There is probably hardly anyone who has never used a UHU product. The glue in the black and yellow tube has become one of the best-known brand products of our time. UHU develops and produces high-quality adhesives for children and parents, but also for do-it- yourselfers and professional applications in trades and industry. The development of ever better and safer products with an eye on future generations is a challenge and commitment in one.
Cleanliness and safety
Most the products are manufactured in the industrial premises in Germany, located right at the centre of the small town of Bühl at the foot of the Black Forest. Cleanliness and safety are hence matter of course in the production. The creation of adhesives generally calls for a variety of solids and solvents, which are combined in a mixer or batching tank. To further increase the cleanliness and safety, UHU decided to use Volkmann GmbH’s INEX vacuum conveyors in 2007, and hence in favour of a sealed introduction of solids to the mixer.
What were the decisive reasons for using the INEX systems?
Volkmann had already opted for an ATEX certification of their vacuum conveyors in keeping with Directive 94/4/EC in early 2002, which generally permits them to be employed in potentially explosive, dusty atmospheres. Where potentially explosive gas atmospheres are concerned, standard vacuum conveyors are turned into a type- tested INEX system by an additional inertization using protective gas (nitrogen). This allows the safe and dust-free introduction of solids into containers that are pre-filled with solvents (zone 0). One essential element of the certified INEX vacuum conveyor system for this is the purely pneumatic control, which guarantees the reliability of the process by means of various safety queries such as “enough nitrogen provided for inertization”, for example. In addition, this INEX control unit can be directly installed in zone 1 or also be used in a mobile fashion on a driving carriage. Besides the safe introduction, this conveyance process also offers the additional advantage that dust and gas emissions are avoided, thus protecting the health of the workforce and ensuring that the production stays clean.
Process safety thanks to vapour barrier
Rising vapours and fumes can cause problems when mixers are filled, and are able to reduce the safety of the process. The shut-off flaps installed to separate the INEX vacuum conveyor from the mixer for introducing the solids into the process can be moistened by these rising vapours and fumes, leading to thick deposits of the solids and their getting stuck. Another frequent consequence is also that the filter inside the vacuum conveyor is moistened and becomes blocked. But the shut-off flap of the INEX system could be kept dry successfully by means of a nitrogen-operated vapour barrier which ensures uninterrupted and reliable operation.
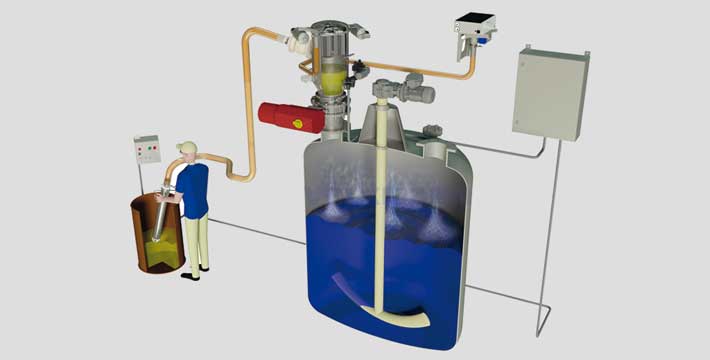
Various installation situations on site
In grown production facilities, one will find highly varied installation situations where standard systems are often unusable. Height restrictions, oblique filler pipes and already provided system components often leave little room for new plant technologies. But given the fact that the entire engineering is performed by Volkmann in-house, and thanks to the high degree of self-production, the INEX vacuum conveyors could be successfully adapted to the various local installation situations of the mixers while also providing adequate access for operability and maintenance.
There can be many reasons for using Volkmann vacuum conveyor systems, as the UHU example illustrates. But one of the most important ones is certainly the close and partnership-based cooperation without which these various customized solutions would hardly be possible.