PowTReX: metal powder extraction and recovery system
The PowTReX series enables the efficient reclaiming and processing of excess metal powder, after it has been used in a print job. The powder is efficiently sieved to remove oversized particles, agglomerates, broken support structures and other foreign bodies. This results in a high-quality processed metal powder that is ready for use in 3D printing.
The PowTReX system combines three functions in one compact unit:
- the aspiration and conveying of metal powder from an upstream system (e.g. 3D printer or unpacking station) into the buffer container of the PowTReX
- cleaning the metal powder removing agglomerates and oversized particles by means of a sieve
- filling the purified metal powder into a container. Optionally, a downstream machine can draw the metal powder directly from this container via a pipeline.
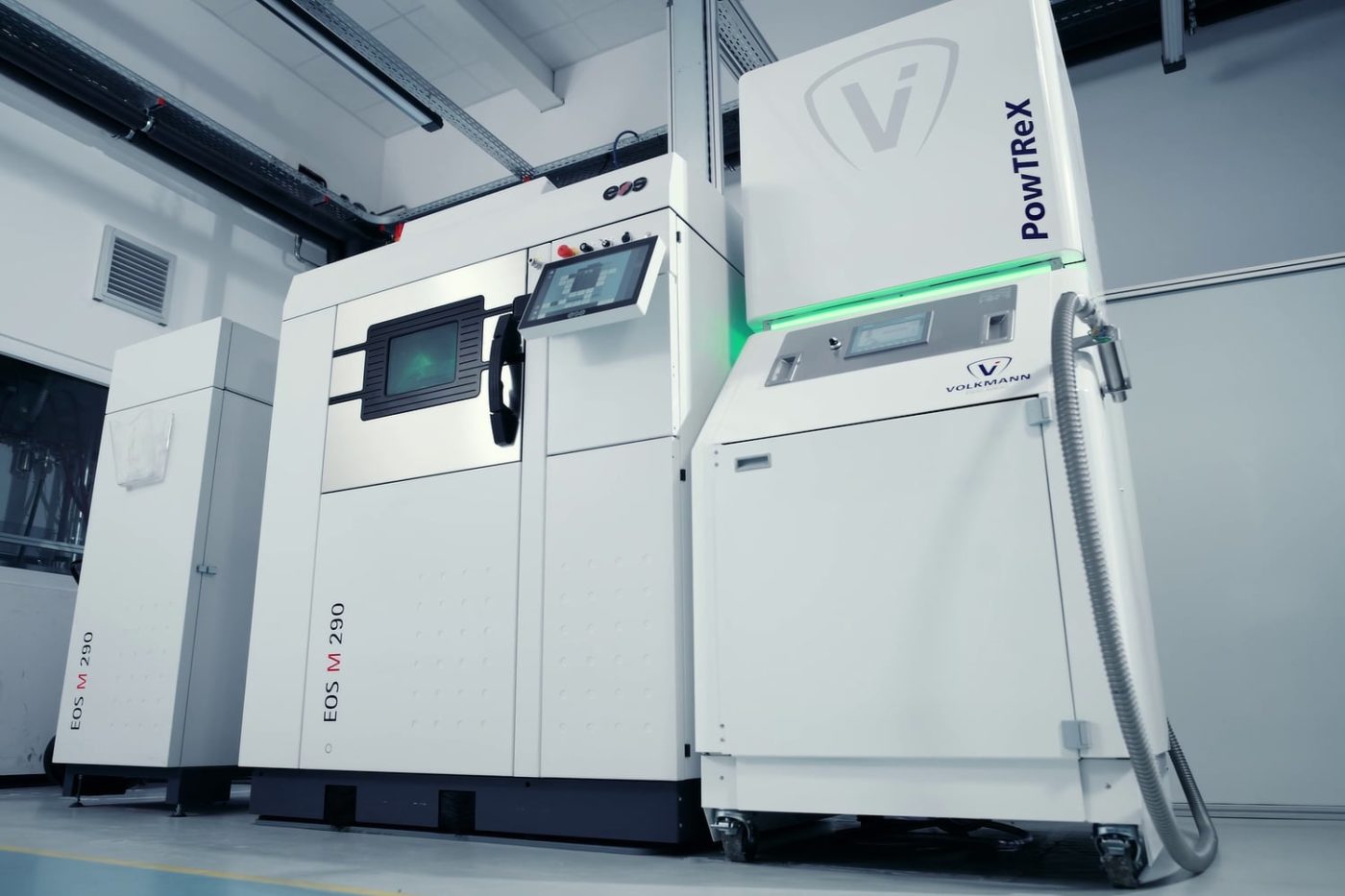
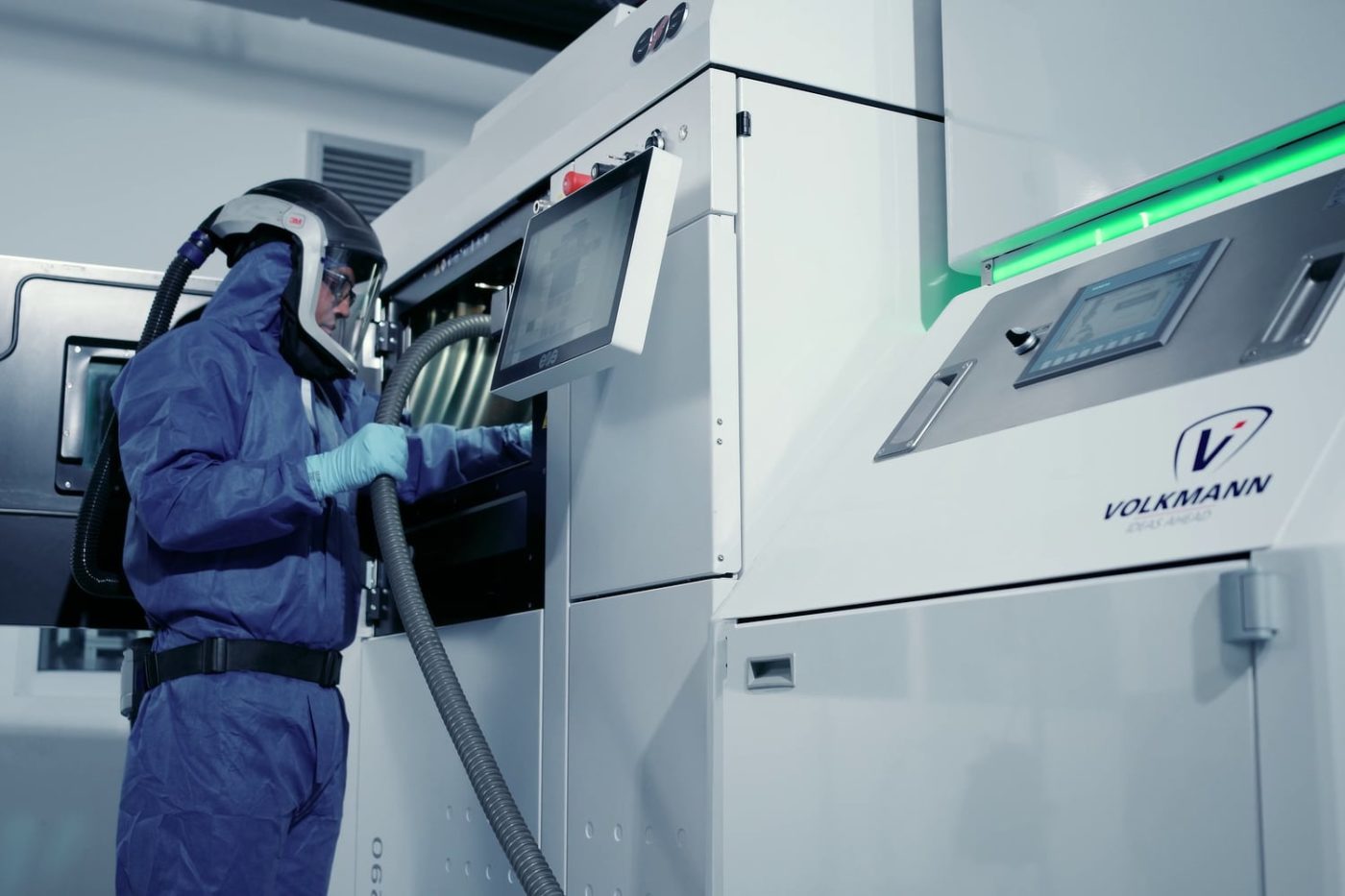
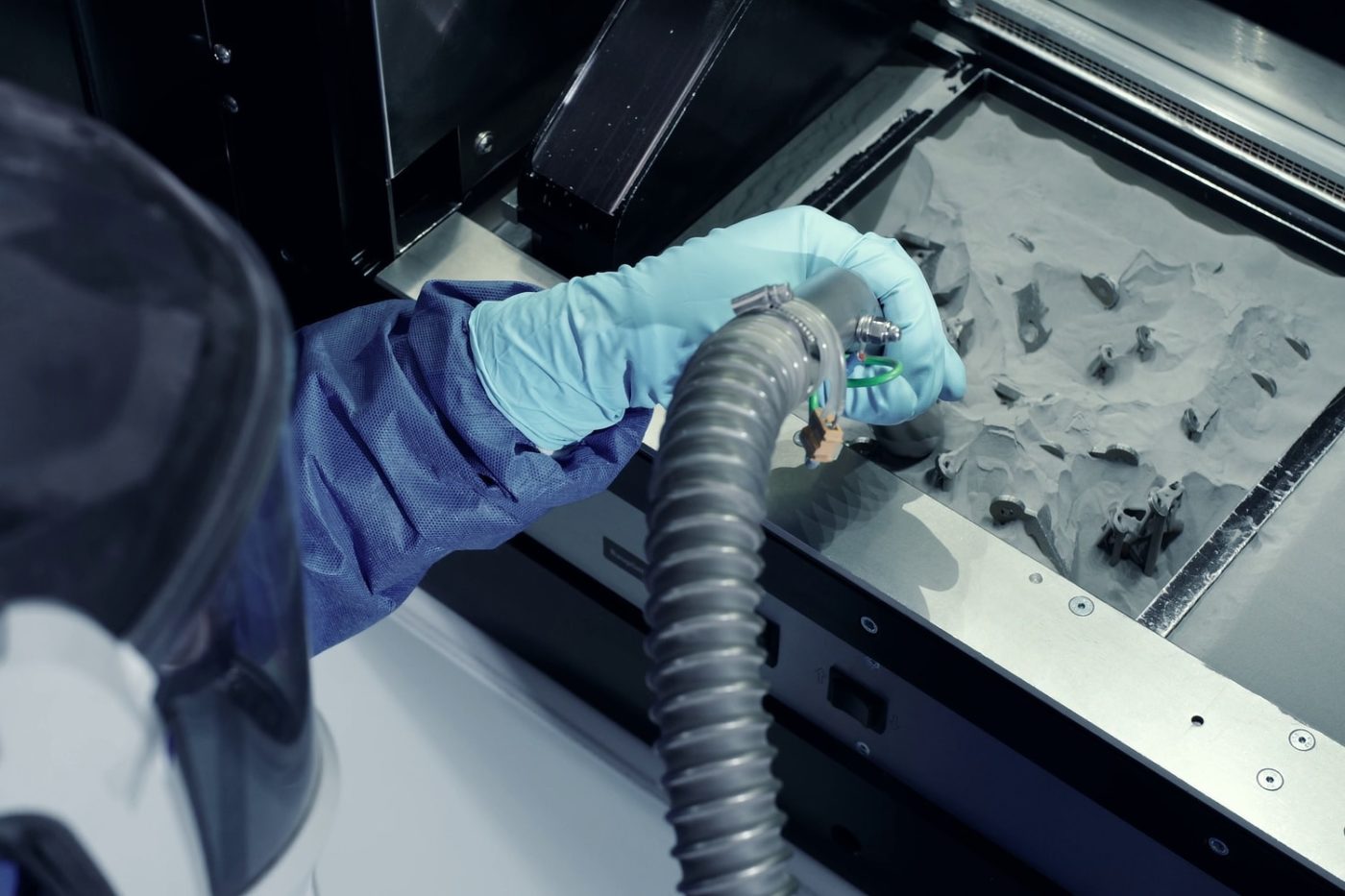
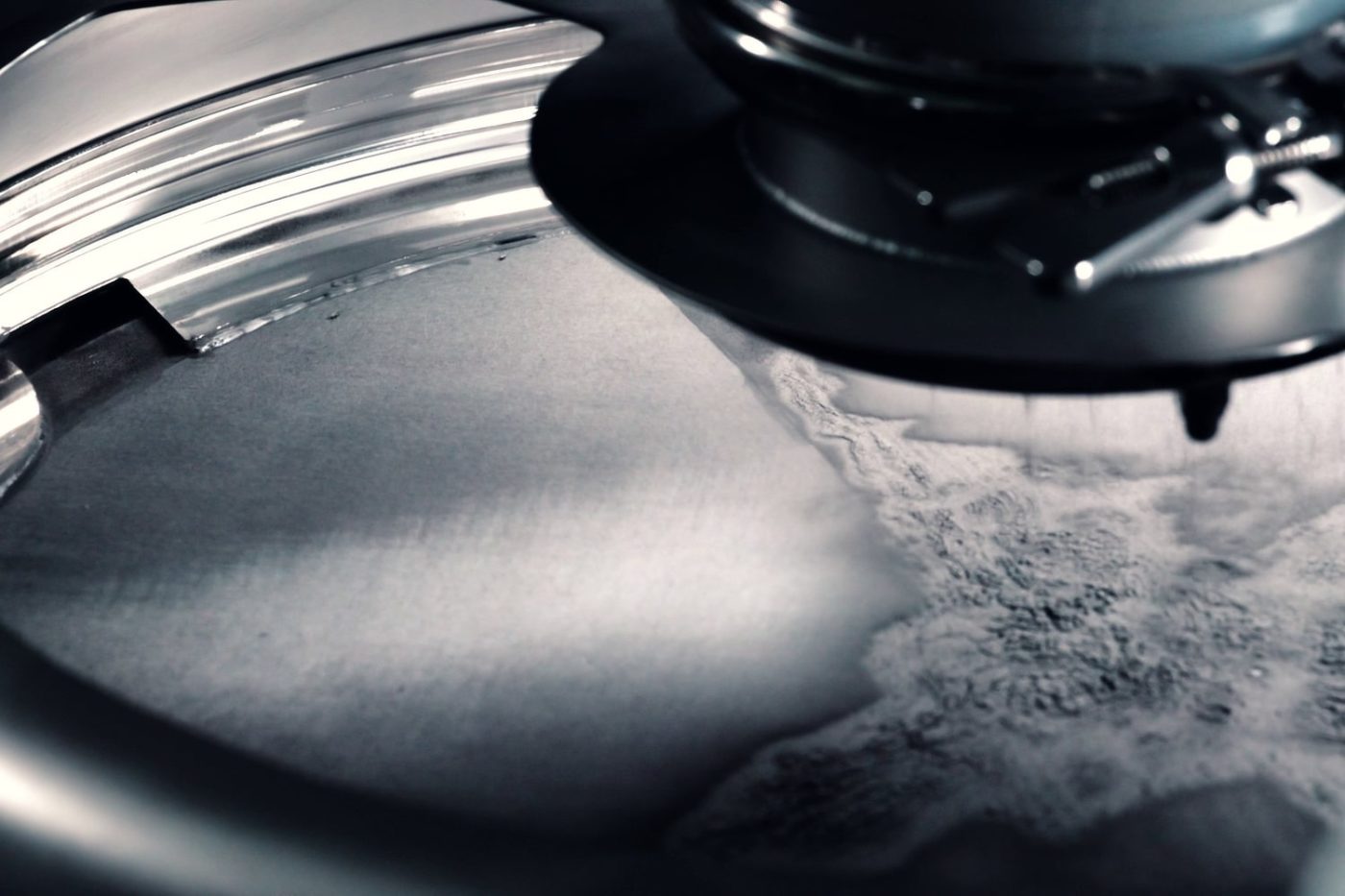
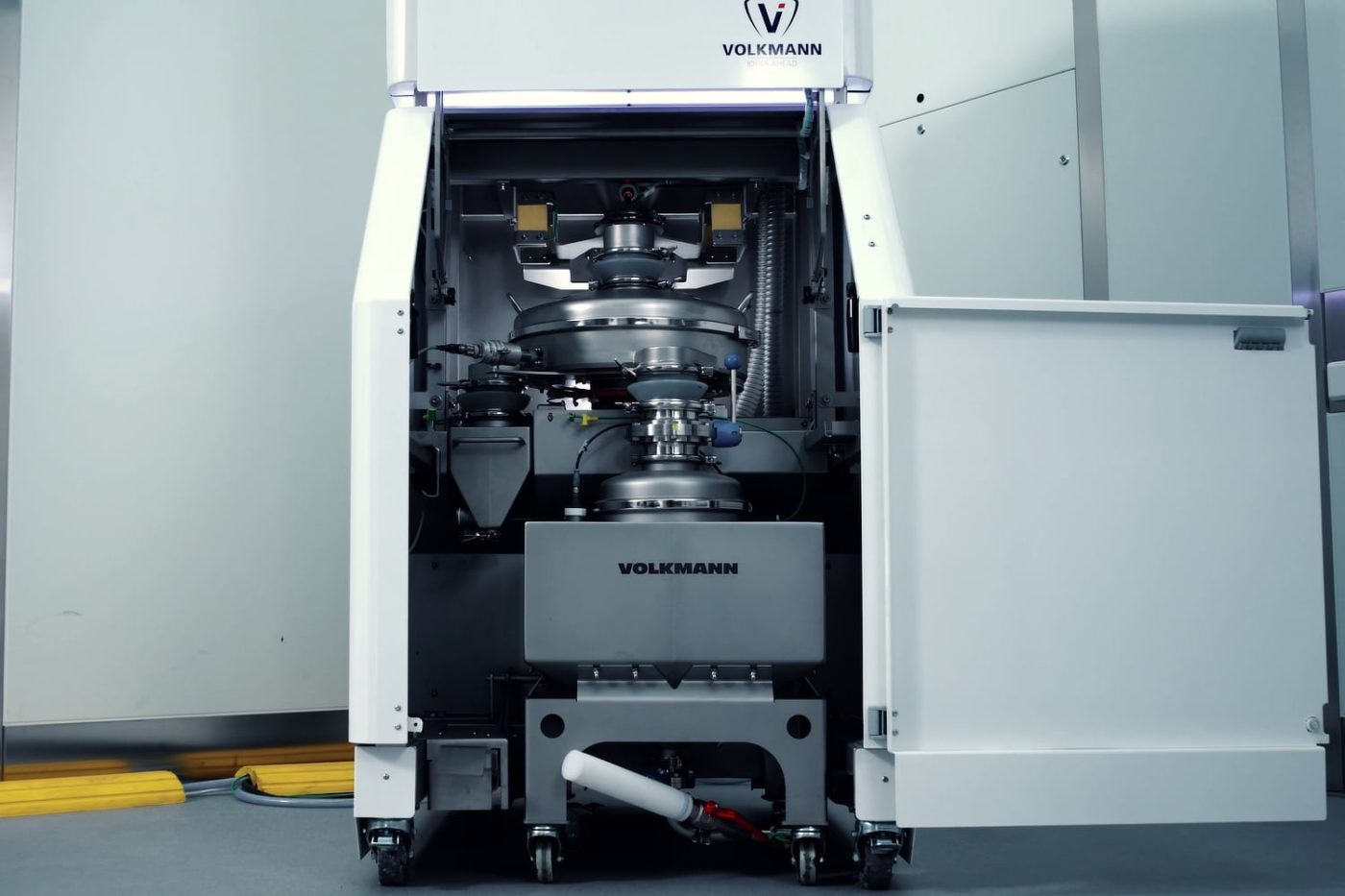
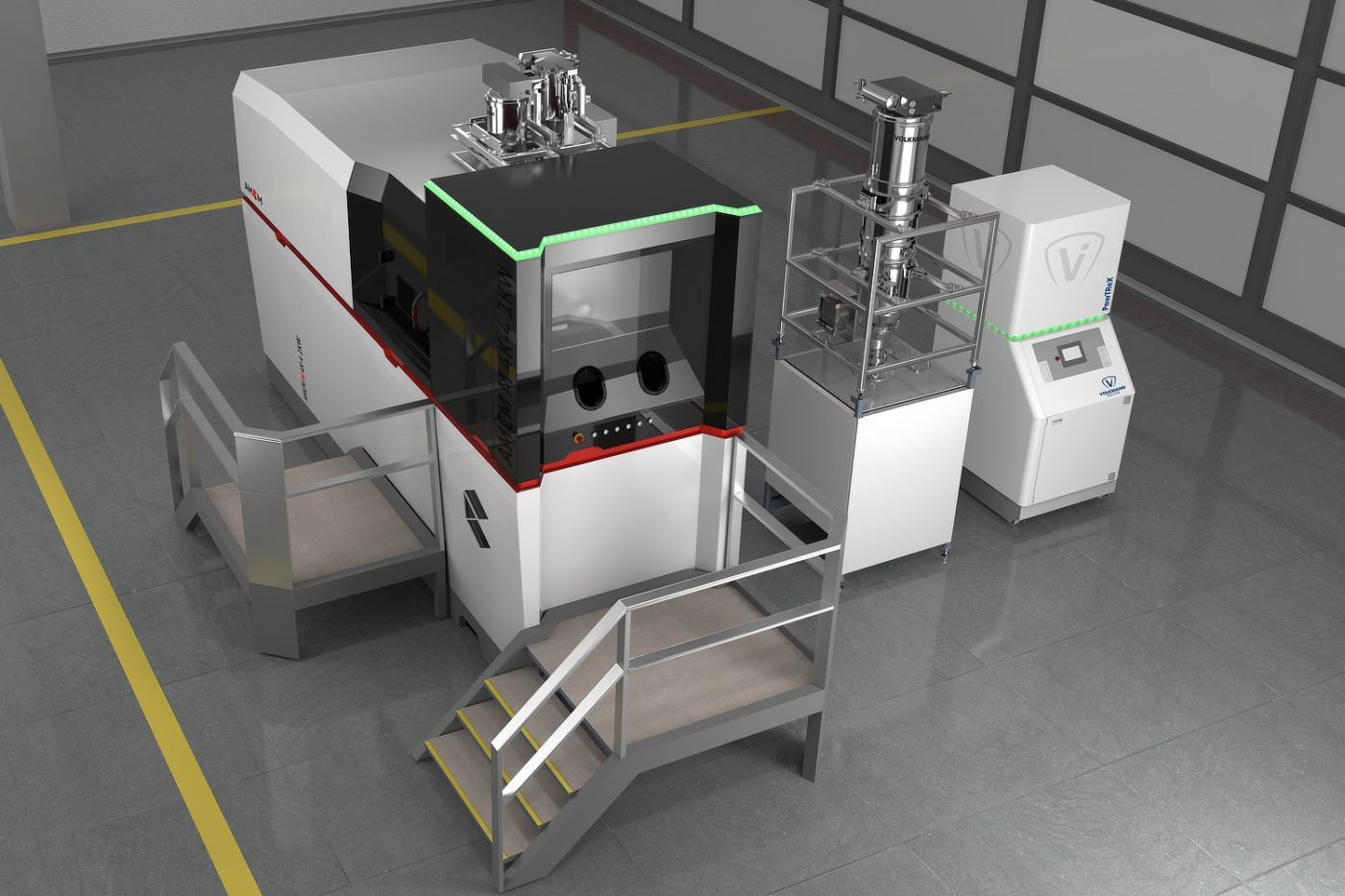
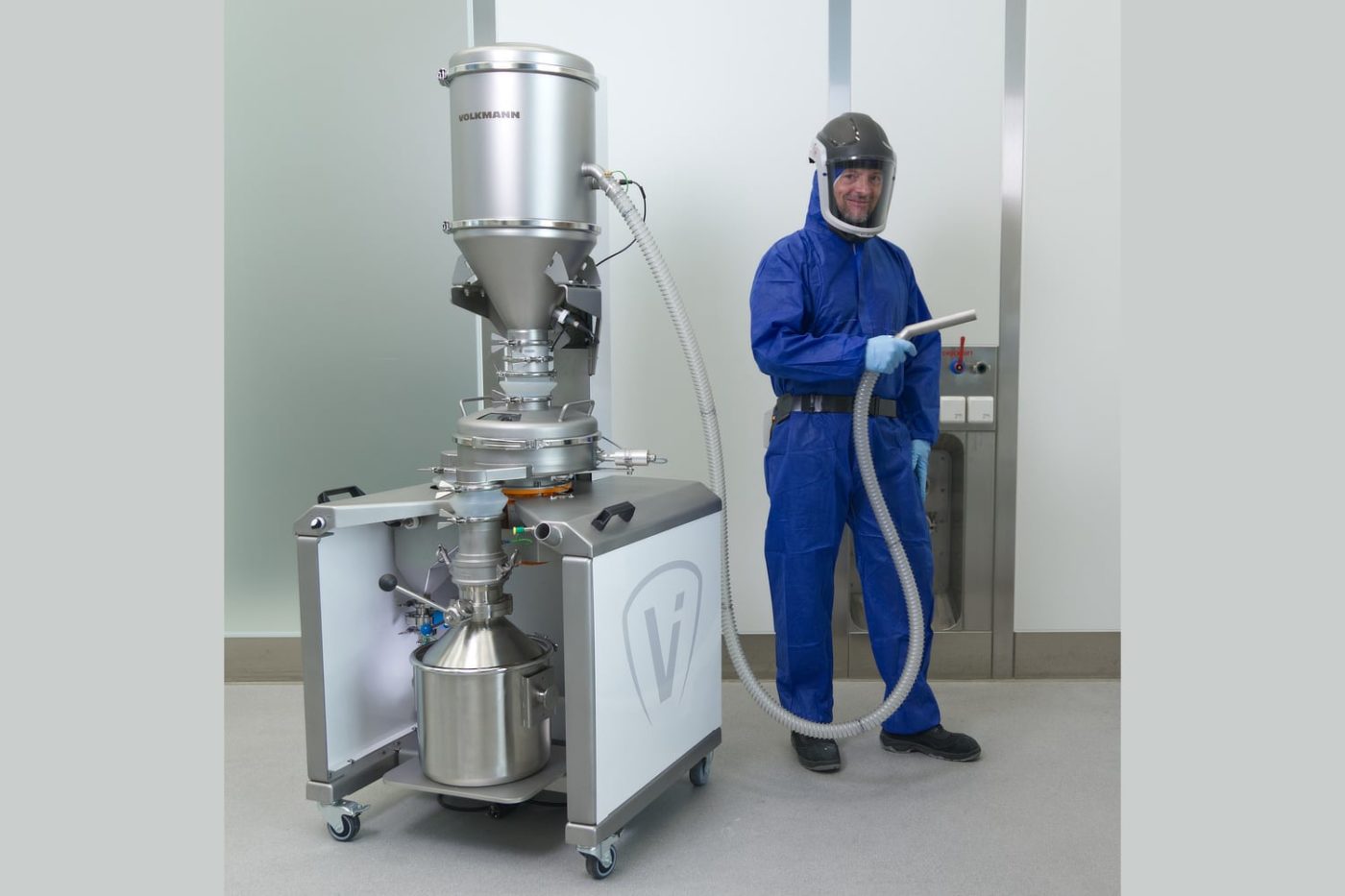
The PowTReX systems
The PowTReX family includes two series or performance classes: the PowTReX and the PowTReX basic. In addition, we can also offer customized solutions for special requirements.
PowTReX
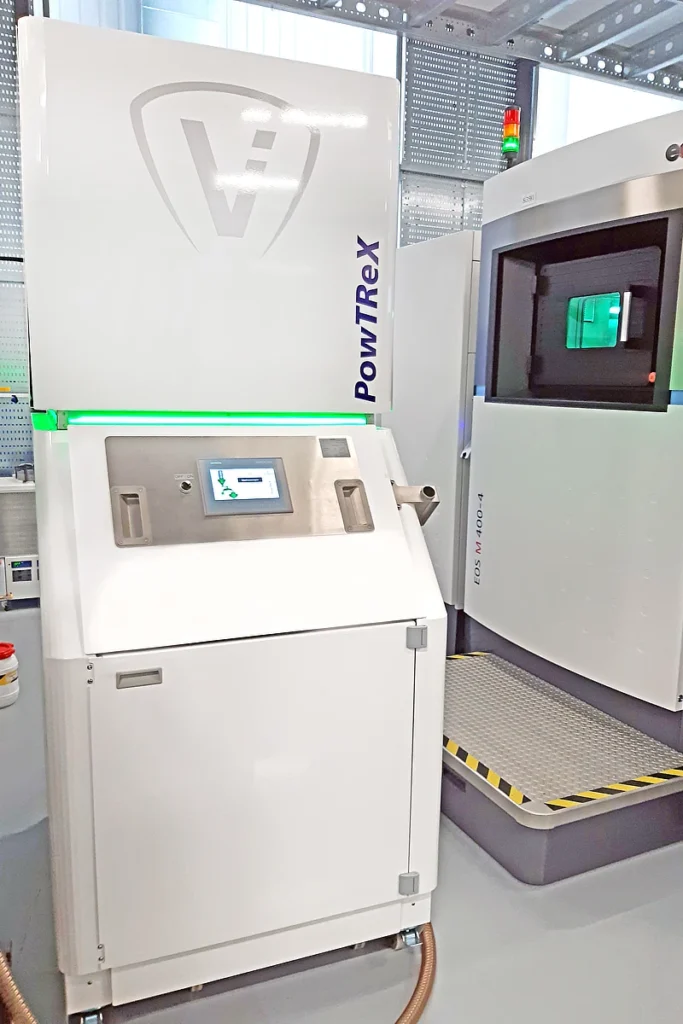
PowTReX enables powder reprocessing at a high throughput, and is therefore suitable for 3D printers with large build volumes, as well as multi-machine arrangements.
PowTReX basic
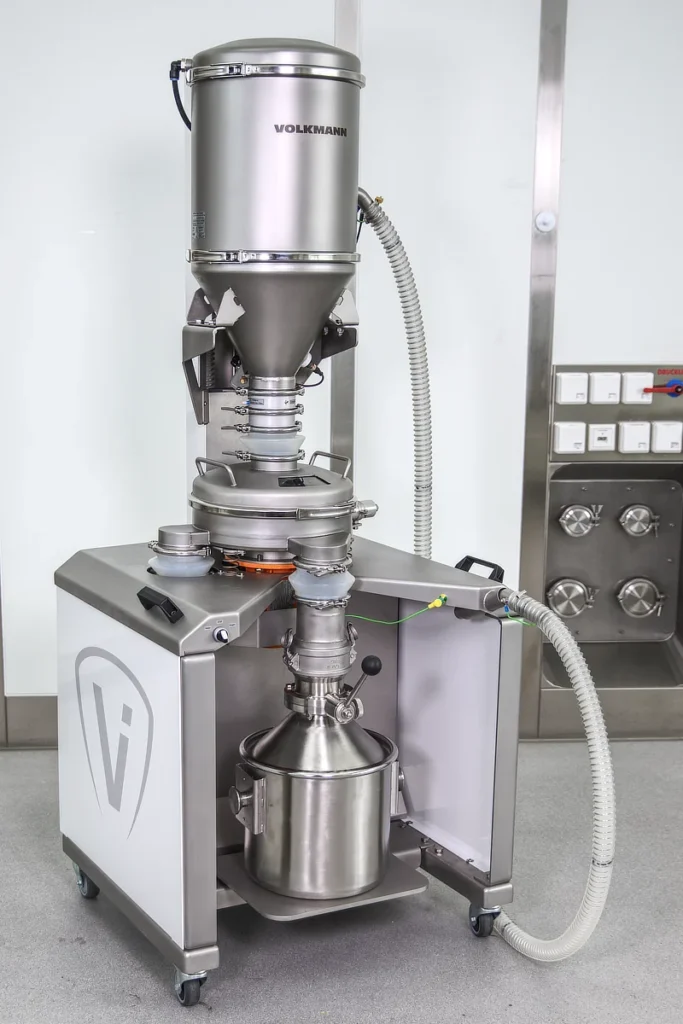
PowTReX basic offers the essential functions for the reprocessing of metal powders. The performance is designed for small to medium 3D printers. The prepared powder can be filled, for example, into an EOS bottle, SLM bottle or similar containers from other manufacturers.
PowTReX in a customized design
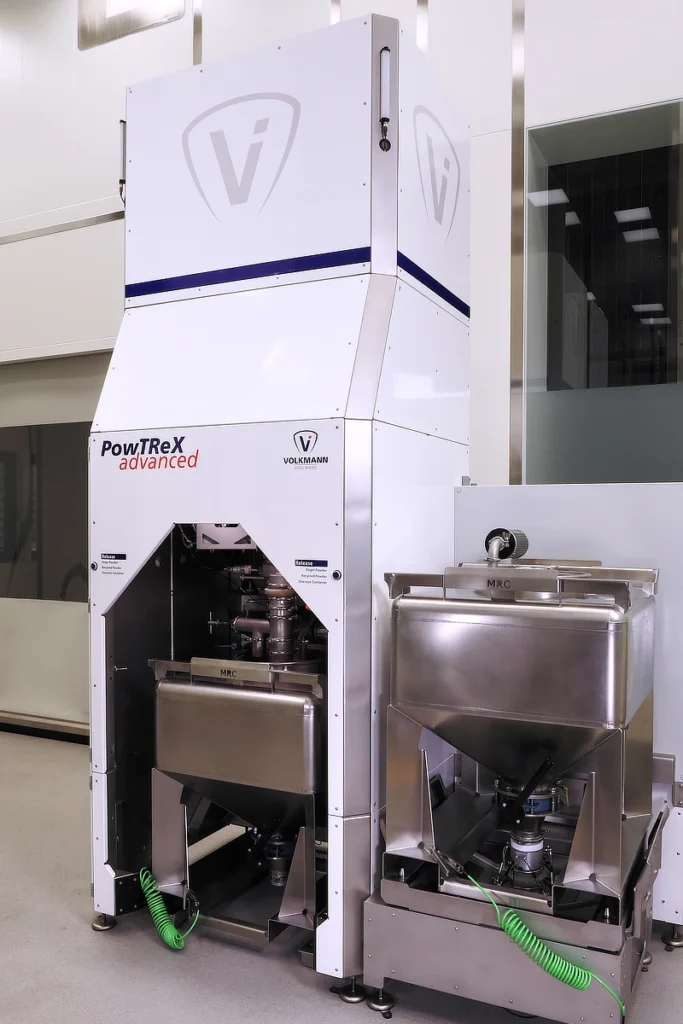
In the event that your requirements are not covered by any of our standard PowTReX systems, we can also build customized special designs to suit individual requirements.
How the PowTReX systems function
All PowTReX systems offer these functions:
- Extraction and conveying of metal powder from a 3D printer, an unpacking station, from a bin or container, or from a vHub 250 metal powder buffer. The integrated vacuum conveyor including a Multijector® vacuum pump ensures a high suction capacity. Vacuum conveying, suction conveying or pneumatic conveying can be carried out over distances of up to 25 meters. Instead of a flexible conveying hose, fixed piping, e.g. with steel pipes, can also be used.
- Buffering of the metal powder before screening: the large buffer volume in combination with the high suction power enables the powder to be transferred quickly, e.g. from an upstream printer, so that it is quickly available for the next print job.
- Reprocessing of the metal powder using a high-performance sieve: The metal powder is dosed from the buffer container onto the sieve at an optimum flow rate. The screen is vibrated by an unbalanced motor to ensure high screening performance. In addition, the screen is continuously cleaned by ultrasound to remove any particles that may be stuck in the screen mesh. Large, oversized particles, agglomerates, splatter particles and foreign bodies are discharged into a container.
- The cleaned or recycled powder is filled into a bottle or container. Appropriate adapters are available for the various containers of established printer manufacturers. Volkmann also offers containers in various sizes, which can also be used as a starting point for vacuum conveying through a fixed pipeline.
PowTReX
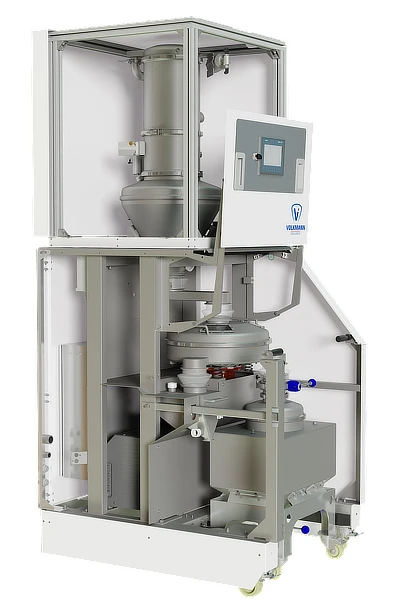
Vacuum conveyor
Buffer container
Powder feeder
Sieve with ultrasonic cleaning
Oversized material collection
Container for sieved metal powder
Fig.: View into a PowTReX with the cover panels removed.
PowTReX basic
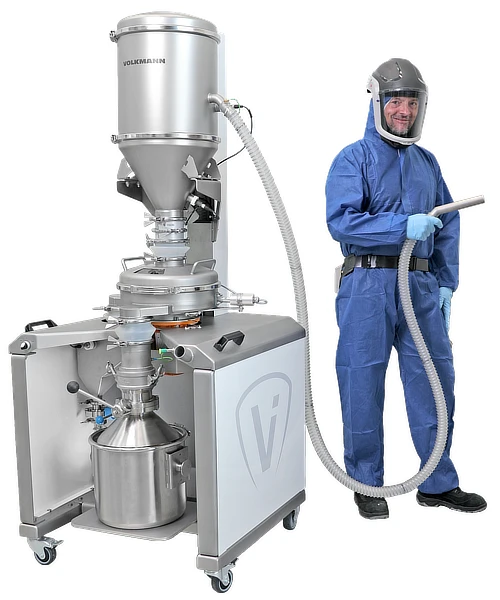
Vacuum conveyor with 20 l powder buffer volume
Powder dosing system
Sieve with ultrasonic cleaning
Oversized material collectionÂ
Bottle or container for sieved metal powder
Suitable for all metal powders commonly used in 3D printing (metal AM – Additive Manufacturing) Â
The PowTReX has proven itself in use with all common metal powders for SLM printing (Selective Laser Melting) and PBD printing (Powder Bed Fusion). However, it is also used in binder jetting for the preparation of metal powder that is wet with a binder.
The following list provides a general overview of a selection of metal and ceramic powders for which the PowTReX system is used by our customers: Steel, stainless steel, nickel alloys, copper and copper alloys, aluminum and aluminum alloys, titanium and titanium alloys, vanadium, niobium, tantalum, tungsten and ceramic powders. This list does not claim to be exhaustive. We would be happy to inform you whether your metal powder can also be processed by the PowTReX. In addition, the suitability can be checked during a test in our technical center and the results analyzed in our in-house laboratory.
You are currently viewing a placeholder content from Youtube. To access the actual content, click the button below. Please note that doing so will share data with third-party providers.
More InformationProven in practice with numerous installations
The PowTReX system has proven itself in numerous installations in intensive use over many years. Users include well-known companies and groups in Europe, North America and Asia from the aerospace, automotive and medical technology sectors, among others.
With the PowTReX EOS edition, a validated version of the PowTReX system tailored to the EOS printers was also developed in close partnership with EOS GmbH and is marketed directly by EOS. Further information: the partnership with EOS and the EOS edition.
Maximum yield in the recovery of metal powder
Metal powder is costly, which is why maximum utilization of the material is the top priority. The PowTReX system takes this into account in many ways. The high suction power enables optimum emptying and material transfer from the 3D printer, unpacking station or other material source. All surfaces within the PowTReX that come into contact with the powder are designed in such a way that no powder residue can be deposited there. Overloading is prevented by dosing the material feed onto the sieve, as otherwise too much metal powder would be sieved out into the reject container. In addition, the sieve is always supplied with the optimum load, resulting in a very high throughput of up to 800 kg/h (reference: stainless steel powder). All in all, these measures result in a very high proportion of recovered metal powder.
Efficiency through fast powder extraction
The fast powder extraction from the upstream station – e.g. from a 3D printer – results in a further economic advantage: the set-up time of the station is reduced and it is available again more quickly for a productive process.
High quality processed powder
The ultrasonic sieve reliably separates all foreign bodies and oversized particles into a separate container. Handling and processing the powder in a closed system ensures that no foreign bodies from the environment contaminate the powder.
Wide selection of screens
The screen is stretched on a screen frame and can be installed and removed in a few simple steps. Screens with mesh sizes of 50 µm, 56 µm, 63 µm, 75 µm, 85 µm and 106 µm are available as standard sizes. Other screen mesh sizes can also be supplied on request.
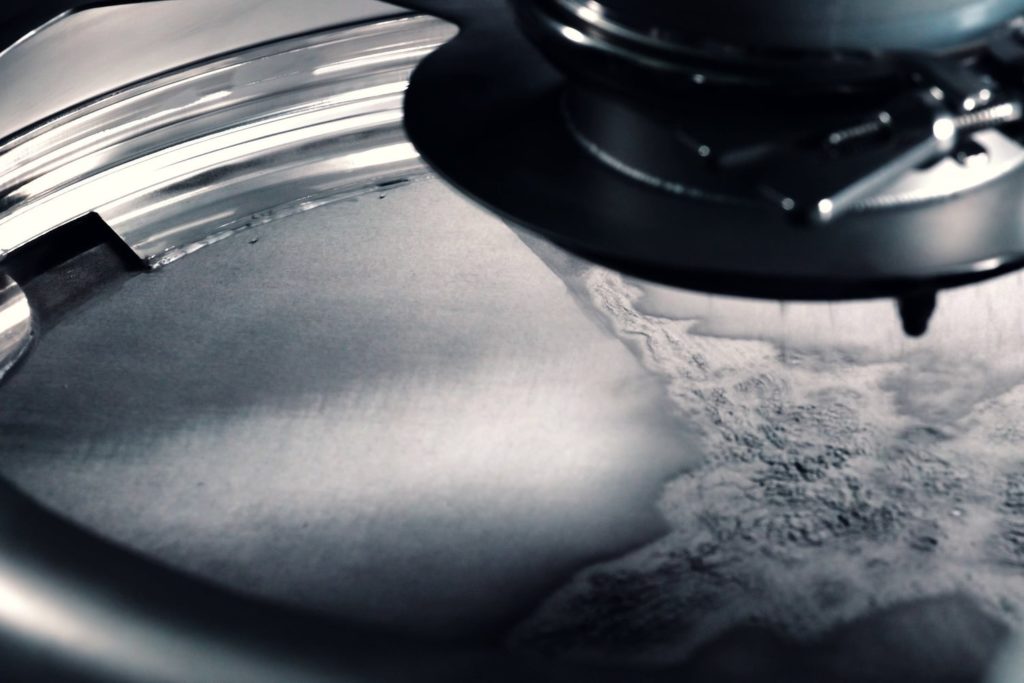
Optional: Inert operation with inert gas
The PowTReX system is also available in the PowTReXi variant for inert powder handling. Common inert gases are argon and nitrogen. The inert gas is usually circulated in a closed gas loop with the feed point – e.g. a 3D printer. Only a small volume of new gas needs to be added per cycle, which significantly reduces overall gas consumption. In an inert gas loop, the vacuum for conveying the material is generated by an electric vacuum pump.
Protection of the powder + protection of the operator
In the PowTReX system, the powder and the environment are isolated from each other. This separation begins with extraction and continues until the powder is filled into bottles or containers, isolated through fixed piping to the downstream station. As a result:
- The powder is protected from environmental influences and from contamination or cross-contamination by other powders.
- The operator and the environment are protected from the powder and its dust.
The exhaust air from the vacuum pump is safely cleaned by a two-stage filter system.
The vacuum conveying of material provides additional protection: if there is a leak in the conveying line, the air is only ever drawn into the conveying line from the surrounding area due to the vacuum. This means that no powder particles can escape into the environment.
Safe handling of dust-explosive powders
The PowTReX system is designed for the handling and conveying of dust-explosive powders. In accordance with the requirements of the ATEX directive, the system has no ignition sources that could trigger a dust explosion. When designing the system, attention was paid to earthing all components and the conveying lines. This means that no electrostatic charging can occur and consequently no spark discharges that could lead to an explosion.
The vacuum conveyors used in the PowTReX systems are type-tested in accordance with Directive 2014/34/EU ATEX and can therefore be operated safely, even without inertization, for any metal powder that is not self-igniting.
Mobile system for use next to the 3D printer
The systems in the PowTReX series are designed for mobile use within the shop floor. The compact devices have rollers and can be easily moved by a single operator between several locations, such as 3D printers.
Because the system has a small footprint, the PowTReX is often set up stationary directly next to a 3D printer.
Easy maintenance, cleaning and material changes
Parts and components that come into contact with metal powder can be easily dismantled, cleaned and reassembled. In addition, the components are designed for manual handling in terms of size and weight. Cleaning when changing materials can be accelerated by using a second set of connecting parts.
Simple operation and automatic screening
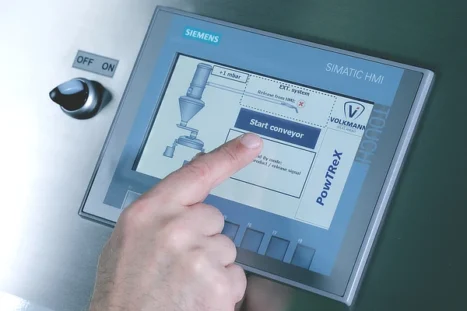
PowTReX systems are generally very easy to operate. With the PowTReX system, the default settings are made via a touch panel. With the PowTReX basic, the processes are started and stopped using a rotary switch. The metal powder is sieved automatically. In the meantime, the operator can devote themselves to another task.
Data interfaces to other systems
The PowTReX can exchange signals with other machines or controllers (24 V DC). The PowTReX is also optionally equipped with an OPC-UA interface. We would also like to point out that we have also installed UL-certified controls for the USA.
PowTReX systems in customized designs
We also develop special versions of the PowTReX for our customers to meet special requirements. Proven components and individual solutions are combined to create a completely new solution. The following list shows some of the functions and features that we have already implemented in such systems for our customers:
- Large container for buffering metal powder before processing.
- Two buffer containers for different metal powders or qualities. These are dosed onto the screen in an adjustable mixing ratio to create a homogeneous blend.
- Filling of the processed powder into large IBC containers.
- Weighing of buffers or containers before or after powder processing.
You are currently viewing a placeholder content from Youtube. To access the actual content, click the button below. Please note that doing so will share data with third-party providers.
More InformationComparison PowTReX vs PowTReX basic
PowTReX![]() |
PowTReX basic![]() |
|
---|---|---|
suitability for automated closed powder loop: | yes | no |
throughput: | Stainless steel powder: ca. 600 kg/h Aluminum powder: ca. 300 kg/h |
Stainless steel powder: ca. 150 kg/h Aluminum powder: ca. 75 kg/h |
vacuum conveyor: | integrated conveyor | integrated conveyor |
conveying capacity: | up to 1,000 kg/h (stainless steel powder) | up to 750 kg/h (stainless steel powder) |
vacuum pump: | Multijector, alternatively electric rotary claw pump | Multijector |
volume of the integrated buffer tank (material feed): | gross volume: 32 L usable capacity: 27 L |
gross volume: 25 L usable capacity: 20 L |
variants of the material supply: |
|
|
simultaneous filling and sieving: | yes | no |
operation under inert gas: | optional (variant PowTReXi) | no |
Material discharge:
|
yes no yes |
yes optional yes |
operator interface: | touch panel with visualization | selector switch |
connectivity for a distributed control system (DCS): | signals 24 DC, OPC-UA optional | no |