Stations for dumping and emptying bags, sacks etc.
The bag dumping and feeding station of the RNT series enables efficient unloading of bulk materials from bags, sacks, small containers and bins. The powder, granulate or bulk material is emptied into the hopper and sucked into the conveyor line from there. It can then be transported by vacuum conveying through a pipeline over a distance of up to 100 metres to a process system (e.g. mixer, reactor, filling machine, etc.) or into a container or silo. Gravimetric emptying into a system directly below the emptying station is also possible.
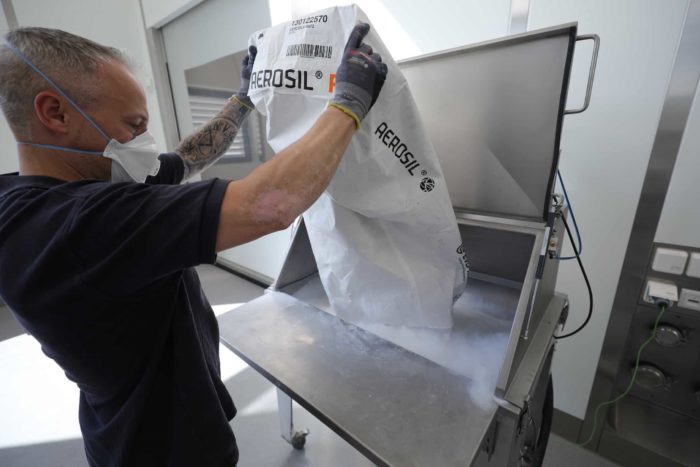
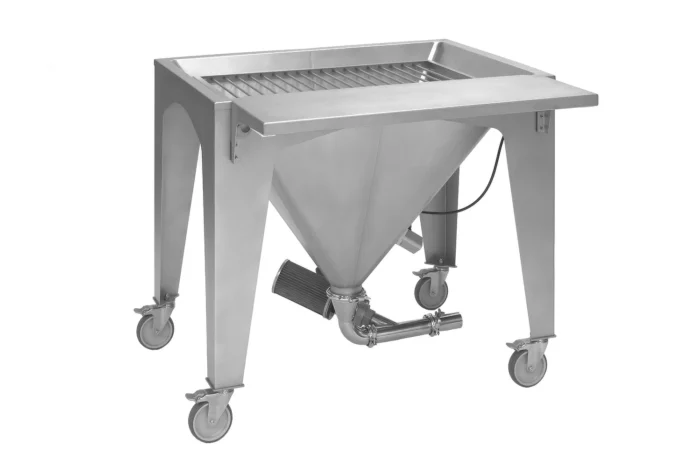
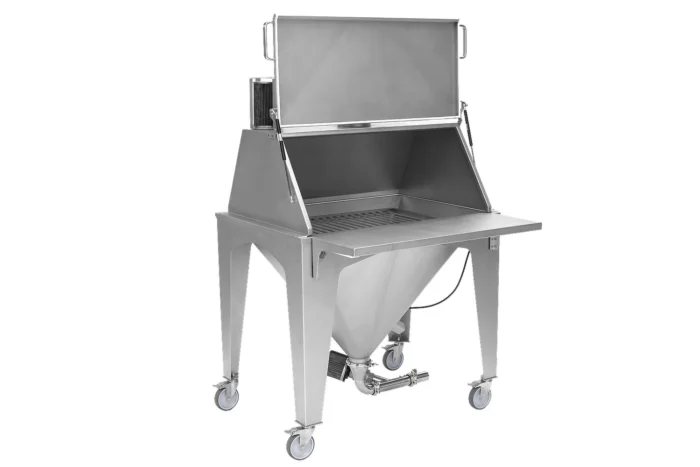
The RNT dumping station is suitable for feeding powder, granulate and other bulk materials from a wide variety of containers: from plastic or paper bags, cartons, boxes, drums and barrels, containers or other packaging. However, the ergonomic aspects of handling, such as the size and weight of the containers, must also be taken into account.
Product dumping and emptying stations are known by numerous synonyms in the industry, including. bag dump station, bag dumping station, manual dumping station, small bag dump station, manual bag dump station, bag intake station, sack discharge station, or hopper.
The design of the RNT 180 takes ergonomic aspects into account and enables user-friendly operation and cleaning.
The modular design of the RNT 180 dumping station
The modular system of the RNT 180 allows the product feeding and emptying station to be customised with numerous functions and details:
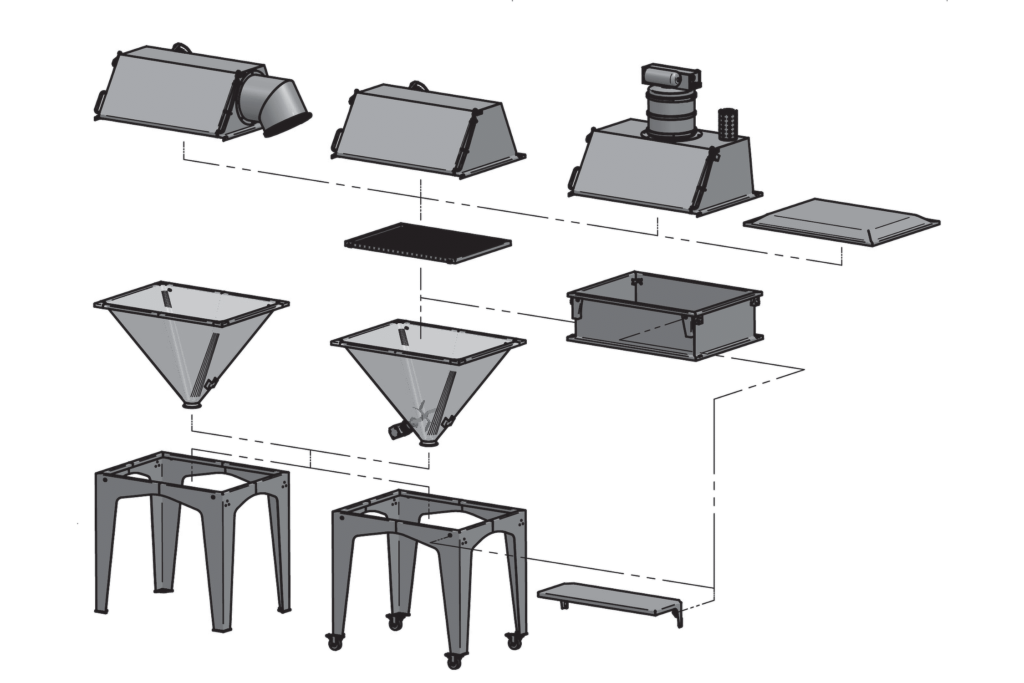
Materials and surfaces
The components that come into contact with the product are made of stainless steel 316L (1.4404 or 1.4435). The frame is made of stainless steel 304 (1.4301). The seal between the bonnet and the hopper is made of silicone foam, and EPDM foam can also be used as an option.
The surfaces of the stainless steel components are glass bead blasted. The surfaces in contact with the product can also be ground or polished at the customer’s request.
Protection against dust and hazardous substances
When emptying sacks or bags, the release of dust must often be minimised or avoided altogether. Different requirements can be defined here: from preventing contamination of the environment to maximising protection of the operator from hazardous dust. Protecting the powder or bulk material from contamination from the environment or from cross-contamination can also be a requirement. The modular emptying station RNT 180 can fulfil this range of different requirements thanks to its numerous expansion options:
You can find more information about containment solutions here.
We are also happy to design customised solutions for you. The following pictures show some examples:
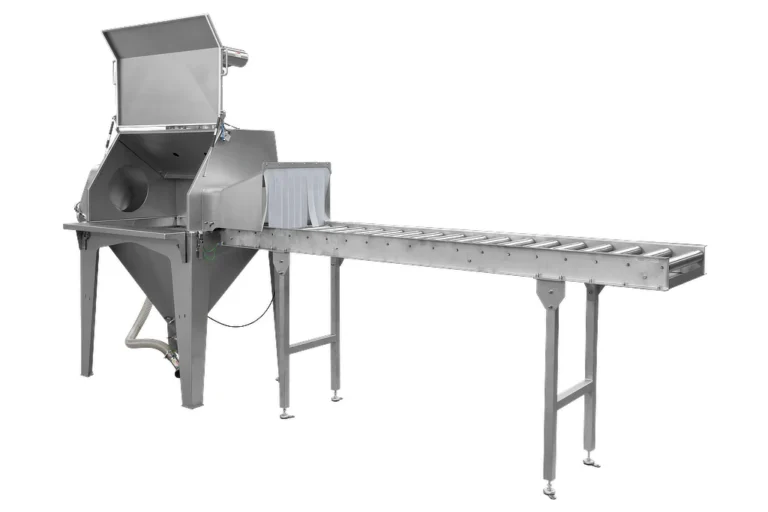
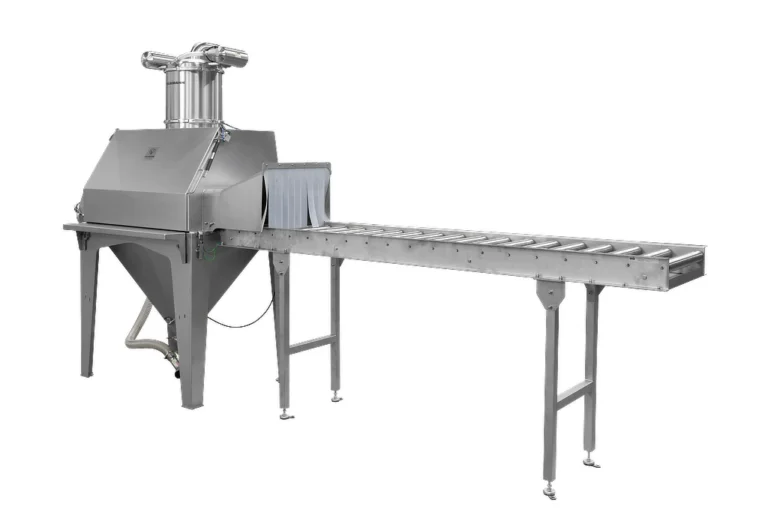
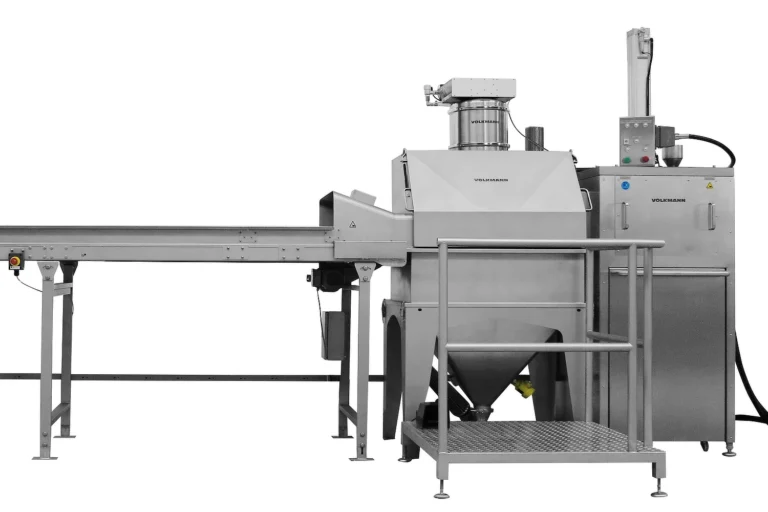
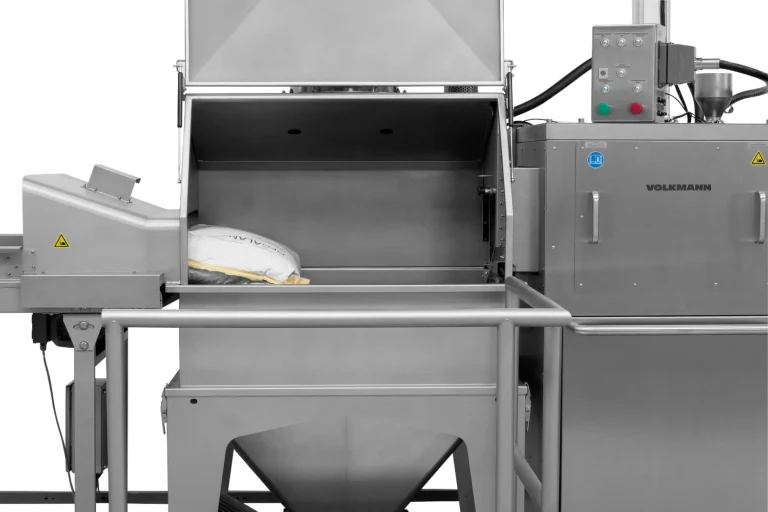
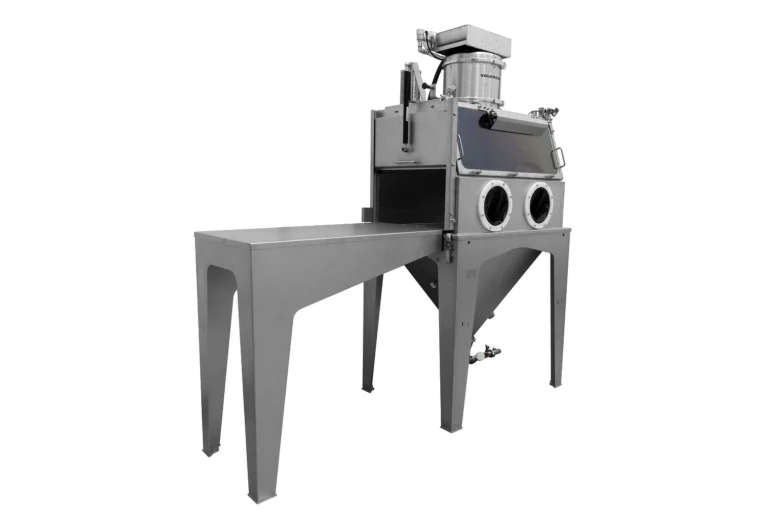
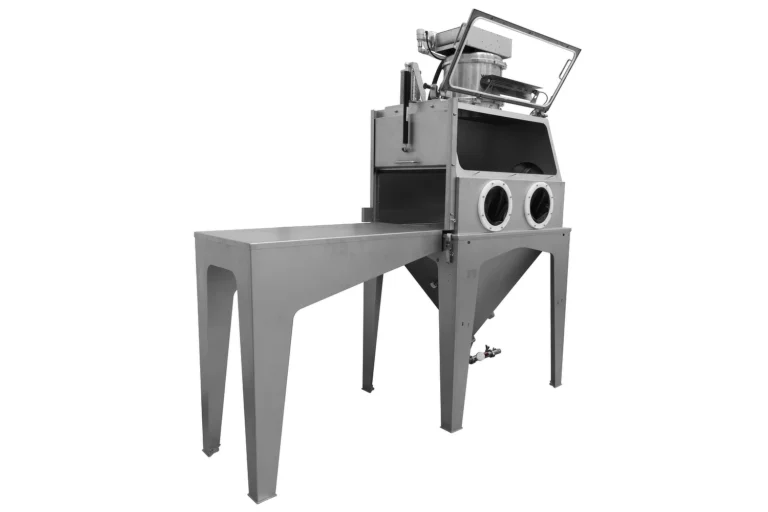
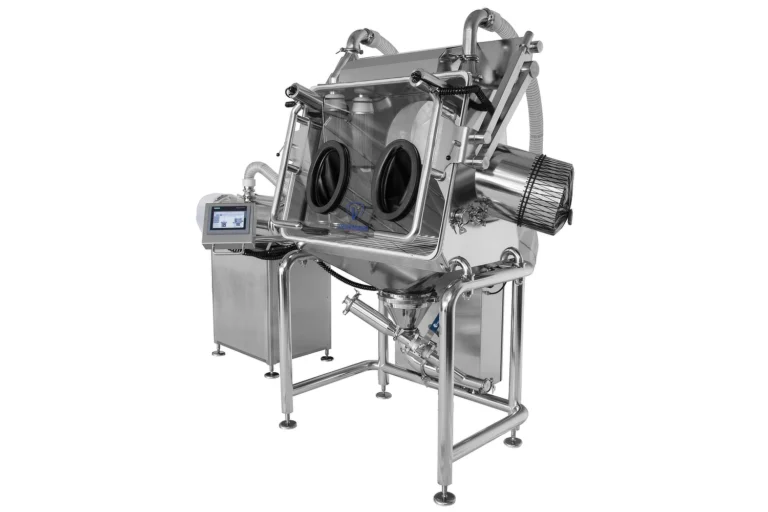
Reduction of material loss
An optional dust hood with integrated aspiration including filter not only protects the operator from dust, but also reduces material loss. The dust is first separated at the filter while the dust extraction system is running. Closing the hood lid automatically stops the aspiration and starts the filter cleaning process at the same time. An abrupt blast of compressed air from the inside of the filter blows off the dust accumulated on the outside of the filter. The dust falls into the feed hopper filled with material and is thus available for further processing. By returning the dust to the product, the operator also saves the effort and costs of disposing of the dust.
Easy cleaning
The RNT hopper is designed with large bends in all corners. This enables residue-free cleaning, which fulfils the requirements of the food industry, among others.
The dust hood can be quickly attached to and removed from the RNT hopper in just a few simple steps. Only two people are needed to lift and place the dust hood. It is fastened with clamps.
Crushing of lumps and agglomerates
A VOLKMANN lump breaker can be installed under the RNT hopper to break up lumps and agglomerates. The crusher enables lumpy material to be vacuum conveyed through a small-diameter pipe with a correspondingly low air volume, resulting in lower energy consumption.
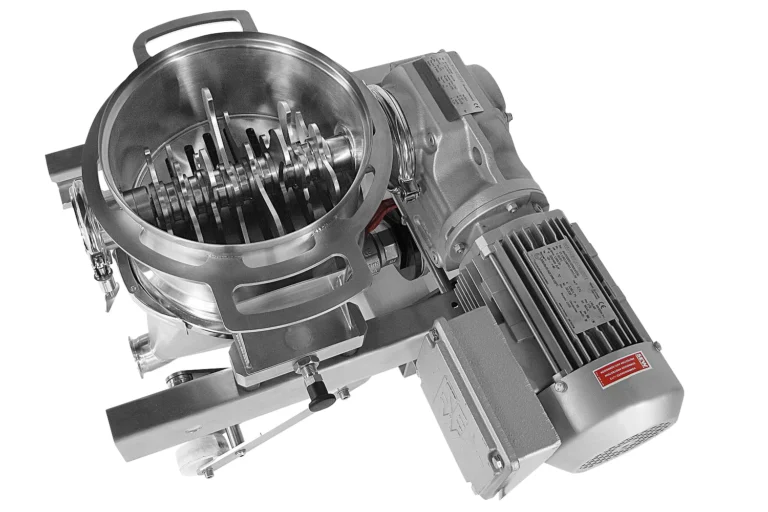
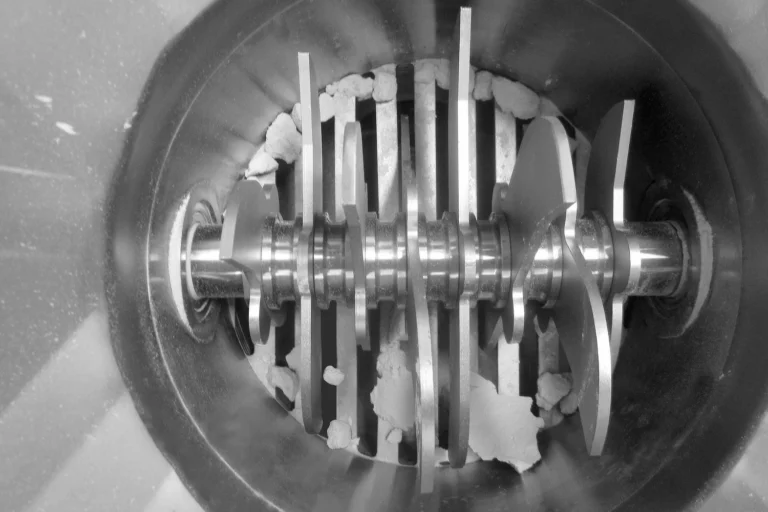
Conveying under nitrogen
If required, the materials to be conveyed can be extracted and transported under nitrogen or another inert gas. To protect the operator and the environment from displacement of the air or oxygen in the working area, the emptying station must be equipped with a lockable hood. Further protective measures are required, such as sensors to monitor the oxygen content in the work area.
The RNT in miniature
Occasionally, the RNT emptying station is required in a small size. A common application is the transfer of product from the product outlet of a process plant in order to transport it in-house through a pipeline by means of vacuum conveying. This may also involve retrofitting or automating an existing system in which the bulk material previously fell into a container that had to be emptied manually. The small RNT is installed in its place and connected to a vacuum conveying system.
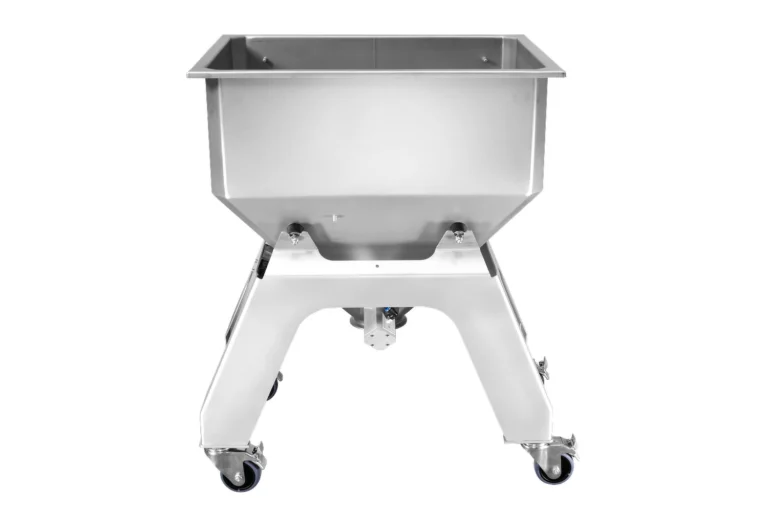
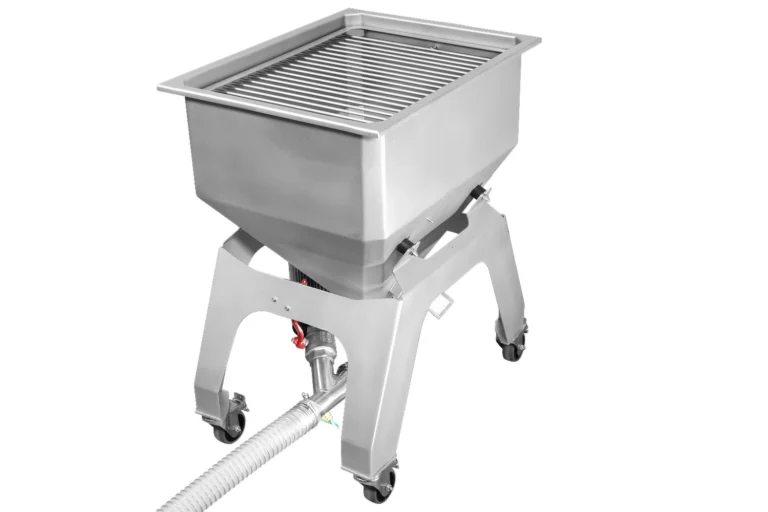
Video: A simple test setup in our test centre with an RNT 80 and a vacuum conveyor
You are currently viewing a placeholder content from Youtube. To access the actual content, click the button below. Please note that doing so will share data with third-party providers.
More Information