In recent weeks, we have reported a lot about our solutions for additive manufacturing with metal powders, with a focus on SLM (Selective Laser Melting) processes. However, our products are also used in SBAM processes (Sinter-based Additive Manufacturing). That is why we were very happy to accept the invitation to give a presentation at the “Sinter-based Additive Manufacturing” workshop of the IFAM Institute in Bremen on 14 – 15 September 2022.
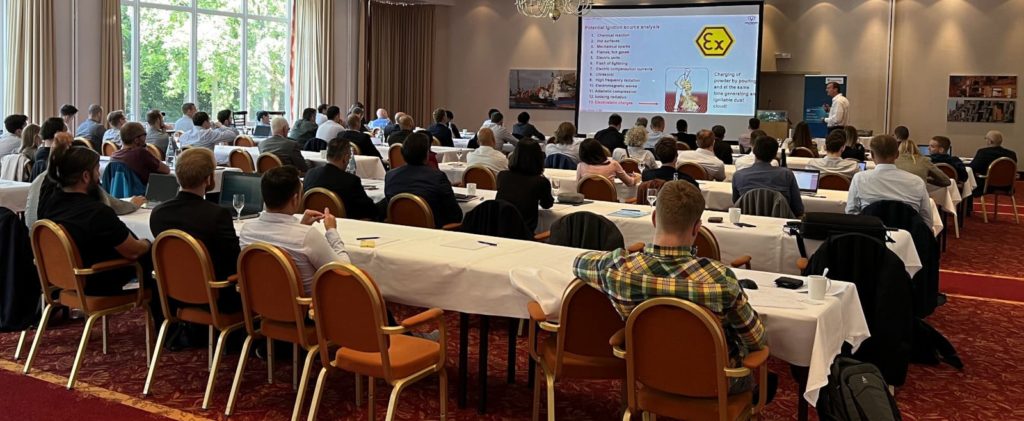
When it comes to filling 3D printers with metal powders, there are no significant differences between SLM and SBAM – vacuum conveying is a field-proven technology in both processes. Unpacking and de-powdering SBAM build jobs, on the other hand, is a particular challenge because the green bodies are very sensitive.
The preparation of the unused powder is also possible in binder jetting applications. Occasionally, users are concerned that the screening result could deteriorate due to the binder splashes that get into the powder, or that the screen could become completely clogged after some time. In practice, however, the ultrasonically excited sieving in our PowTReX systems has also proven itself in continuous use with SBAM processes.
In his presentation entitled “Smart Metal Powder Handling Solutions for Additive Manufacturing”, Thomas Ramme also addressed the question of whether vacuum conveying damages the metal powder and ultimately results in a lower quality of the printed 3D component. As part of the IDAM project, this question was investigated by the Fraunhofer-ILT (Institute for Laser Technology, Aachen, https://www.ilt.fraunhofer.de/), but no negative changes were detected. On the contrary, the powder quality can even be significantly improved during conveying and conditioning. Drying the metal powder by vacuum leads to significantly better flowability, thus to a better coating application, and ultimately to a higher component quality.
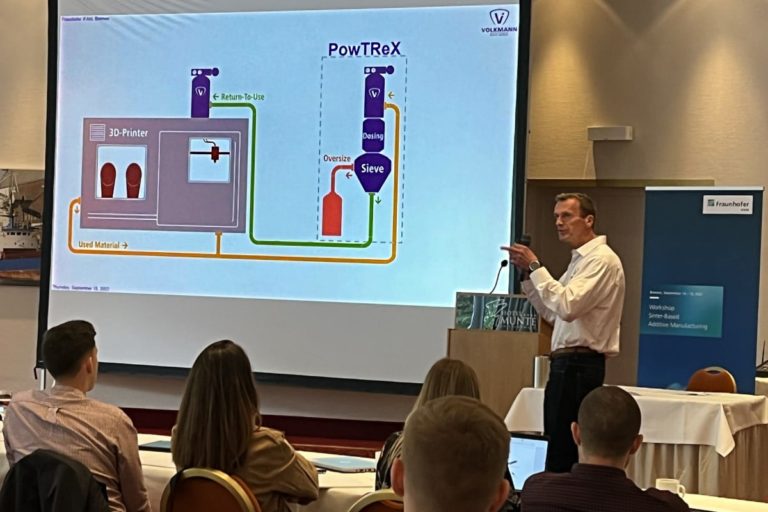
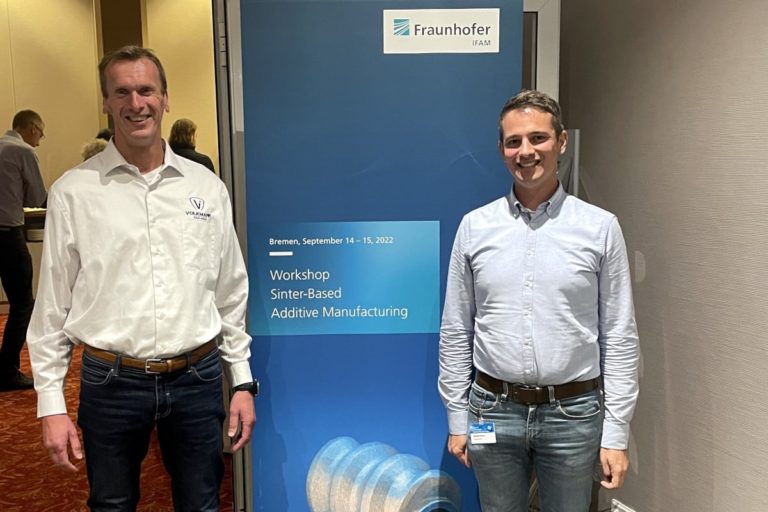
The clean and safe handling of metal powder is becoming increasingly important to users. It is equally a matter of protecting the personnel from respirable dusts as well as protecting the metal powder from contamination. Closed systems and the use of vacuum conveying are an optimal solution in many respects, as the negative pressure in the system prevents dust from escaping.
With over 80 participants, the 3rd edition of the workshop hosted by the IFAM Institute attracted a great deal of interest. We are already looking forward to the next SBAM workshop on 13-14.09.2023 in Bremen.
The IFAM Institute, with around 700 employees at 5 locations, is a research institution of the Fraunhofer-Gesellschaft (www.ifam.fraunhofer.de). Further information about the SBAM workshop can be found in the article published by IFAM:Â https://www.linkedin.com/posts/fraunhofer-ifam_sinter-additivemanufacturing-binderjetting-activity-6976495180161937409-xLiA?utm_source=share&utm_medium=member_desktop