Metallpulver für den 3D-Druck ist teuer, und bei einem Druckjob bleibt viel Pulver ungenutzt übrig. Vor einer erneuten Verwendung müssen aber erst die verschmolzenen Pulverkonglomerate ausgesondert werden. Im Rahmen des IDAM-Forschungsprojekts hat VOLKMANN dafür eine Pulveraufbereitungsstation entwickelt und in einen vollautomatisierten Druck, Auspack- und Entpulverungsprozess bei der BMW AG integriert.
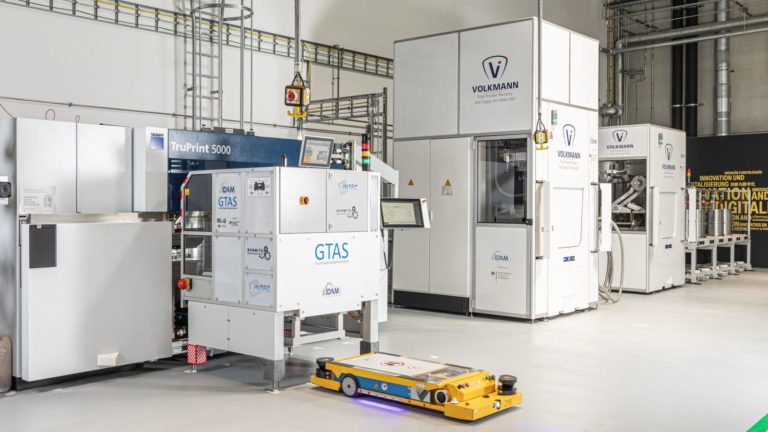
Beim industriellen 3D-Druck mit Metallpulvern entstehen – neben den gewünschten Bauteilen – auch viele kleine Konglomerate aus verschmolzenen Pulverpartikeln. Aber auch abgebrochene Stützstrukturen können sich im gebrauchten Pulver finden. Solche Partikelkonglomerate und Fremdkörper gilt es zuverlässig zu entfernen, bevor das Pulver wieder einem Druckprozess zugeführt wird.
Das aufbereitete Pulver wird in der Regel mit neuwertigem Pulver gemischt. Der Anteil des Neupulvers kompensiert dabei jene Menge, die vorher in den gedruckten Bauteilen verarbeitet wurde. Das Mischungsverhältnis kann sich auf die Bauteilqualität auswirken, weshalb die Produktentwicklung und Qualitätssicherung oft enge Vorgaben machen. Außerdem muss eine homogene Durchmischung gewährleistet sein.
Die Aufbereitung von gebrauchtem Metallpulver und die Mischung mit neuwertigem Pulver wird in der Demonstratorlinie bei der BMW AG durch eine zentrale Pulveraufbereitungsstation erledigt. Die Demonstratorlinie des IDAM-Forschungsprojekts ist eine digital vernetzte, vollautomatisierte 3D-Druck-Fertigungslinie für die automobile Serienproduktion. Unter der Leitung der BMW Group haben insgesamt 12 Unternehmen und Forschungsinstitute von 2019 bis 2022 an dem Projekt mitgewirkt, darunter die VOLKMANN GmbH. Mit einer Demonstratorlinie bei der BMW AG (München / Oberschleißheim) und einer zweiten bei GKN Additive (Bonn) wurden erfolgreiche Praxiserprobungen durchgeführt. Bei GKN erfolgt die Pulveraufbereitung durch ein PowTReX-System von VOLKMANN. Das IDAM-Projekt (Industrialization and Digitalization of Additive Manufacturing) wurde vom Bundesministerium für Bildung und Forschung (BMBF) gefördert.
Die zentrale Pulveraufbereitungsstation bei der BMW AG wurde durch VOLKMANN entwickelt und gebaut, wobei viel Erfahrung aus dem PowTReX-Pulveraufbereitungssystem eingeflossen ist. Darüber hinaus bietet die Station aber zusätzliche Möglichkeiten zum Puffern von gebrauchtem und neuwertigen Pulver in Silos, sowie zum Mischen dieser Fraktionen im vorgegebenen Verhältnis. Die Station erledigt außerdem die Trocknung des Metallpulvers – dazu später mehr.
Der sehr hohe Automatisierungsgrad der IDAM-Demonstratorlinie findet sich auch in der Pulveraufbereitungsstation. Das gebrauchte Metallpulver wird von der vorgelagerten VOLKMANN-Entpulverungsstation per Vakuumförderung durch eine Rohrleitung zur Pulveraufbereitungsstation gefördert und dort in einem Silo gepuffert. Auch innerhalb der Station laufen alle Prozessschritte für die Aufbereitung inkl. der Mischung mit neuwertigem Metallpulver automatisch ab.
Das fertig aufbereitete Metallpulver wird in einen Supply-Zylinder gefüllt, dieser mit einem Deckel verschlossen, von einem Transfermodul / FTS übernommen und zur nächsten Station transportiert.
Lediglich die Befüllung mit neuwertigem Pulver erfolgt in dieser Prototypanlage noch manuell. Aus Weithalsflaschen wird neues Pulver per Sauglanze abgesaugt und durch einen Vakuumförderer zum Vorratsbehälter transportiert. Bei zukünftigen Produktionslinie kann auch dieser Arbeitsschritt automatisiert werden.
Der hohe Automatisierungsgrad in der Pulveraufbereitungsstation schützt das Personal vor dem Kontakt mit Metallpulvern und Stäuben. Manuelle Arbeitsschritte unter einer Schutzmaske entfallen weitgehend. Die Pulveraufbereitung findet in verschlossenen Behältern statt, und die Pulverförderung im Unterdruck verhindert den Austritt von Stäuben.
Höhere Bauteilqualität durch getrocknetes Metallpulver
Die VOLKMANN-Pulveraufbereitungsstation kann noch mehr – in ihr wird das Metallpulver auch getrocknet. In dem IDAM-Forschungsprojekt war eine Trocknung anfangs aber gar nicht vorgesehen. Statt dessen sollte das Metallpulver mit einem Inertgas vor der Oxidation geschützt werden. Untersuchungen durch das Fraunhofer-ILT (Institut für Lasertechnologie, Aachen, https://www.ilt.fraunhofer.de/) zeigten aber auf, dass der Einsatz von Inertgas beim Handling von Metallpulver zu keiner signifikanten Verbesserung der Bauteilqualität führt.
Gleichzeitig wurde nachgewiesen, dass die Feuchte des Metallpulvers einen erheblichen Einfluss auf das Druckergebnis besitzt. Feuchtes Metallpulver besitzt schlechte Fließeigenschaften, und deshalb können beim Auftragen einer neuen Pulverschicht im Pulverbett Fehlstellen entstehen. Bei einigen Metallen und Legierungen – z.B. bei Aluminium – entstehen durch das gebundene Wasser beim Drucken außerdem Poren im Bauteil.
Die Ursache für die Metallpulverfeuchte liegt in den oft stark hydrophilen Oberflächen von Metallen. Das feine Metallpulver besitzt eine große Oberfläche und kann somit besonders viel Wasser aus der Umgebung adsorptieren. Es braucht eine Exposition von lediglich wenigen Minuten, und das Metall hat aus der Luft oder einem anderen Gas so viel Wasserdampf adsorptiert, dass sich dies im Druckergebnis deutlich bemerkbar macht. Selbst bei Einsatz von Inertgasen wie z.B. Stickstoff ist zu beachten, dass manche Gasqualitäten eine zu hohe Feuchte besitzen und damit die Metallpulverqualität verschlechtern.
Die Untersuchungen haben auch aufgezeigt, dass durch eine Trocknung die ursprünglichen Eigenschaften des Metallpulvers wiederhergestellt werden können. Die Vakuumtrocknung ist hierfür besonders gut geeignet: sie kann sehr einfach und platzsparend implementiert werden und ist sehr effizient. Außerdem kommt diese Technologie ohne eine Wärmequelle im Bereich des Pulvers aus, was in Hinblick auf die staubexplosiven Metallstäube ein großer Vorteil ist. Selbst bei Schwankungen in der Feuchte des zugeführten Pulvers wird eine konstante Restfeuchte erzielt. Die Vakuumtrocknung kann auch bei neuwertigem Metallpulver eingesetzt werden, um evtl. in der Logistikkette adsorptierte Feuchtigkeit wieder zu entfernen.
Die Vakuumtrocknung lässt sich sehr gut mit einer Vakuumförderungsanlage kombinieren. Bei der BMW-Demonstratorlinie wurde die Vakuumtrocknung in die zentrale Pulveraufbereitungsstation integriert, und erfolgt dort nach der Siebung und dem Beimischen von neuwertigem Pulver.
Durch den Verzicht auf Inertgas beim Pulverhandling entsteht ein erhebliches Einsparungspotential – sowohl in der technischen Ausstattung wie auch bei den Betriebskosten. Die Vakuumtrocknung lässt sich vergleichsweise kostengünstiger umsetzen. Bei der Pulveraufbereitungsanlage bei der BMW AG wurde unter dem Strich ca. 30 % der ursprünglich budgetierten Investitionskosten eingespart.
Zentrale Pulveraufbereitung für mehrere 3D-Drucker
Die Pulveraufbereitungsstation hat genug Leistung, um die Pulveraufbereitung für vier oder mehr 3D-Drucker zu übernehmen. Dies läßt sich auch mit einer automatischen Entpulverungsstation verbinden, wodurch eine sehr wirtschaftliche Lösung für das automatische Auspacken und Entpulvern der Baujobs und die anschließende Pulveraufbereitung entsteht.
Der Transport von den Baurahmen und Pulvercontainern zwischen den 3D-Druckern und einer zentralen Entpulverung und Pulveraufbereitung kann manuell per Hubwagen erfolgen, und dies wird in den kommenden Jahren auch das vorherrschende Konzept sein. In der weiteren Zukunft wird sich in der Additiven Fertigung der vollautomatischer Transfer mittels fahrerlosen Transportsystemen, und die automatische Beschickung der Drucker mit Pulver über Förderleitungen per Vakuumförderung durchsetzen.
Weiterführende Meldungen über das IDAM-Projekt: