vLoader 250: automatic filling of 3D printers with metal powder
The vLoader 250 supplies a 3D printer with metal powder automatically. The metal powder and the environment are optimally protected from each other while the continuous supply of the 3D printer is ensured in the best possible way.
With the optional vDryer module, the metal powder can also be dried. The improved flowability of the dry metal powder has a positive effect on the quality of the printed components.
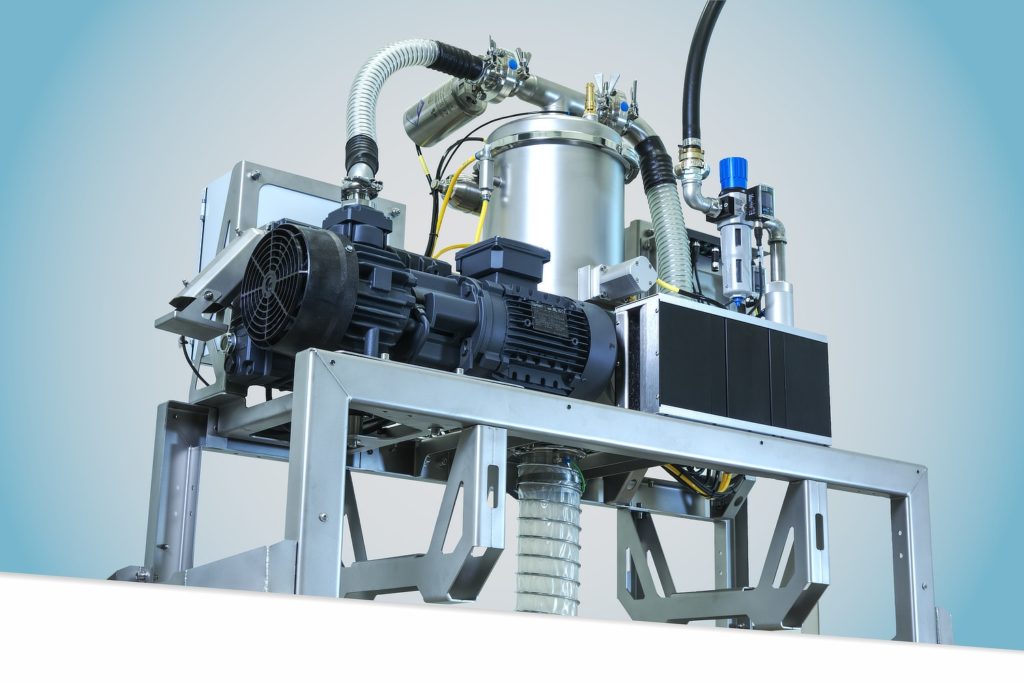
The integrated vacuum conveyor governs the conveying of the metal powder into the system. The powder is transported through a pipeline or hose up to 25 meters long and with a height difference of up to 5 meters. With an intermittent mode of operation, the vLoader first fills its buffer container, and then empties it into the powder supply of the 3D printer.
The vLoader can obtain the powder from a wide variety of sources. In a closed powder circuit, it is either a buffer reservoir (e.g. vHub 250) or a powder reprocessing system (e.g. PowTReX). But also other systems, such as a GloveBox or an IBC docking station (e.g. vDock) can be the initial material source. Manual extraction from a container is also possible.
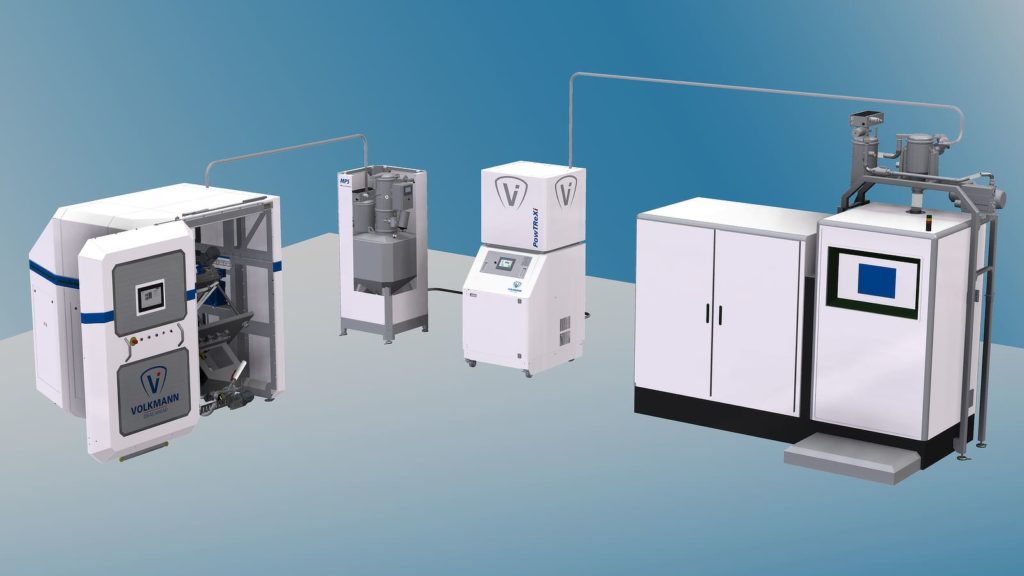
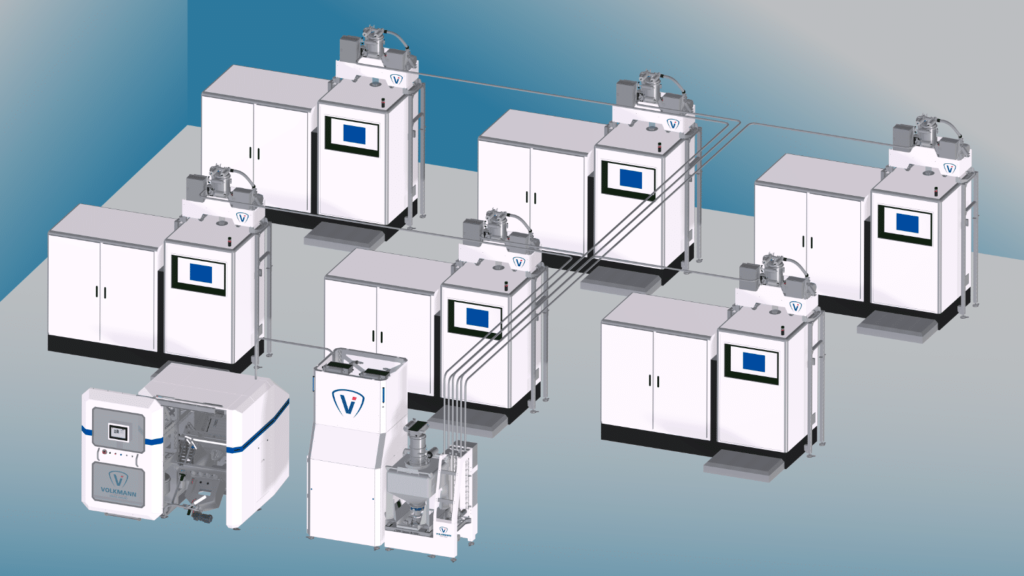
Advantages:
- Automatic filling of the printer. Manual filling operations are eliminated.
- Suitability for fully automated, unmanned production.
- A safe powder supply to the 3D printer is ensured when connected to a large supply container. The risk of interruption or suspension of the printing process is significantly reduced.
- Closed powder handling: better operator protection, and the powder cannot be contaminated.
- Space-saving installation on top of the 3D printer
The vLoader is installed on top of the 3D printer with special supports. Vibration dampers and hose sleeves decouple the devices from each other.
The vLoader is suitable for all common 3D printers with a connection point for powder filling and can replace an installed bottle filling. Retrofitting existing 3D printers with a vLoader is also possible.
vDryer: better print quality with dried metal powder
Moist metal powder can have a negative effect on the quality of printed components. It has significantly poorer flow properties, which can affect the application of new powder layers in the printer, among other things. In the case of aluminum powder, the moisture also leads to increased hydrogen porosity in the component.
Metals adsorb moisture from the surrounding atmosphere, and even some inert gas grades are too humid. Virgin powder can experience this deterioration during transport and storage. However, the process is reversible: drying restores the desired properties.
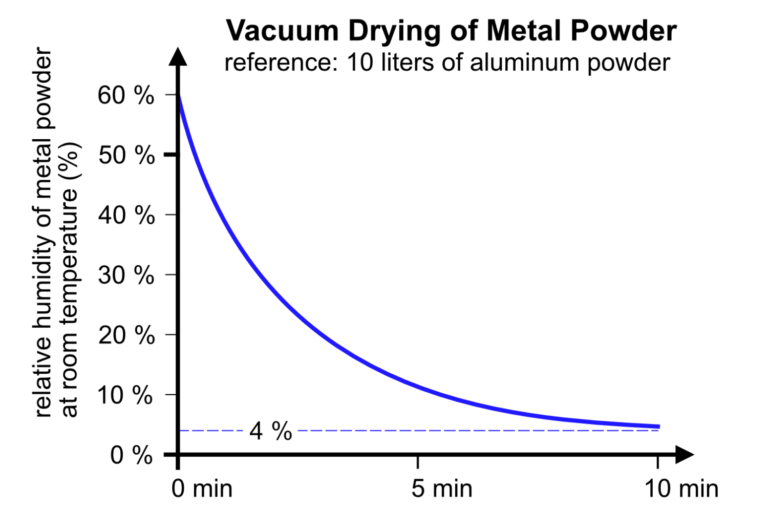
The influence of humidity on metal powder was also analyzed in a study by the Fraunhofer Institute of Laser Technology (ILT) together with FH Aachen – University of Applied Sciences and RWTH Aachen University – Chair for Laser Technology (LLT). The findings are presented in the paper “Investigation on the influence of powder humidity in Laser Powder Bed Fusion (LPBF)”, see https://www.sciencedirect.com/science/article/pii/S2212827122009830.
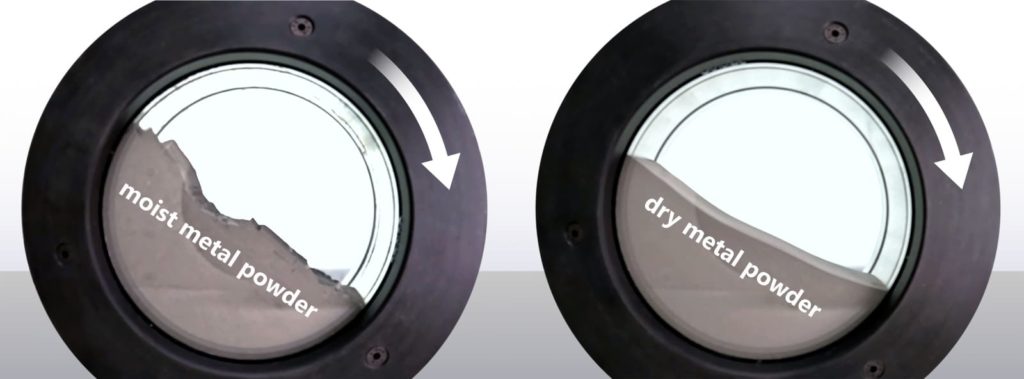
The vDryer module dries metal powder by vacuum drying. This process is very fast and does not require additional heat input. Even for batches with different degrees of moisture, vacuum drying can reliably achieve a target value, ensuring that powder with a defined degree of moisture is always available for the subsequent printing process.
With its compact dimensions and a fast drying process, the vDryer module can be very easily combined with a vacuum conveyor – such as with the vLoader 250.