage et le dépouillement automatiques des travaux de construction et la préparation de la poudre qui s’ensuit.
À court terme, le transport des cadres de construction et des conteneurs de poudre entre les imprimantes 3D et une station centrale de dépowdering et de recyclage de la poudre peut être effectué manuellement à l’aide d’un équipement de manutention de palettes. À l’avenir, les véhicules guidés entièrement automatisés (AGV) et la distribution automatique de poudre métallique aux imprimantes 3D par transport sous vide à travers un réseau de tuyauterie deviendront plus courants dans la fabrication additive.
1 Plus d’informations sur le projet IDAM :