Metaalpoeder voor 3D printen is duur, en tijdens een printopdracht blijft een grote hoeveelheid poeder ongebruikt. Voor hergebruik moeten de gesmolten poederagglomeraten echter eerst gescheiden worden. Als onderdeel van het IDAM-onderzoeksproject 1) heeft VOLKMANN hiervoor een poederrecyclingstation ontwikkeld en geïntegreerd in een volledig geautomatiseerd 3D-print-, uitpak- en poederrecyclingproces bij BMW AG.
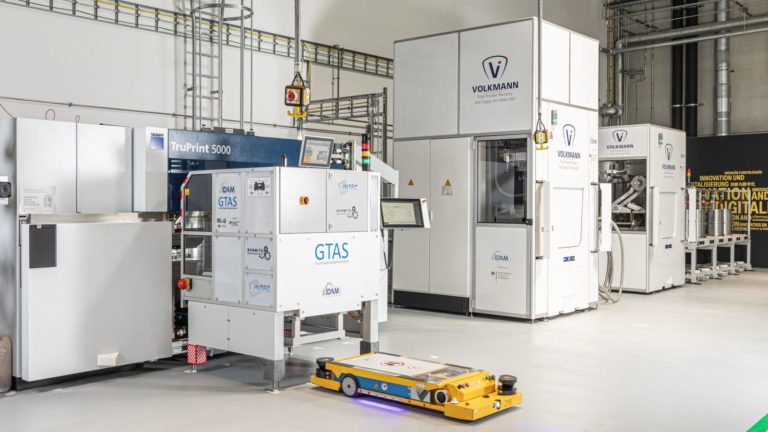
Industrieel 3D printen met metaalpoeders levert – naast de gewenste onderdelen – ook veel kleine agglomeraten van gesmolten poederdeeltjes op. In het gebruikte poeder kunnen ook gebroken draagstructuren worden aangetroffen. Dergelijke deeltjesagglomeraten en vreemde lichamen moeten op betrouwbare wijze worden verwijderd voordat het poeder weer in een printproces wordt ingevoerd.
Het gerecycleerde poeder wordt gewoonlijk gemengd met nieuw poeder. De hoeveelheid nieuw poeder compenseert de hoeveelheid die eerder in de bedrukte componenten is verwerkt. De mengverhouding tussen nieuw en gerecycleerd poeder kan de kwaliteit van de componenten beïnvloeden, reden waarom productontwikkeling en kwaliteitsborging vaak strenge specificaties opleggen. Bovendien moet worden gezorgd voor een homogene menging.
Het IDAM-project (Industrialization and Digitalization of Additive Manufacturing) werd gefinancierd door het Duitse ministerie van Onderwijs en Onderzoek (BMBF). De demonstratielijn van het IDAM-onderzoeksproject is een digitaal genetwerkte, volledig geautomatiseerde 3D-printproductielijn voor serieproductie in de automobielsector. Onder leiding van de BMW Group namen van 2019 tot 2022 in totaal 12 bedrijven en onderzoeksinstellingen deel aan het project, waaronder VOLKMANN GmbH. Er werden succesvolle praktijkproeven uitgevoerd met een demonstratielijn bij BMW AG (München, Duitsland) en met een tweede lijn bij GKN Additive (Bonn, Duitsland). De voorbereiding van gebruikt metaalpoeder en het mengen met nieuw poeder werd in de demonstratielijn bij BMW AG verzorgd door een centraal poederrecyclingstation. Bij GKN werd de poederrecycling uitgevoerd door een PowTReX-systeem van VOLKMANN.
Het centrale poederrecyclingstation bij BMW is ontwikkeld en gebouwd door VOLKMANN, waarbij waardevolle ervaringen met het PowTReX-poederrecyclingsysteem zijn verwerkt. Bovendien biedt het station capaciteit voor het afzonderlijk bufferen van zowel gebruikt als nieuw poeder en voor het mengen van deze metaalpoeders in een door de gebruiker gespecificeerde verhouding. Het station zorgt ook voor het drogen van het metaalpoeder – daarover later meer.
De zeer hoge automatiseringsgraad van de IDAM demonstratielijn is ook terug te vinden in het poederrecyclingstation. Het gebruikte metaalpoeder wordt pneumatisch overgebracht van het upstream VOLKMANN depowderstation door een vacuümtransport via een buis naar het poederbereidingsstation waar het wordt gebufferd in een trechter. Ook binnen het station verlopen alle processtappen voor de voorbereiding, inclusief het mengen met nieuw metaalpoeder, automatisch.
Het afgewerkte metaalpoeder wordt gevuld in een toevoercilinder, afgesloten met een deksel, automatisch geladen op en getransporteerd door een transfermodule (GTAS / AGV) naar het volgende station.
Alleen het vullen met nieuw poeder gebeurt in deze prototype-installatie nog handmatig. Nieuw poeder wordt met een zuiglans uit flessen met brede hals gehaald en via een vacuümtransportband naar de opslagcontainer getransporteerd. In toekomstige productielijnen kan ook deze werkstap worden geautomatiseerd.
De hoge mate van automatisering in het poederbereidingsstation beschermt het bedienend personeel tegen directe blootstelling aan metaalpoeders en stof. Handmatige werkstappen met volledige PBM’s worden grotendeels geëlimineerd. De poederbereiding vindt plaats in afgesloten containers en het poedertransport onder negatieve druk voorkomt het ontsnappen van stof.
Hogere componentkwaliteit door gedroogd metaalpoeder
Het VOLKMANN-poederrecyclingstation kan nog meer – het droogt het metaalpoeder ook. In het IDAM-onderzoeksproject was het drogen echter niet van meet af aan gepland. In plaats daarvan moest het metaalpoeder met een inert gas tegen oxidatie worden beschermd. Latere onderzoeken door het Fraunhofer-ILT (Instituut voor Lasertechnologie, Aken, Duitsland, https://www.ilt.fraunhofer.de/en.html) toonden echter aan dat het gebruik van inert gas bij de behandeling van metaalpoeder niet leidt tot een significante verbetering van de kwaliteit van de componenten.
Tegelijkertijd werd aangetoond dat vocht in het metaalpoeder een aanzienlijke invloed heeft op het drukresultaat. Nat metaalpoeder heeft slechte vloei-eigenschappen, en daarom kunnen er bij het aanbrengen van een nieuwe poederlaag onvolkomenheden in het poederbed ontstaan. Bij sommige metalen en legeringen – bv. aluminium – zorgt het gebonden water tijdens het drukken ook voor poriën in het onderdeel.
De oorzaak van metaalpoedervocht ligt in de vaak zeer hydrofiele oppervlakken van metalen. Het fijne metaalpoeder heeft een groot oppervlak en kan daardoor een grote hoeveelheid water uit de omgeving adsorberen. Het duurt slechts enkele minuten voordat het metaalpoeder voldoende waterdamp uit de lucht of een andere gasatmosfeer heeft geadsorbeerd om het afdrukresultaat te beïnvloeden. Zelfs bij gebruik van inerte gassen, zoals stikstof, dient te worden opgemerkt dat sommige gasvoorraden een te hoog vochtgehalte hebben, waardoor de kwaliteit van het metaalpoeder toch kan worden aangetast.
Studies hebben ook aangetoond dat het drogen de oorspronkelijke eigenschappen van het metaalpoeder kan herstellen. Vacuümdrogen is hiervoor bijzonder geschikt: het kan zeer gemakkelijk en ruimtebesparend worden toegepast en is zeer efficiënt. Bovendien is voor deze technologie geen warmtebron nodig, wat een groot voordeel is met betrekking tot het potentieel explosieve metaalstof. Een constant laag restvochtgehalte kan worden bereikt, zelfs bij grote variaties in het oorspronkelijke vochtgehalte van het geleverde poeder. Vacuümdroging kan ook worden gebruikt voor nieuw metaalpoeder om eventueel in de logistieke keten opgenomen vocht te verwijderen.
Vacuümdroging kan gemakkelijk worden gecombineerd met een vacuümtransportsysteem. In de BMW demonstratielijn was het vacuümdrogen geïntegreerd in het centrale poederbereidingsstation, waarbij het droogproces plaatsvond na het zeven en mengen met nieuw poeder.
Door het gebruik van inert gas bij de poederbehandeling af te schaffen kan aanzienlijk worden bespaard – zowel op de technische uitrusting als op de bedrijfskosten. Vacuümdrogen kan kosteneffectiever worden uitgevoerd dan een systeem met inert gas en de bijbehorende apparatuur voor het hanteren van inert gas. In het geval van de poedervoorbereidingsinstallatie bij BMW kon door het gebruik van vacuümdroging ongeveer 30% van de oorspronkelijk begrote investeringskosten worden bespaard.
Centrale poederbereiding voor meerdere 3D-printers
Het poederrecyclingstation heeft voldoende capaciteit voor de poederbereiding voor vier of meer 3D-printers. Dit kan ook worden gecombineerd met een automatisch depowderstation, waardoor een zeer economische oplossing ontstaat voor het automatisch uitpakken en depoweren van bouwopdrachten en de daaropvolgende poederbereiding.
Op korte termijn kan het transport van de bouwframes en poedercontainers tussen de 3D-printers en een centraal depowering- en poederrecyclingstation manueel gebeuren met behulp van palletverwerkingsapparatuur. In de toekomst zullen volledig geautomatiseerde geleide voertuigen (AGV’s) en automatische distributie van metaalpoeder naar de 3D-printers door vacuümtransport via een leidingnetwerk steeds gebruikelijker worden bij additieve fabricage.
¹Verder nieuws over het IDAM-project: