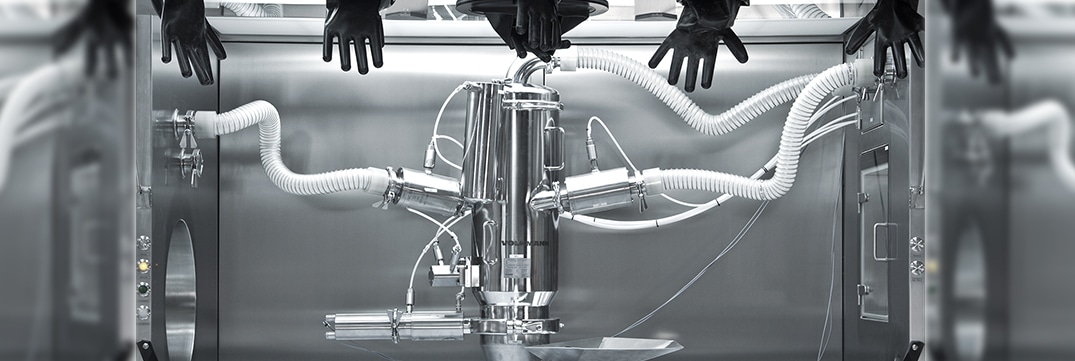
The requirements and demands for suitable containment solutions have greatly increased in industry in recent years. For example, more potent and more effective active ingredients are constantly being produced in the pharmaceutical industry which require closed and dust-free processes. The handling of these dangerous substances demands a high level of safety to protect the employees, the product and the production environment. In the past, the employees had often been only equipped with a full-body protection suit and more or less worked in an open process. In doing so, the risk of contamination of the product and the work environment was very high. Today the process, depending on the application, is either integrated in an isolator (protective cover) or executed as a sealed and closed process facility to ensure a dust-free and safe work environment. Vacuum conveyor systems are especially suited for assignments in high containment due to the procedures in negative pressure ranges.
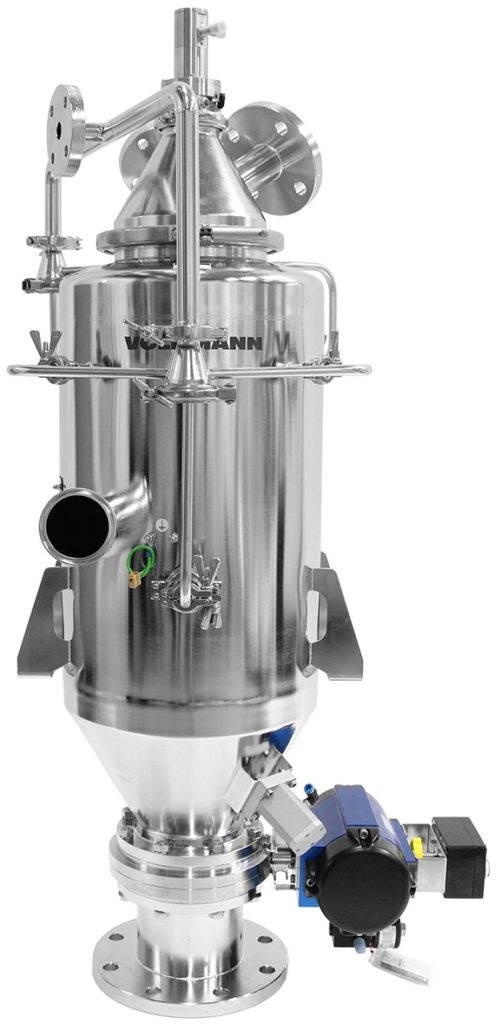
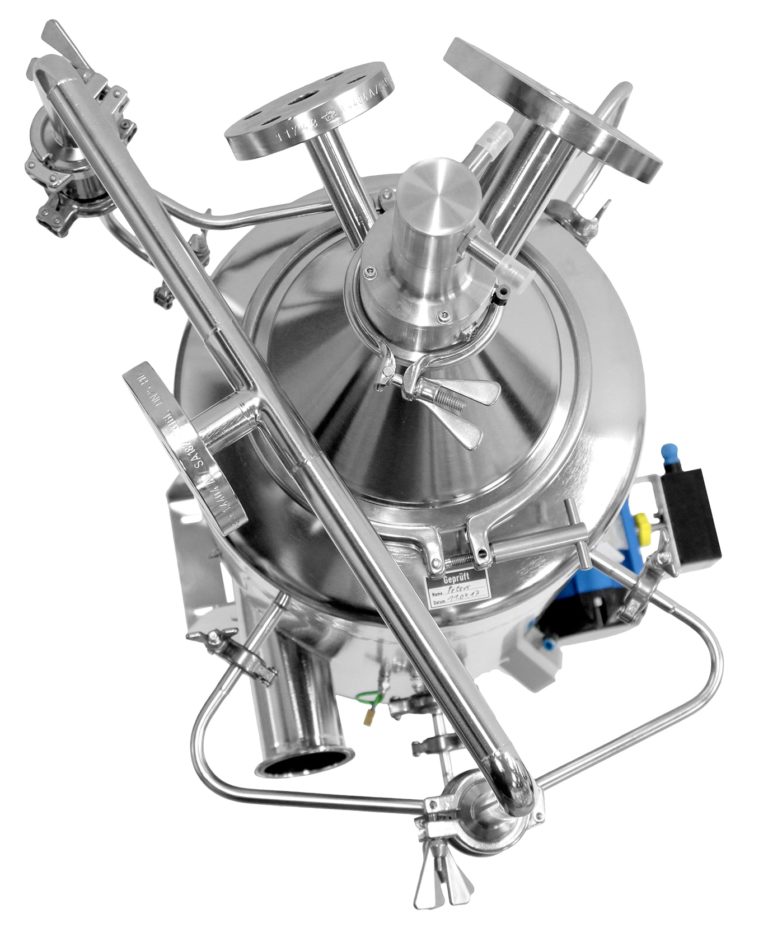
It Depends on the Product
The requirements for containment are always product specific and must therefore be redefined for every product. Internationally as well as in general use, the terms OEL level or OEB class are used. In the case of OEL (Occupational
Exposure Level), the focus is on the maximum concentration levels permissible in a work environment. The specific OEL value and the product features (granule size and fluidity) play a significant role here in the design of the process unit. Not every containment system is suitable for every product.
Pressure from the Authorities
Other reasons for a growing demand of containment solutions are guidelines and regulations. The REACH Regulation established a chemical guideline for all of Europe that addresses a classification of hazardous and harmful substances. REACH stands for the Registration, Evaluation, Authorization and Restriction of Chemicals. The manufacturers of chemicals and the operations of processing plants are then obligated to disclose information about how hazardous or harmful a substance is and how the user should handle it in order to protect oneself.
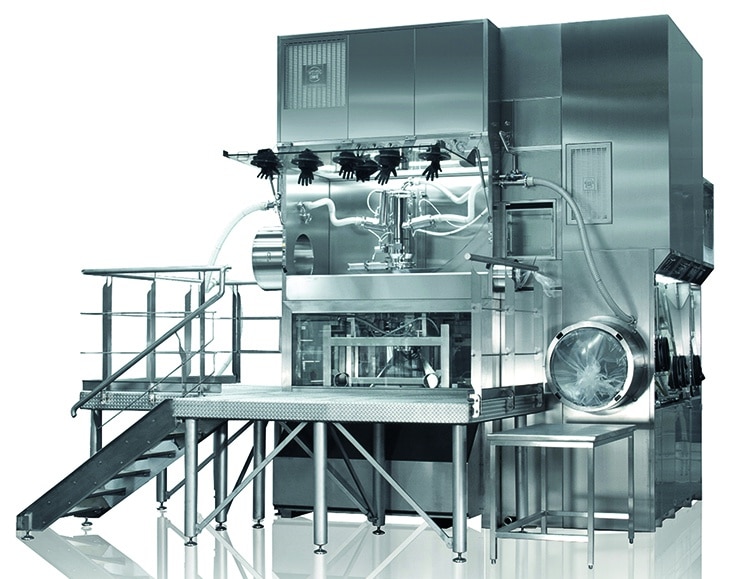
In a high containment project, a closer and more open cooperation than usual between the company and users involved is required. For a pharmaceutical manufacturer in Switzerland, a PPC250 type vacuum conveyor was integrated in a special containment facility (Weiss Pharmatechnik GmbH) for the filling and transferring of high potency ingredients and various excipients. The objective of this project was to develop a closed facility concept that fulfils the required OEB class 4.
Double flap system for filling the products into the containers.
The transferring and filling facility essentially consists of a transfer compartment for the purpose of the products, an upstream material lock for the insertion of the container, a filling compartment with integrated PPC 250 as well as a container station with a docked double flap system for filling the containers with the product.
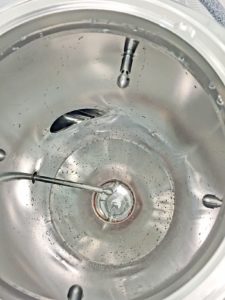
The containers with the ingredients are first positioned over a material lock in the transfer compartment. Using the integrated gloves in the transfer compartment, the operator opens the containers and, by means of a manual suction lance connected to the PPC 250, sucks the material found in the adjacent filling compartment. From here, the transferred ingredient is emptied into the docked container via the double flap. The container is situated on a weighing system to determine the required amounts. The emptied containers are fed through the side walls via foil ports. The harmless pharmaceutical excipients are sucked in through a second suction lance directly from the supply container outside the unit. The entire containment system fulfilled the required OEB 4 demands during the filling and the subsequent WIP cleaning and is suitable for dust-explosive powder (conforms to ATEX).
Design Limit 1 µg/m3 (OEB 5)
A classic application of vacuum conveyors in the pharmaceutical industry is the unloading of fluid bed granulators and the subsequent filling of a downstream sieve mill. One of our pharmaceutical clients asked if our PPC vacuum conveyor is suitable for a design limit of 1 μg/m3. In order to be able to form an idea of these minimal dust concentrations, you can use the following example: A small grain of commercial sugar that we use in our morning coffee weighs ca. 0.6 mg. The six-hundredth portion of this sugar grain is allowed to appear in one cubic meter of air within a maximum of 8 hours so that a risk for the employees does not exist.
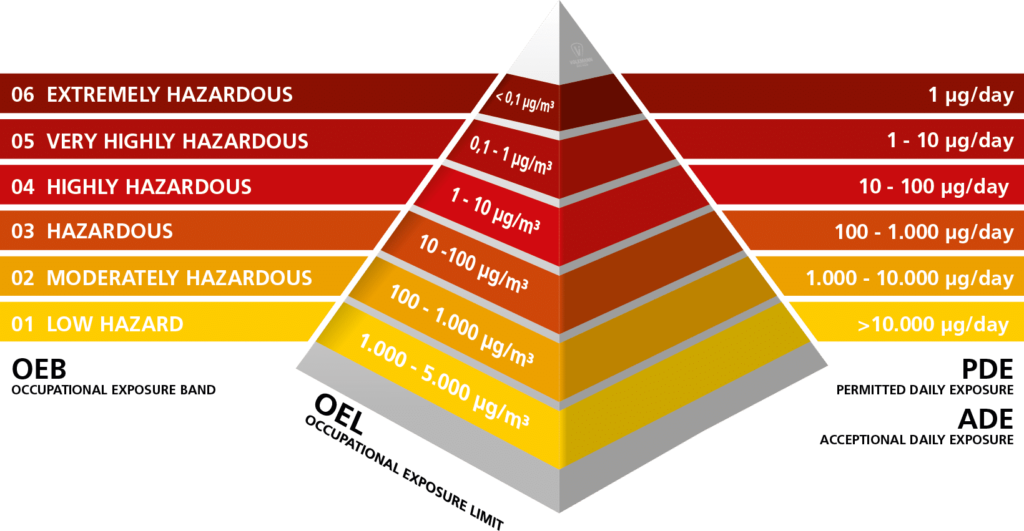
It is not enough to be sealed
A sealed and closed process was required for this high containment assignment that should forgo the protective cover in the form of an isolator. In order to be able to fulfil these high demands, the hygienic PPC 350 vacuum conveyor that is free of dead space was further developed and augmented with a second filter level (HEPA H14) and suitable isolation valves.
However, to be sealed is only a requirement for a complete high containment system. A second essential feature is the cleanability of the entire surface in contact with the product including the ports to the other process facilities in the closed WIP (washing in place) procedure.
In the first cleaning step, the entire facility is flooded with water; this especially applies to the contaminated conveyor hoses and process lines. Wetting the surfaces that come into contact with the product first serves to pre-wash the separator tanks, filters and valves. Afterwards, the intensive cleaning begins with rotating nozzles and the repeated washing of the stainless-steel filter that is used as the primary filter here. The vacuum line after the primary filter and the second filter level (HEPA H14) could also be contaminated and is likewise cleaned. The WIP procedure executed here is very individual and depends strongly on the respective product, on the cleaning agents used and, of course, on the process.
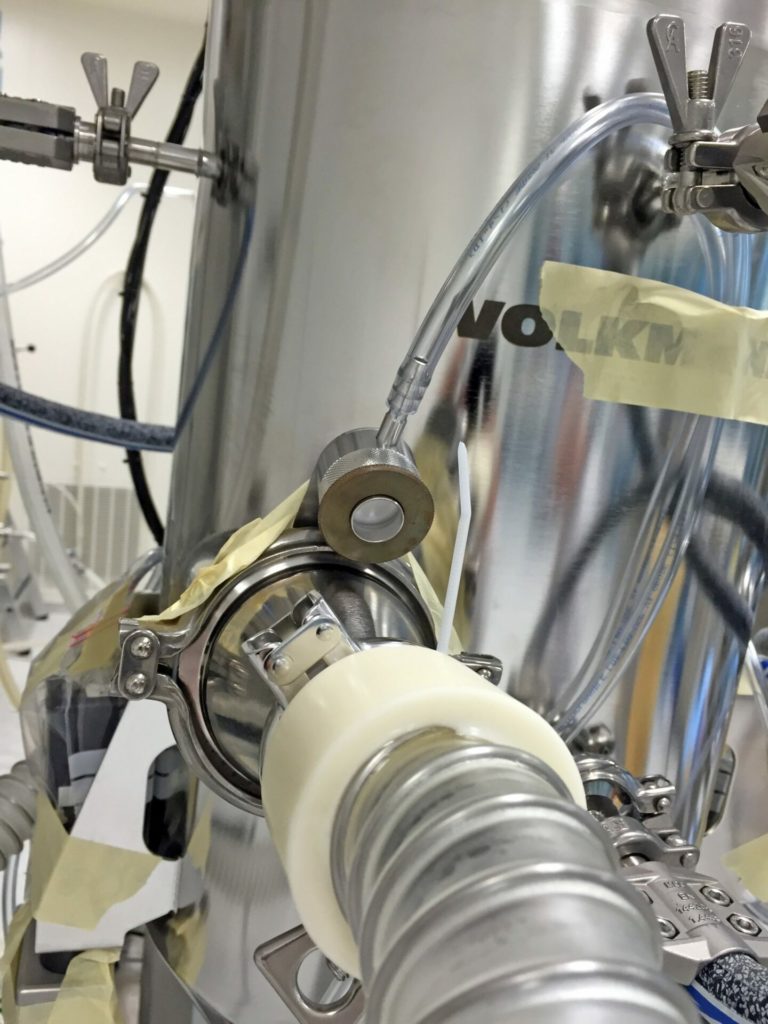
Dust Emission Measurements as Proof
Which containment level a process facility now satisfies can only be proved with a measurement of the emitted particle. In a prepared clean room, the PPC350-CIP was tested under comparable conditions as in the later production. The test material used was a very fine-grained and dusty naproxen-lactose mixture that is very well suited for such tests and is frequently used. The test material was located in a transport vessel (IBC) that was docked through a double flap system on the feed hopper. The PPC350-CIP was mobile in a frame and likewise connected with an empty IBC by a double flap.
An expert team selected several statistically process relevant measuring points for the test and placed the permitted air sensors with test filters for these measuring sequences there. These primarily record the situation in the direct surroundings of the measurement points while the person-related measuring point displays the cumulative, average burden of the operating personnel. The operator supervised the process during the measuring and changed the filled and emptied IBCs here. The conveying process was performed three times for a representative result, and each individual process was measured separately. The measurement itself was completed by special compact filter systems that were perfused by a defined amount of air with the aid of a small vacuum generator.
The measurement of the particle concentration not only occurred during the conveyor process exclusively in the IBC change but also during the cleaning and the subsequent disassembly of the vacuum conveyor.
Conclusion:
The evaluation of the particle measurements in the laboratory yielded that the PPC350-CIP lay under the design limit of 1 μg/m3 in all three process steps and is therefore most suitable for this high containment application.
Would you like to find out more or do you have a specific task?
Our application experts will be happy to help you. Contact