DPS Metal 1 – automatic unpacking and depowdering of the build job
Unpack the build job from the build frame and completely de-powder both. The DPS Metal 1 makes this possible automatically, and in a single work operation, without the requirement for an operator to perform any intermediate manual steps. The cleaning result is so good that downstream cleaning activities are usually unnecessary. During the cleaning cycle the metal powder is collected in a container for subsequent reprocessing.
The closed system protects personnel from the metal powder dust while equally protecting the metal powder from external environment contamination.
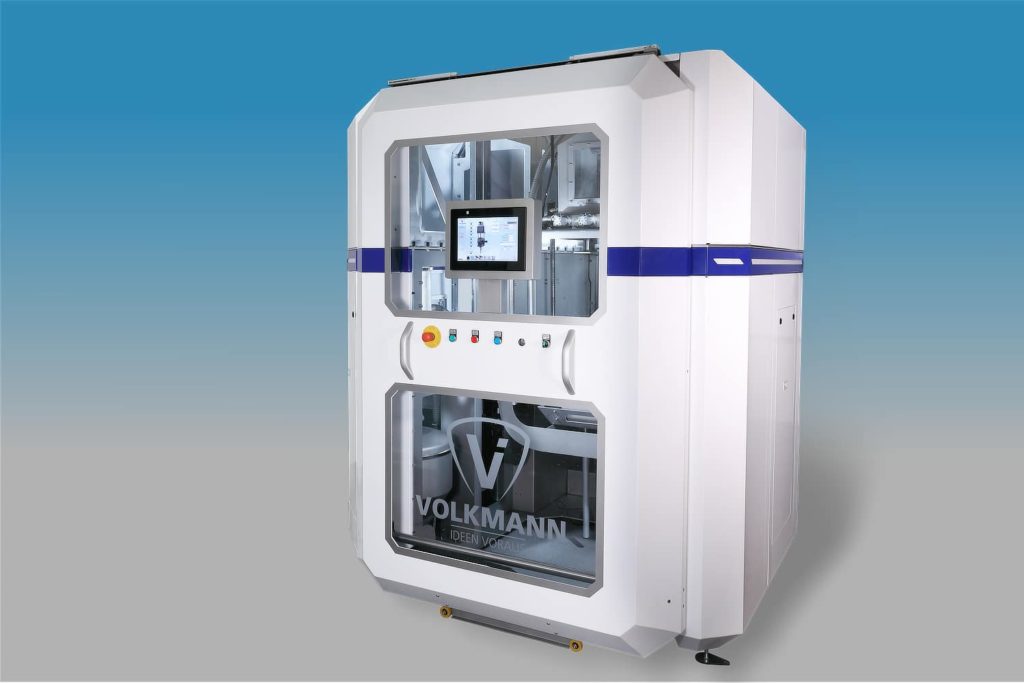
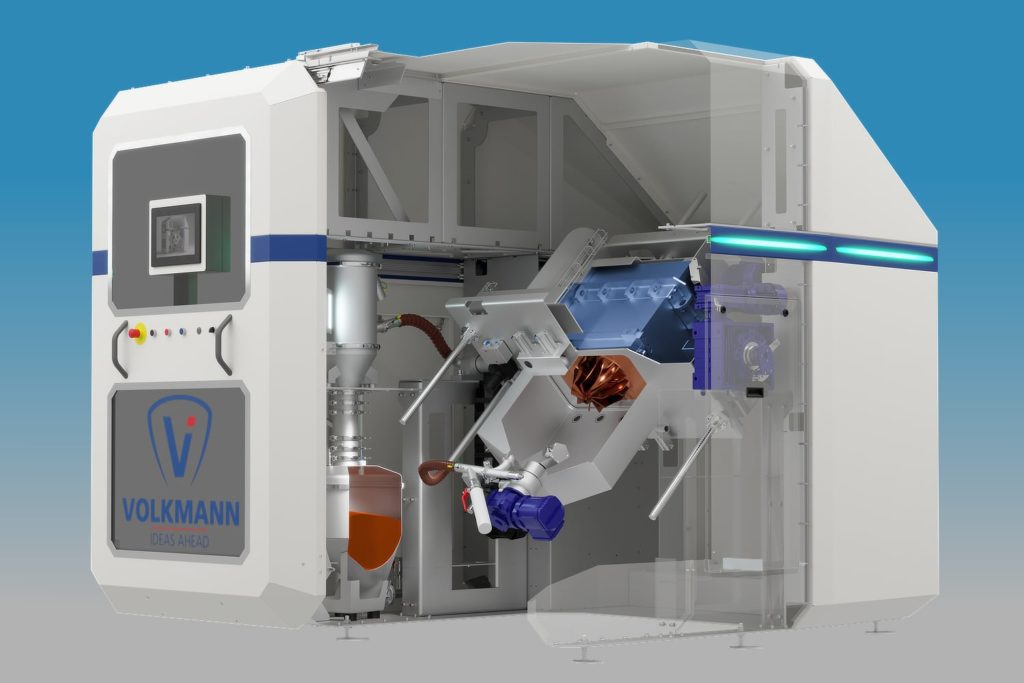
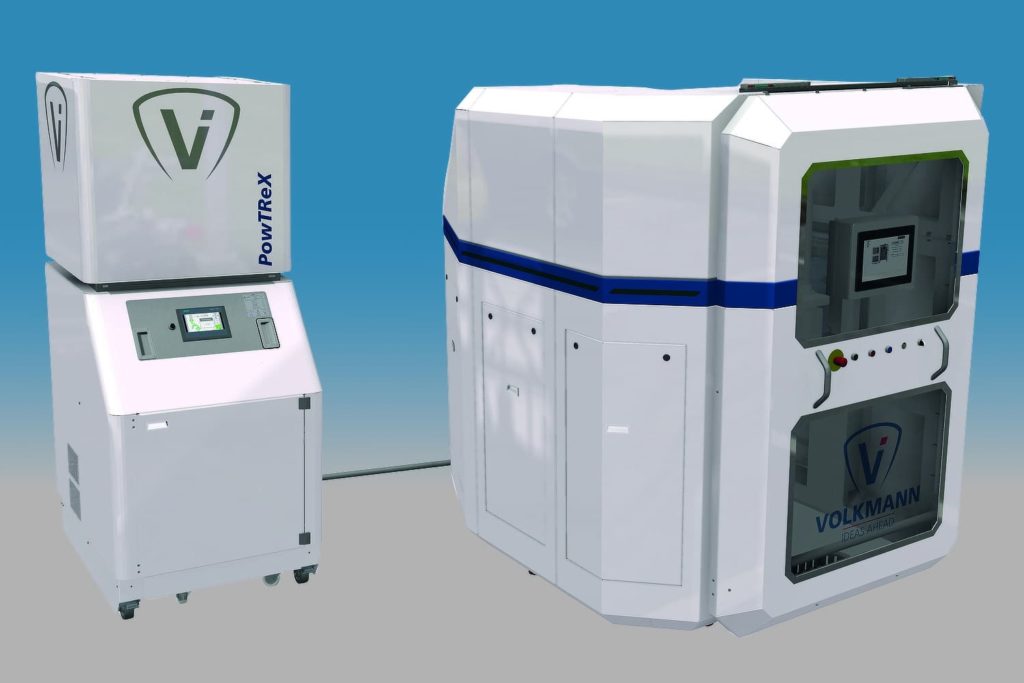
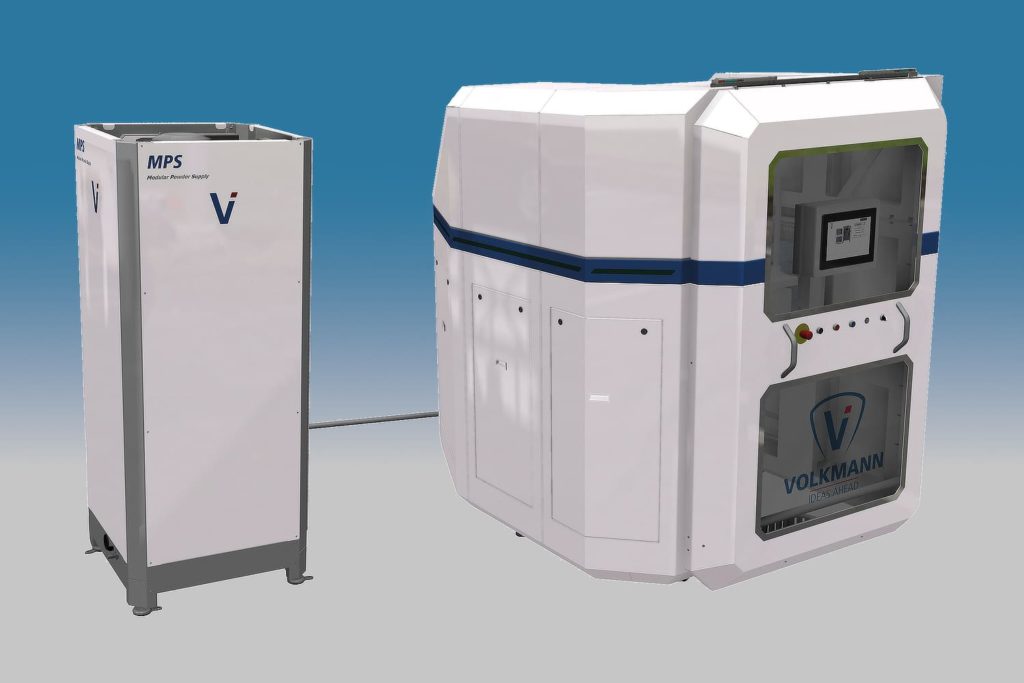
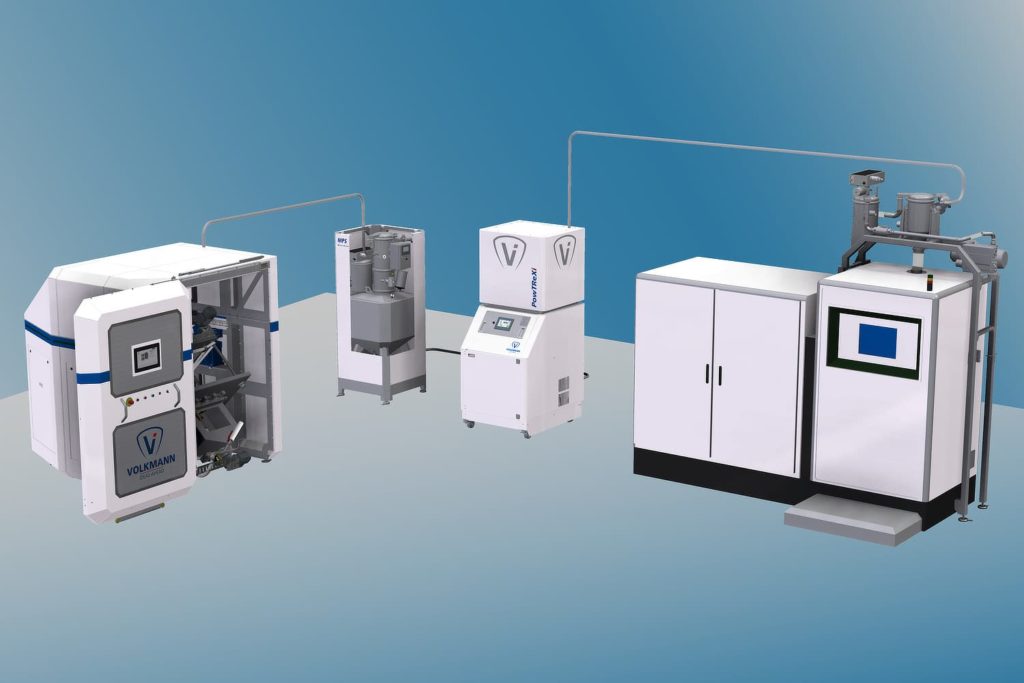
Functionality of the DPS Metal 1:
The build frame is fed directly from the 3D printer into the station with the build job together with the excess metal powder contained within it. Loading can be carried out manually (e.g. by lift truck) or using an automatic transport system.
The entire cleaning process takes place within a closed chamber either under atmospheric conditions or under inert gas. After inverting the build frame with the printed parts, cleaning nozzles use air jets (compressed air or inert gas) to remove excess powder from the components. This not only loosens the excess metal powder from the deepest crevices of the built component, but also removes the powder adhering to the build frame.
The cleaning process is further enhanced by the use of a vibrator unit. The frequency-modulating vibrations introduced into the component break up any bridges formed in the metal powder.
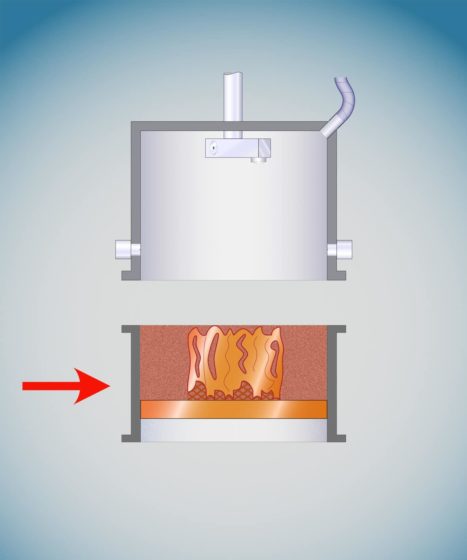
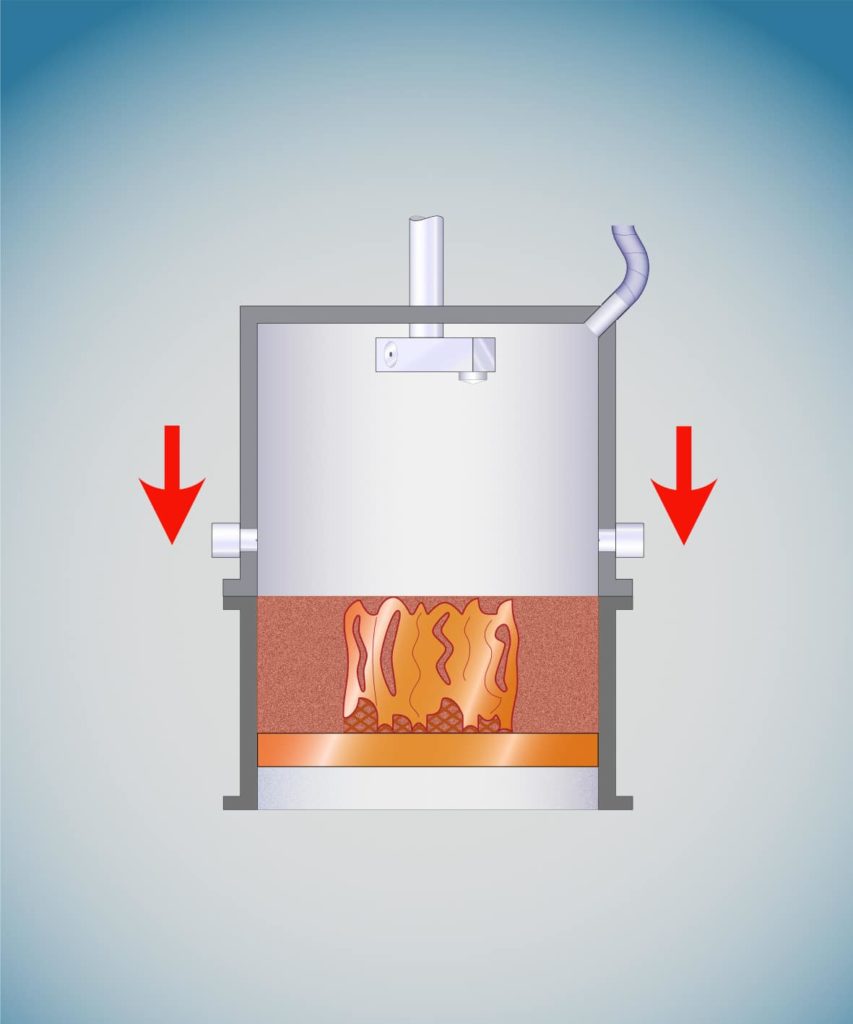

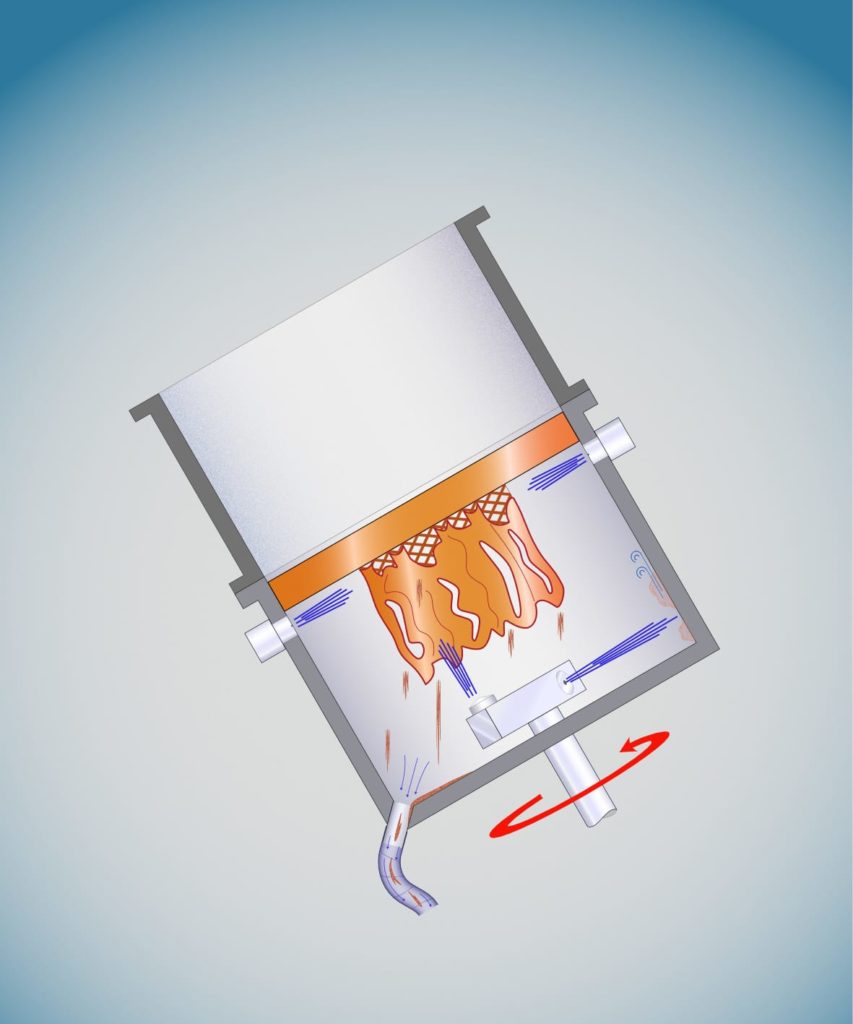
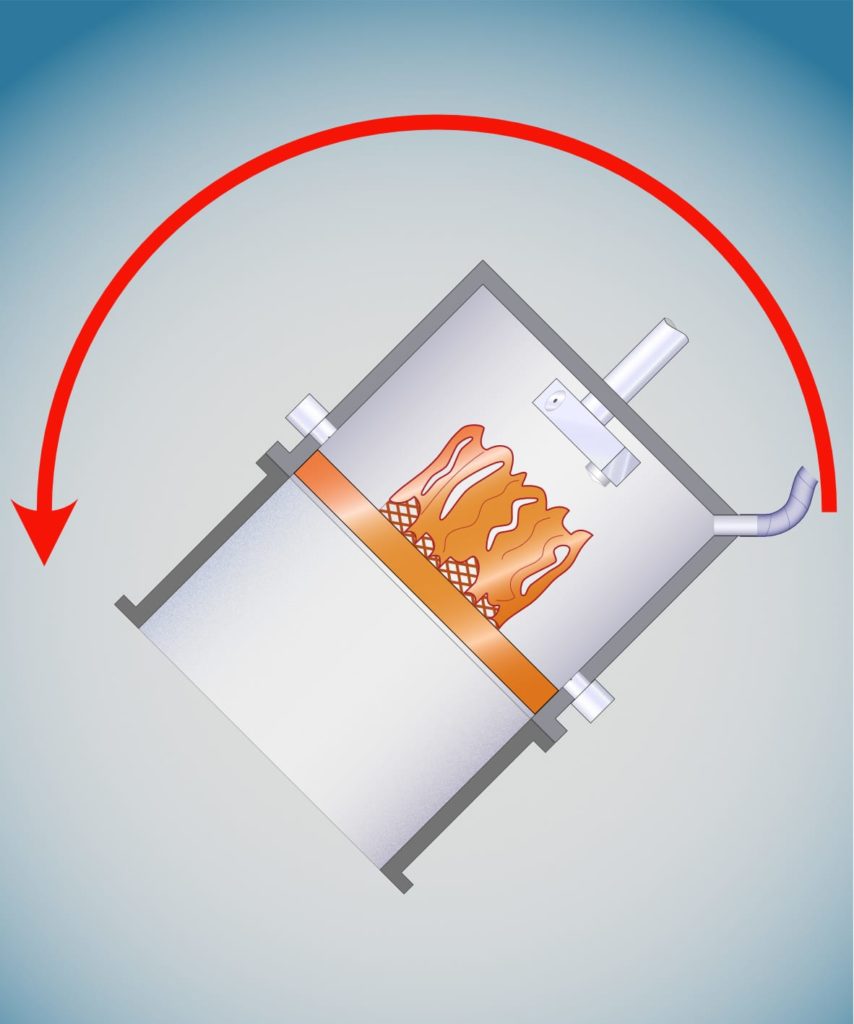
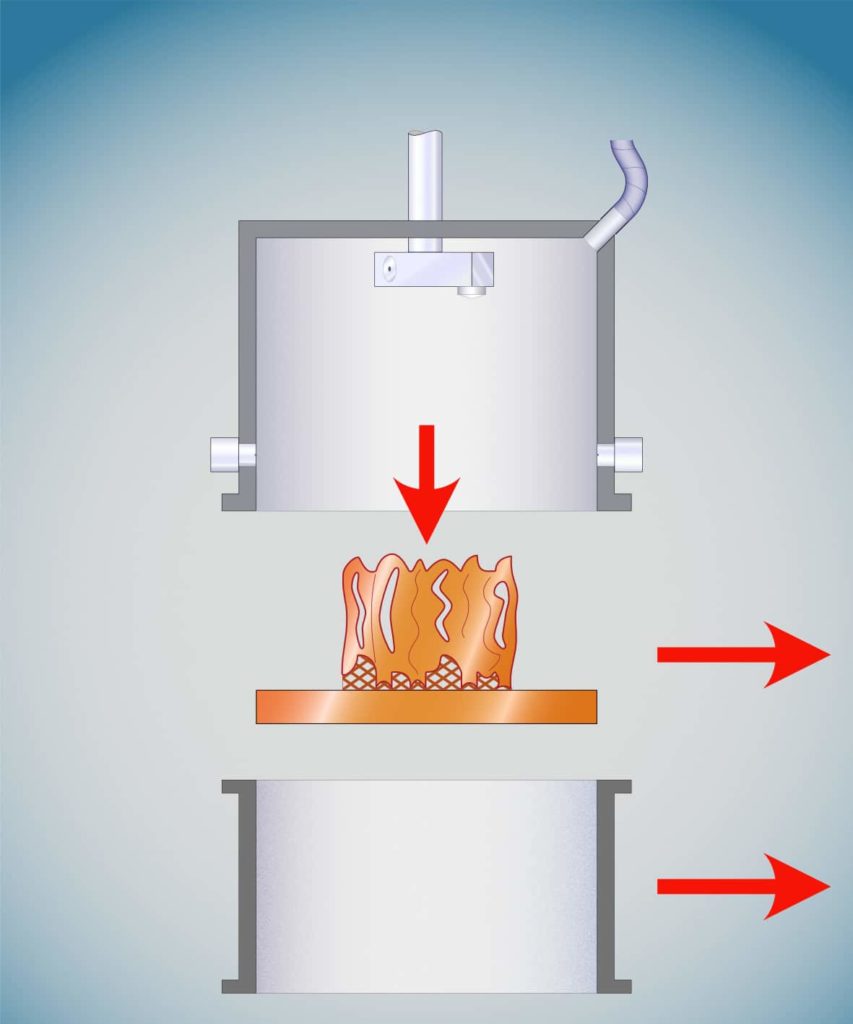
Fig.: schematic representation of the cleaning steps (build frame with build job as well as cleaning hood of the DPS Metal 1.
Optionally, in the DPS Metal 1 at the end of the cleaning process, the build job can either be removed from the build frame or left within it. Accordingly, they are subsequently unloaded from the station combined or separately. In the latter the build frame can be loaded with a new build plate in the system.
The loose metal powder is completely collected and buffered by vacuum conveying in a container integrated in the station. From there it can be conveyed, again by vacuum conveying, to a powder preparation station – e.g. a PowTReX. For a buffer volume of 250 L up to 1,000 L, the powder can be conveyed to an vHub system.
The exhaust air from the vacuum conveying system is safely discharged into the environment through a primary and secondary filter system (material with H14 classification) as standard.
Depending on the construction job geometry, a cleaning cycle usually takes between 10 and 30 minutes. The exact sequence of a cleaning cycle can be managed as a customer-specific recipe.
The DPS Metal 1 can be adapted to the different designs of the established manufacturers of 3D printers. A DPS Metal 1 is designed in each case to fit the specific dimensions and geometries of the build frame of a 3D printer manufacturer.
DPS in the IDAM research project
The DPS was developed by Volkmann as a project partner in the IDAM research project and successfully tested with two prototypes in demonstrator lines at BMW and GKN Additive.
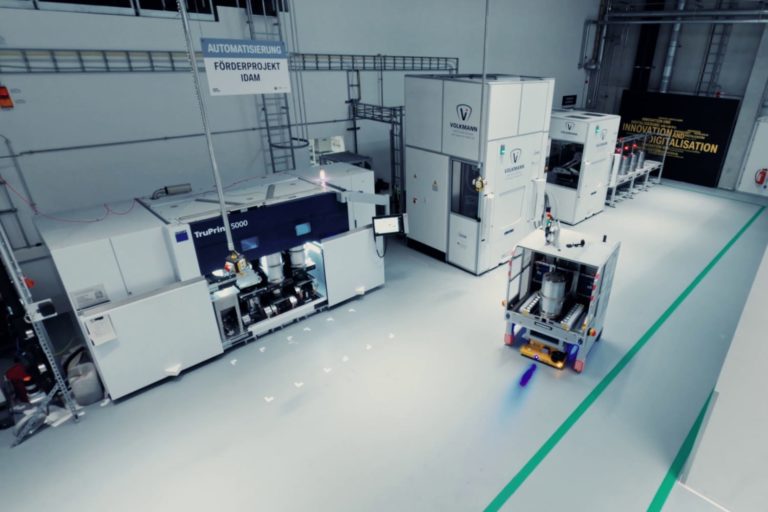
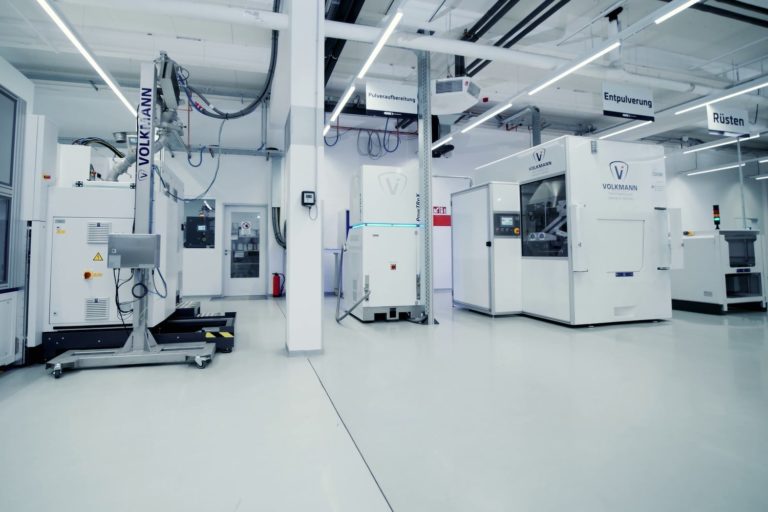
Fig: Demonstrator lines of the IDAM project, left at BMW AG, right at GKN Additive [courtesy: BMW AG and GKN Additive]
Two videos offer insights into the IDAM project and the depowdering station:
Video about the IDAM research project:
You are currently viewing a placeholder content from Youtube. To access the actual content, click the button below. Please note that doing so will share data with third-party providers.
More InformationVideo about the depowdering stations in the IDAM project:
You are currently viewing a placeholder content from Youtube. To access the actual content, click the button below. Please note that doing so will share data with third-party providers.
More Information