As part of the IDAM research project¹, VOLKMANN developed a depowdering station for the total depowdering of the build frame and built components using a fully automatic process. Excellent cleaning results are achieved while the production costs are significantly reduced when compared to conventional cleaning methods.
At the conclusion of the 3D printing process is the requirement for unpacking the build. The 3D printed components, or build job, must be removed from the metal powder bed with the need for all loose metal powder particles and dust to be extracted. To the same extent, the build frame itself must also be cleaned prior to its’ next use. The unused metal powder is collected, recycled in a downstream process step, and made available for reuse in subsequent 3D printing.
In previous state of the art installations, unpacking and depowdering the printed construction job has historically involved highly manual operations. Even all prior automation concepts still necessitated individual manual work steps. As a result, the operators required personal protection from harmful metal powders and dusts further leading to correspondingly high production costs.Â
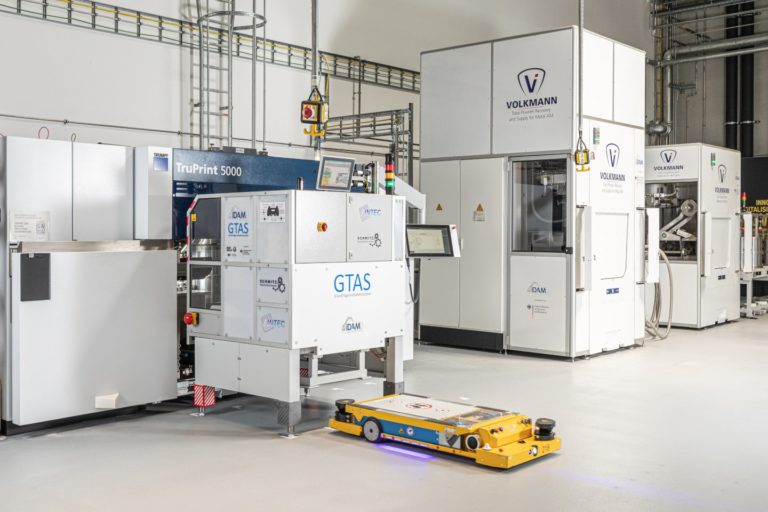
In the IDAM research project, complete and automated de-powdering was required and realized for the first time. The IDAM project (Industrialization and Digitalization of Additive Manufacturing) was funded by the German Federal Ministry of Education and Research (BMBF). Under the leadership of the BMW Group, a total of 12 companies and research institutes participated in the project from 2019 to 2022. Included in the 12 was VOLKMANN GmbH who designed and supplied two demonstrator systems for unpacking and de-powdering; one at BMW AG (Munich / Oberschleissheim) and a second at GKN Additive (Bonn). Successful practical trials were carried out.
In the IDAM demonstrator lines, after the end of 3D printing, the build frame (or build cylinder), including the build job it contains as well as the unused metal powder, are automatically loaded from the 3D printer into the GTAS transfer module. An AGV (automated guided vehicle) then moves the GTAS to the de-powdering station where the build frame is automatically loaded.
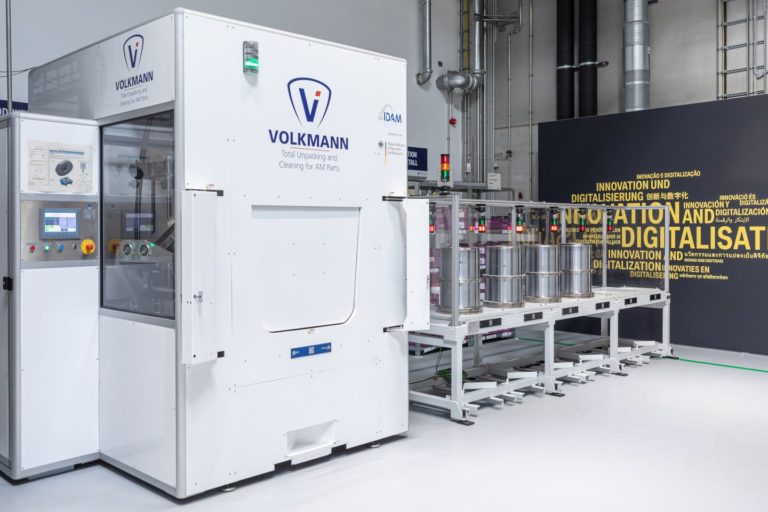
In the fully automatic depowdering station, the entire cleaning process occurs in a closed and sealed cleaning chamber. Initially, the build frame, with the build job contained therein, is inverted allowing the majority of the surplus metal powder to discharge under gravity. The real challenge; however, is the removal of the remaining powder trapped within the crevices, undercuts and cavities of the build job. This is achieved by using specially designed rotating compressed air nozzles. The nozzles generate intense air flow around and throughout the build job from all directions combining with the suction air flow of the integrated vacuum conveyor. In addition, a vibrator excites the build plate, and thus also the 3D printed parts. The vibration loosens the bridging behavior of the metal powder, particularly in the narrow channels such as the support structures, ensuring the metal powder is removed. This not only removes the metal powder from the remaining crevices of the build component, but also removes the adhering dust from the surfaces of the build job, the build frame and the cleaning hood itself.
The depowdering station then removes the build job from the build frame and transfers each individually to the GTAS transfer module for the subsequent process steps.Â
The metal powders and metal dusts collected during cleaning are stored in the station and then conveyed through a hose or tube to a VOLKMANN powder handling station for recycling.
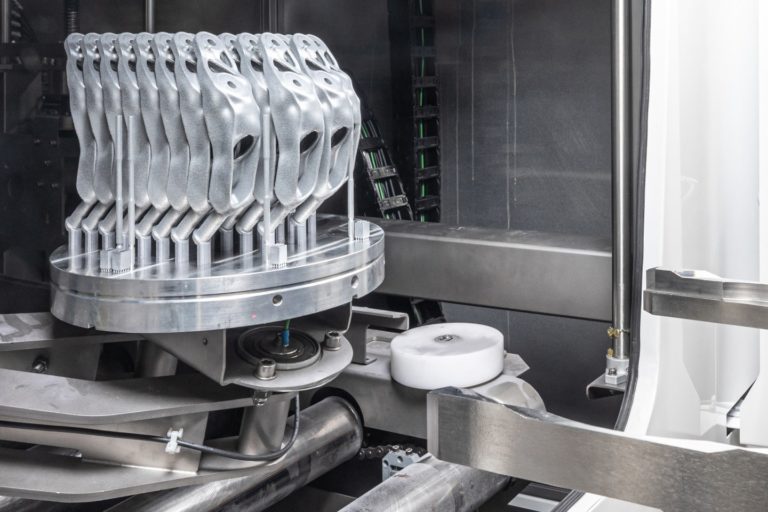
The demonstrator line at BMW AG uses build cylinders from TRUMPF (TruPrint 5000), while the line at GKN Additive uses build frames from EOS (M300-4). By making corresponding modifications to the cleaning hood, the depowdering stations were adapted to suit the different container types.
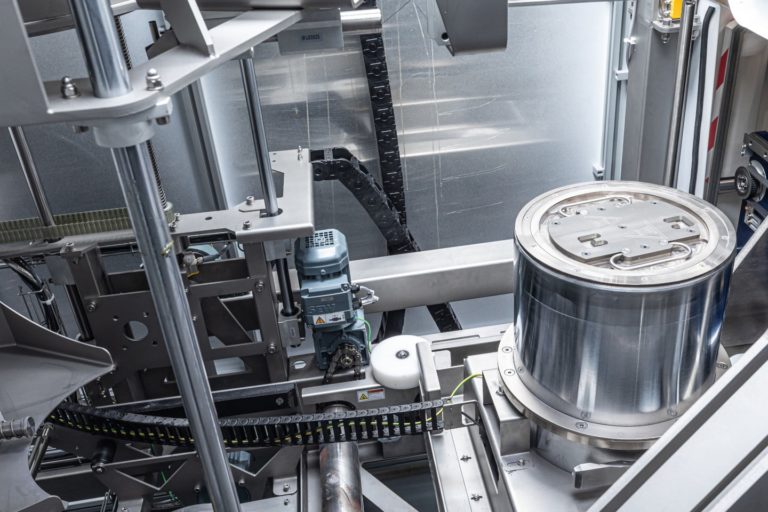
Both the personnel and the production environment must be safely protected from metal dusts. Therefore, in the IDAM demonstrator lines, the build frames/build cylinders of the 3D printers are automatically closed with a cover before any transfer between the stations. In the depowdering station, the air extracted by the integrated vacuum conveyor is further cleaned by a HEPA filter.
VOLKMANN GmbH customers are expressing a high level of interest in the depowdering station implemented in the IDAM project leading to the expectation that this concept will soon become a common procedure in the everyday volume production by additive manufacturing.
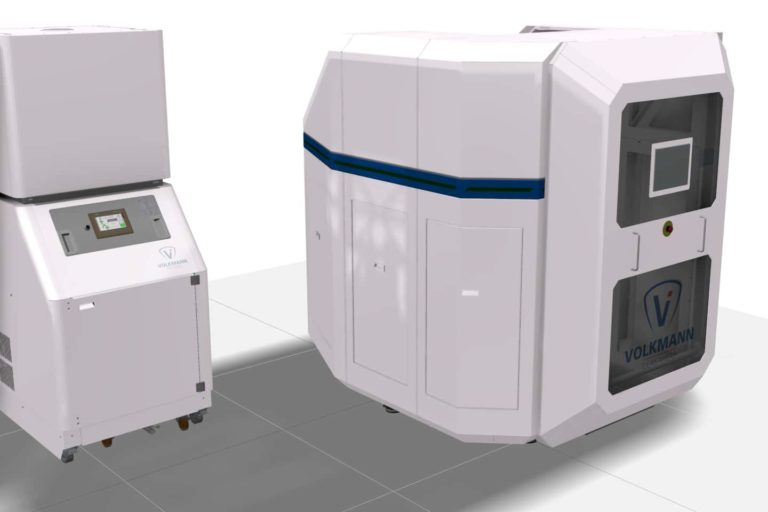
¹ Further news about the IDAM project: