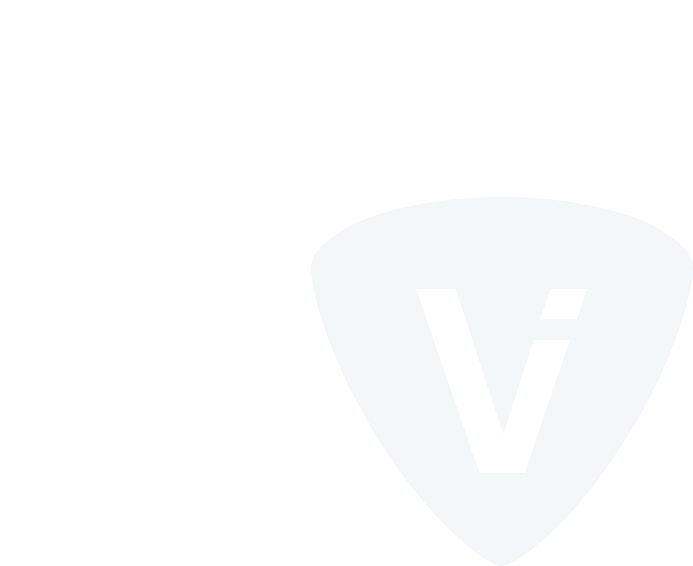
Conveying of powder, granulate, etc. by means of a vacuum conveyor
VOLKMANN’s Vacuum Conveyors can transport numerous granulated bulk materials, small parts, powders, and pigments under vacuum in lean and dense phase through hoses and pipes. They are easy to install and quite simple to operate. By using vacuum these systems can keep the production environment clean.
Due to constant development and improvement in technology, removal of explosion risks and with a focus on good hygienic solutions, Vacuum Conveyors today are a preferred choice in many industries. They can transfer nano-sized material and fine dust with particles size from 0,1 µm up to bigger sized tablets, sweets, or bottle caps, for example. They are good for highly abrasive powders, mixtures, light filling materials (such as fumed silica with a bulk density of only 0,05 kg/l), but also work well with metal powders which can have bulk densities of up to 10 kg/l.
They can make all powder handling in production processes safe and reliable, making the work of operators easier and improving the conditions in the workplace: choose Vacuum Conveying systems from VOLKMANN.
Vacuum conveyor variants for different tasks
The heart of a vacuum conveyor system is the vacuum conveyor. Our modular series are available in different sizes and thus cover a wide performance spectrum. At the same time, requirements such as hygienic design or pressure shock resistance can also be met.
Pickup, Transfer and Loading of Machines with Bulk Materials
- user friendly systems with safe material transfer
- easy material pickup and dust-free loading of machines
- gentle dense phase conveying, no segregation of material mixtures
- optimum hygienic conditions
- reliable filter systems in GMP quality
- simple to install and to operate
- low energy consumption
- favourable investment- and operating costs
- product contact parts are 316L Stainless Steel or FDA approved soft parts
Suitable for the Chemical, Pharma and Food industries (amongst others), our modular designed Vacuum Conveyors offer an easily customisable solution to match each individual application. Even critical materials can be conveyed safely, and modified conveyors can be used for hazardous applications, such as inside explosion risk areas or with highly toxic materials.
Conveying capacities: 100 kg/h up to 3.5 t/h (with a possible maximum of about 12 t/h)
Conveying distance will affect the achievable transfer rate and have been seen to vary from as little as a few meters up to 100m (with total lift of 40m).
We offer conveying trials and demonstrations on-site or in our test facility. With any query we analyse your material handling task, along with any special requirements, to convey your products. We want you to be sure, that the required capacity is reached, that your product is not affected in an unacceptable way by the transportation and convince you of the stability of the vacuum conveying process provided by Volkmann Conveyors.
How Vacuum Conveyors Work
Vacuum conveyors transport powder, dust, pigments, granulated material, tablets, capsules, small parts etc. in a suction air stream under vacuum through hoses or pipes. They are easy to install and to operate. Even if leakages occur, no product can escape into the environment because of the vacuum.
-
(A)
-
(B)
-
(C)
-
(1)
-
(2)
-
(3)
- The vacuum pump (1) generates a vacuum in the Vacuum Conveyor’s separator body. Air rushes in, from the feeding point (A) through the hose/pipe and into the suction inlet (2). The bulk material is aerated and then carried in this air stream.
- Due to the special designed separator body, the velocity is reduced, and the material is collected gently above the vacuum conveyor’s discharge valve. Inside the separator body a filter module (3) separates airborne dust and product from the conveying air. With fine dust, a cyclone element can be inserted into the separator to help provides higher transportation capacities due to the lower loads across the filter elements.
- When the separator is filled with product, the vacuum pump switches off. Inside of the vacuum conveyor the pressure is equalises with the surrounding area within tenths of a second. The separated material is discharged from the vacuum conveyor through the discharge valve and falls directly into the receiving location (B).
- When the conveyor discharges, the filter elements are cleaned automatically by an air shock system. The occasional filter cake is released from the filters. Volkmann offers piston vibrators and fluidizing units to improve the discharge of sticky or bridging bulk materials.
- After unloading the product, the discharge element closes and the whole conveying cycle starts again.
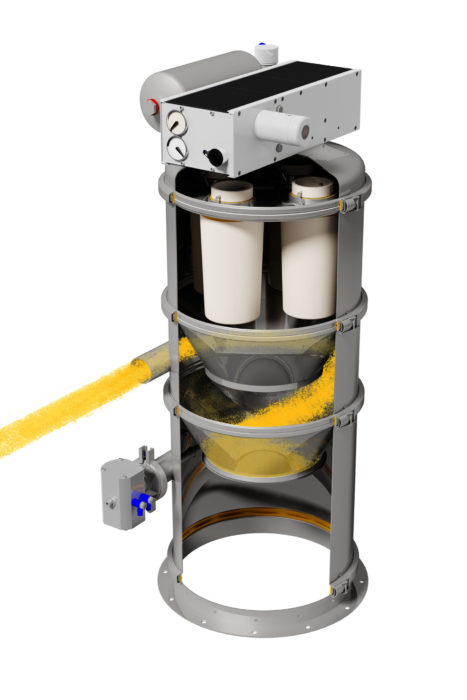
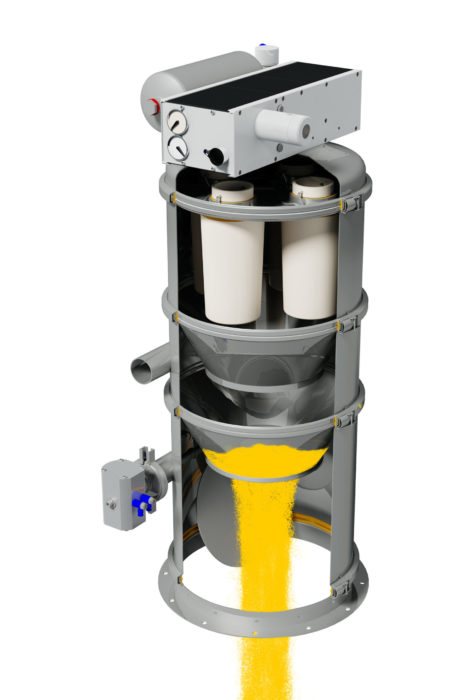
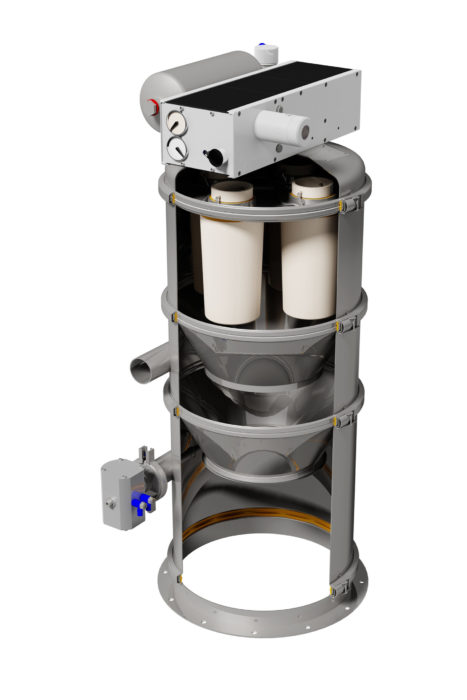
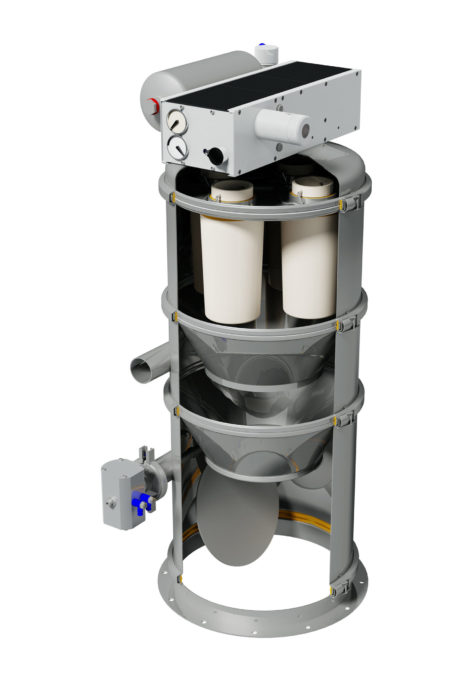