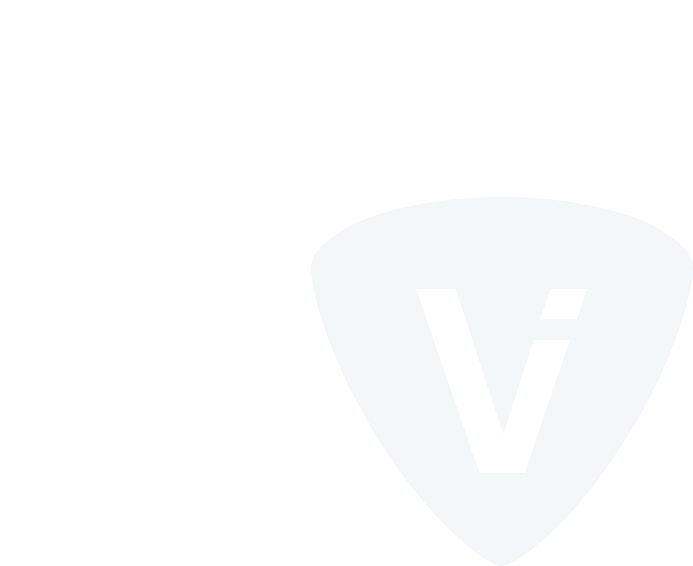
Metal Powder Handling in Additive Manufacturing (3D Printing)
We offer a wide range of products to handle and convey metal powders for additive manufacturing in both the pre- and post-printing stages. The material cycle can be realized as a holistic solution where a high degree of automation can be achieved simultaneously.
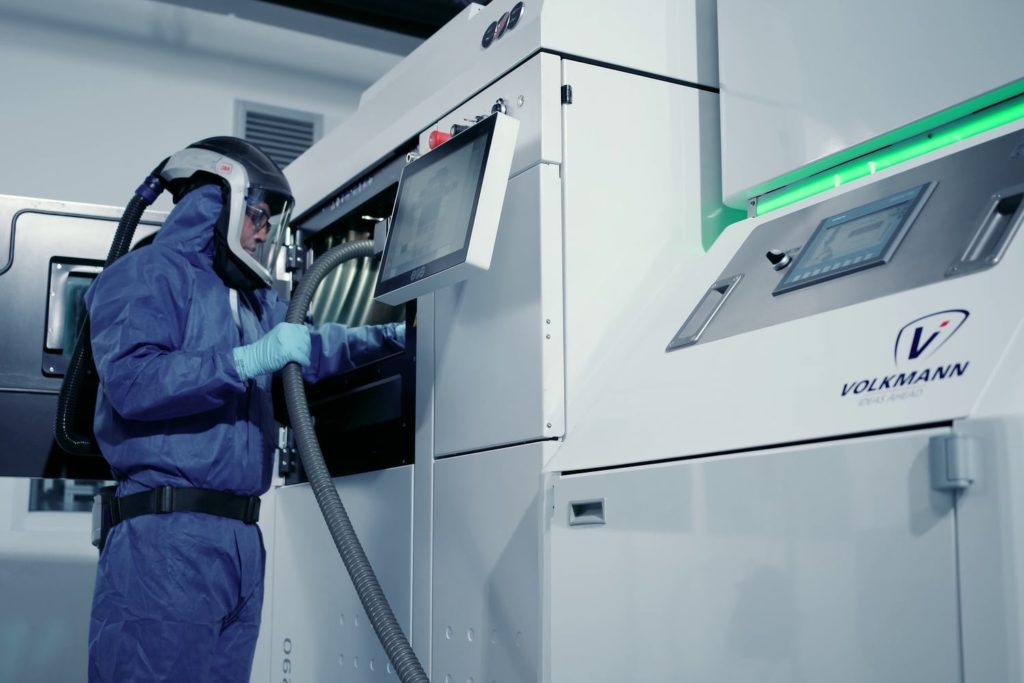
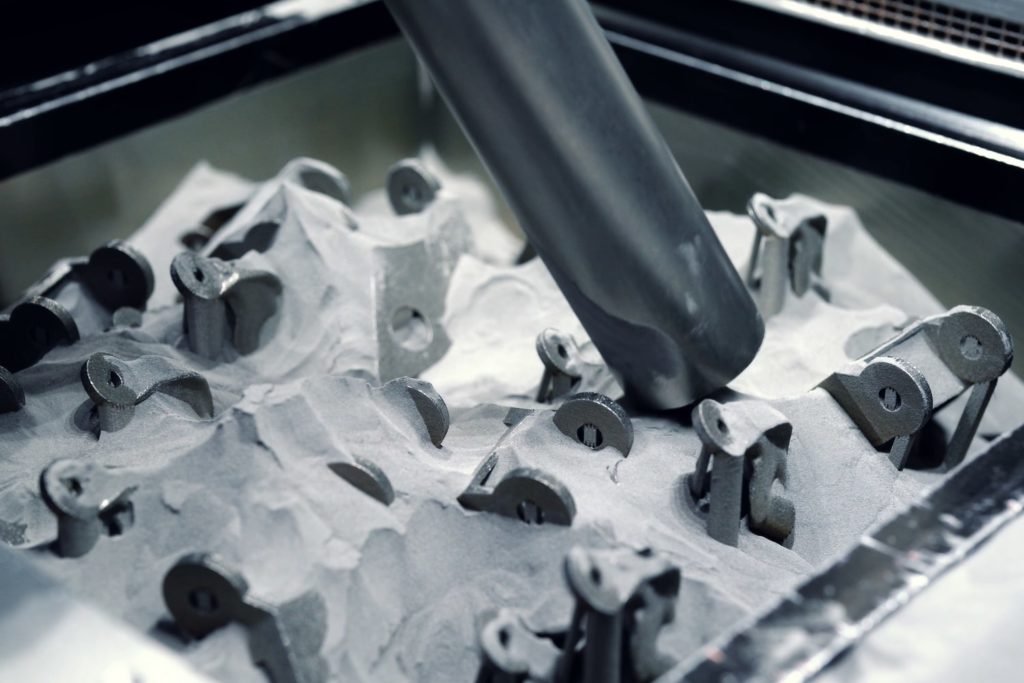
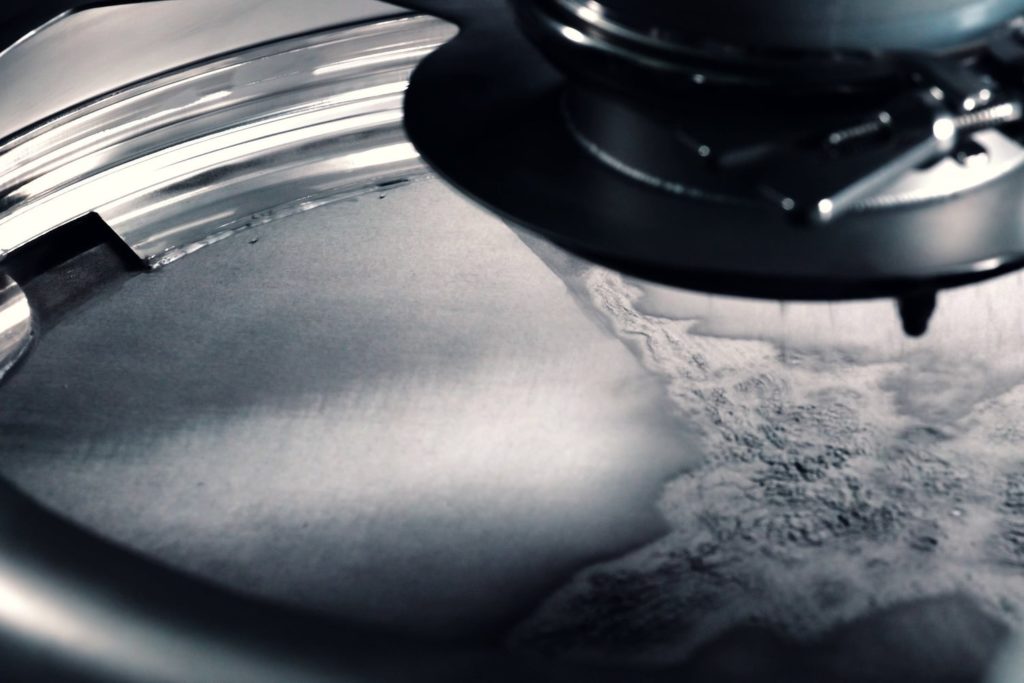
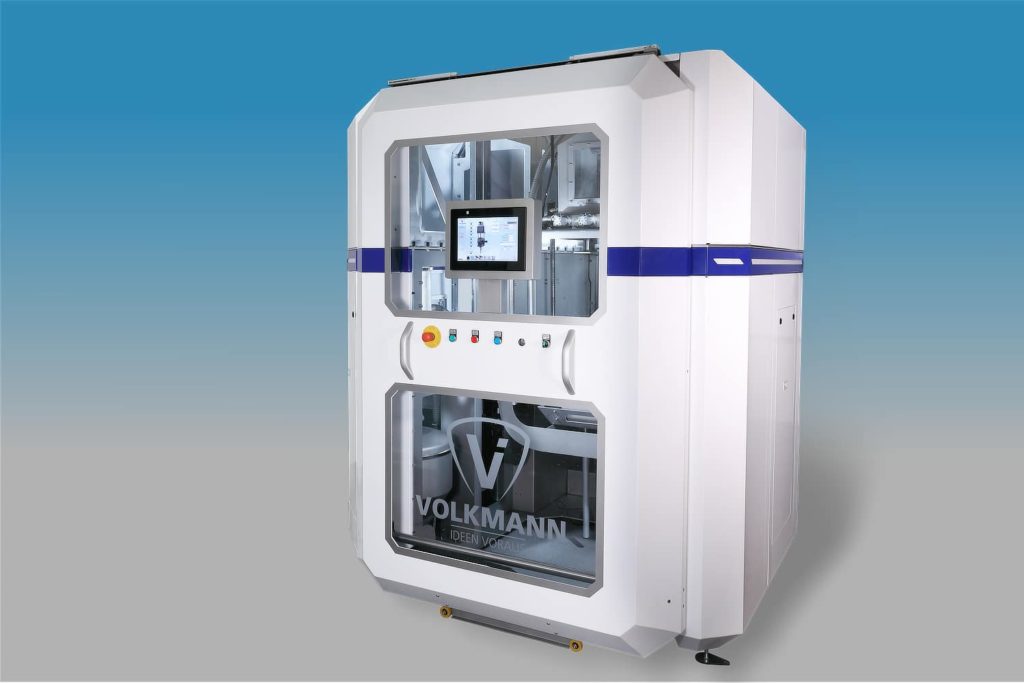
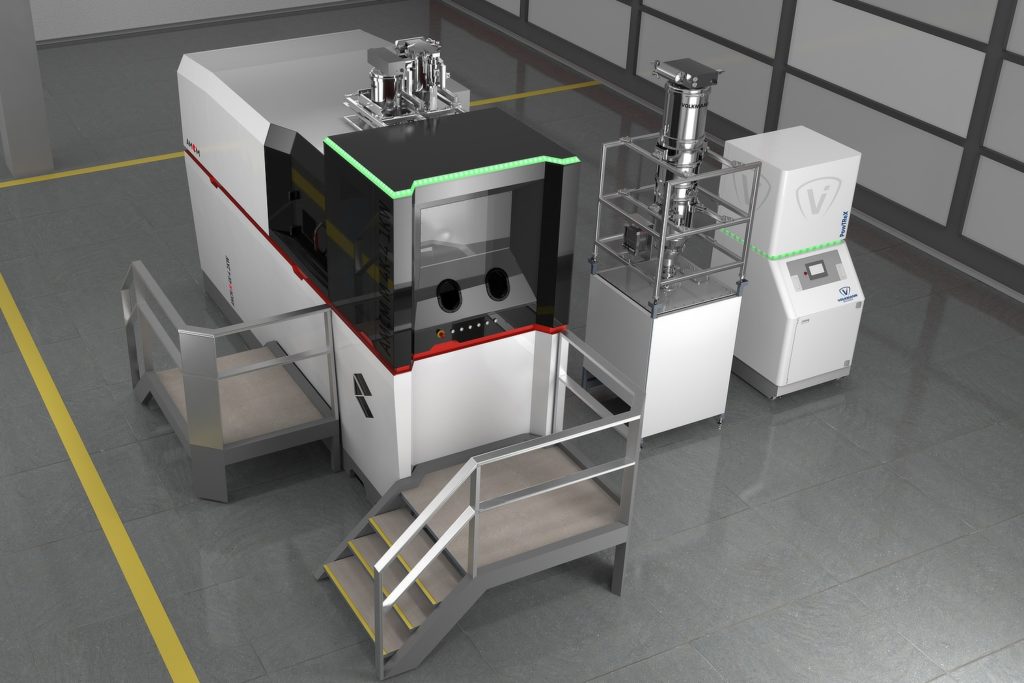
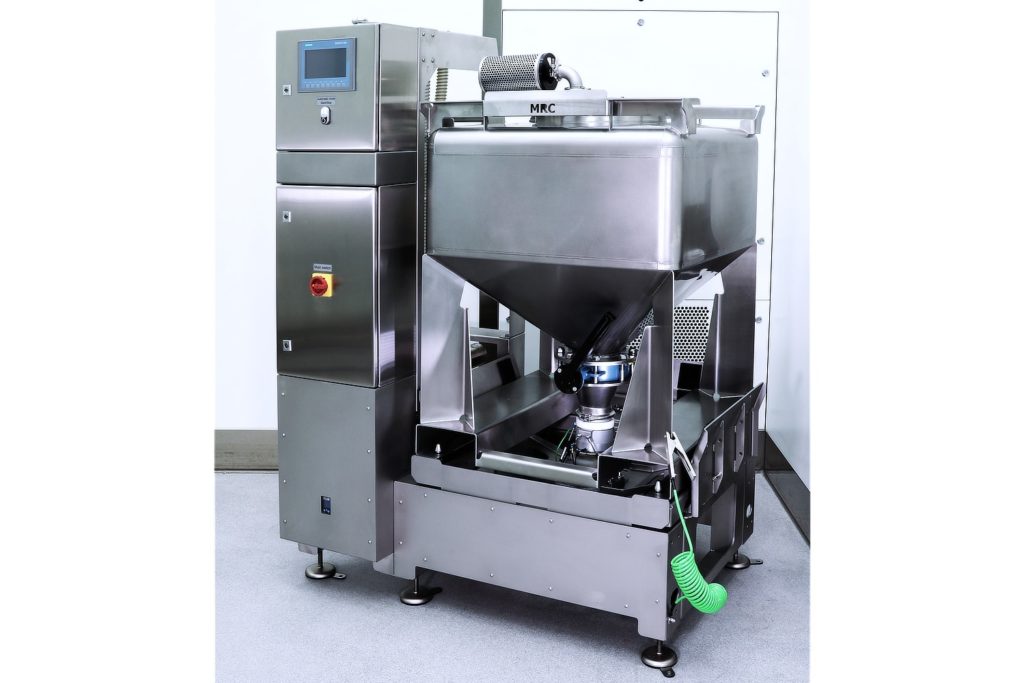
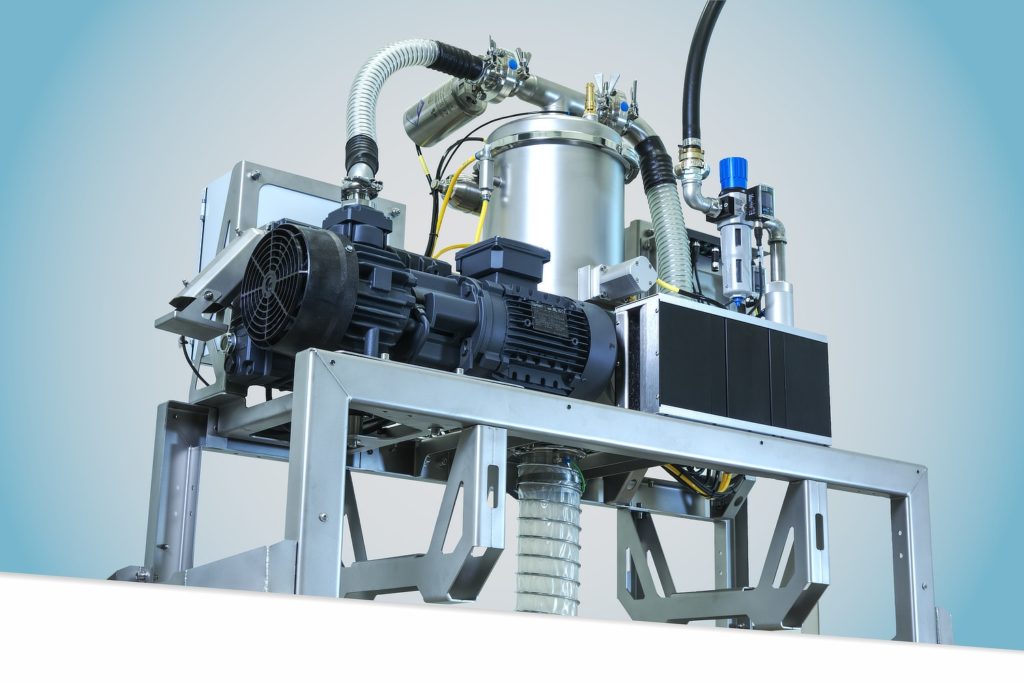
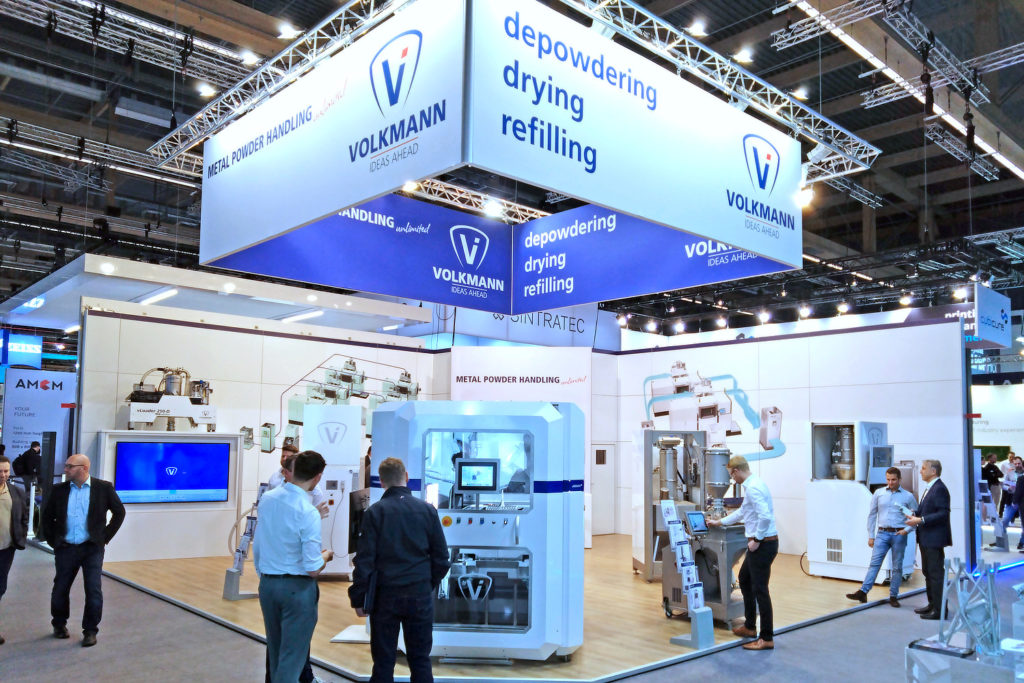
From old to new - the reprocessing of metal powders
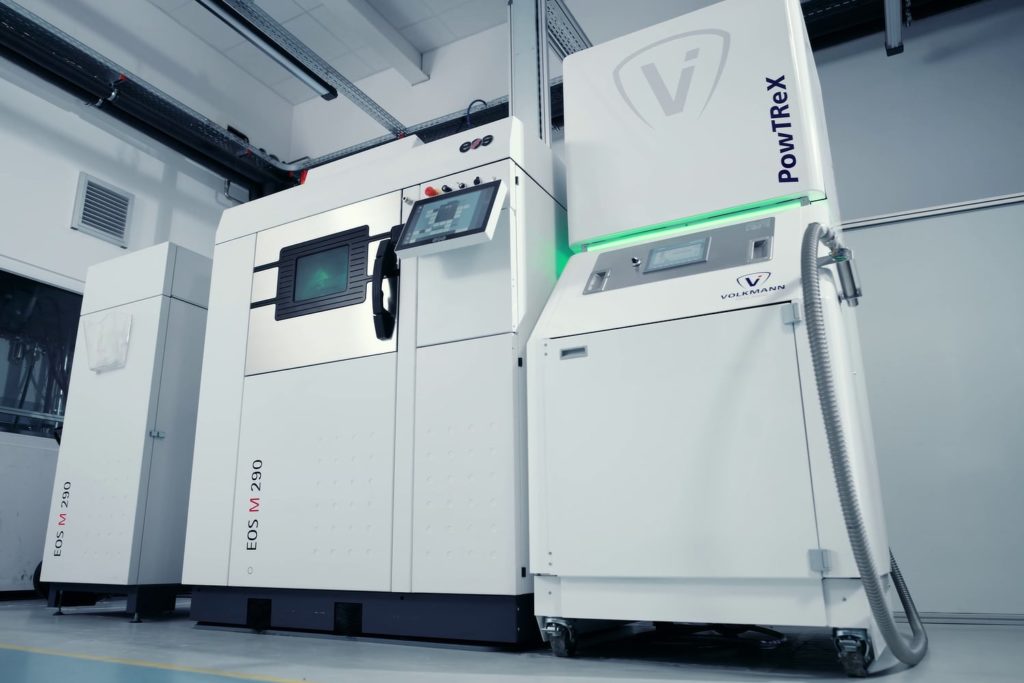
With powder reprocessing by a PowTReX-System, the excess metal powder from a build is prepared for reuse. Oversized particles such as metal spatter and broken support structures are safely removed by screening.
This reprocessing usually takes place in the direct vicinity of 3D printer where the in-house logistics are most efficient. This is aided by the transfer of the powder through pipelines or hoses, using vacuum conveying, from the printer to additional equipment.
Closed Powder Loop: Holistic material flow and automation
We cover the entire material flow of metal powder in pre- and post-printing with integrated and fully automated solutions. From the unpacking and depowdering of the build job, to the buffering and preparation of the used powder, to the filling of the printers with fresh or used powder. Various material flow concepts can be implemented. Flexibility also exists with regard to room layout, distances, and transport routes, even accommodating several floors.
Vacuum conveying of the metal powder between the individual machines enables a high degree of automation. For example, the 3D printer can be automatically supplied with metal powder from an IBC container. A reliable material supply, even during unmanned shifts or within 24/7 production, is thus achievable.
This video shows a selection of Volkmann solutions for the AM industry:
You are currently viewing a placeholder content from Youtube. To access the actual content, click the button below. Please note that doing so will share data with third-party providers.
More InformationDo you have questions about our products and services in additive manufacturing?
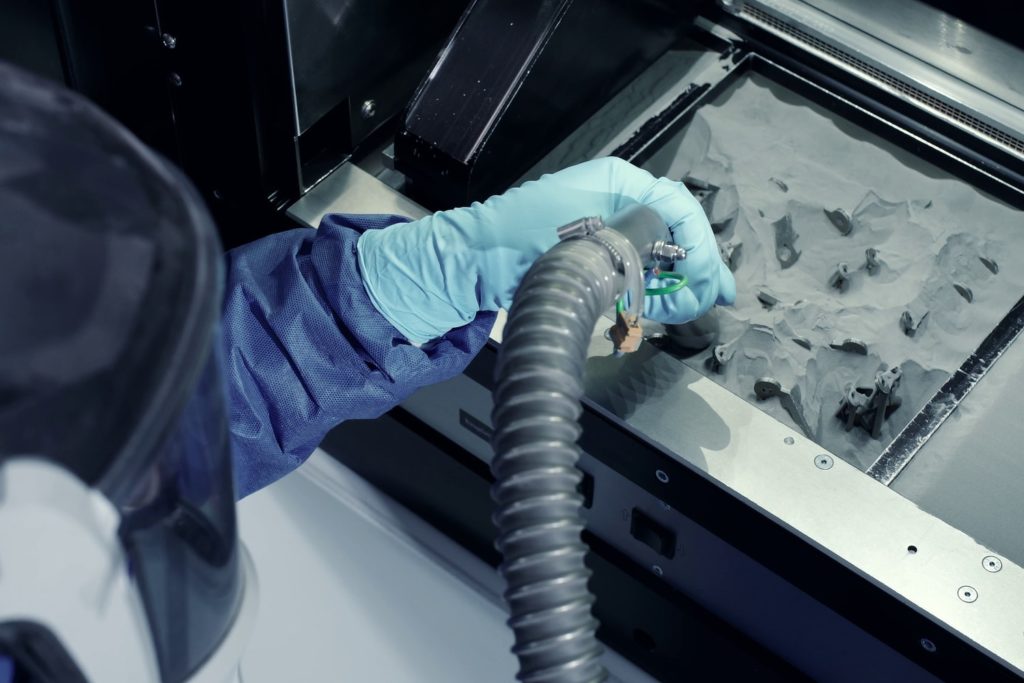
Protection of the metal powder and protection of the staff
The quality of the 3D printed component is only as good as the quality of the metal powder used. Handling and conveying in closed systems protects the powder from harmful environmental influences. Fewer manual operations equal fewer operator errors and product mix-ups. Additional vacuum drying operations even improve the flow properties and thus the quality of the printed component.
Handling the metal powder in closed systems also protects personnel from harmful dust. The use of expensive personal protective equipment can therefore be reduced or even completely eliminated.
Established solutions for the AM industry
Renowned OEM manufacturers of 3D printers rely upon our products when it comes to handling metal powder on, or around, the 3D printer. Additionally, our customer base also includes numerous AM producers who use 3D printing to manufacture products for the automotive, aerospace and medical technology industries, amongst others.
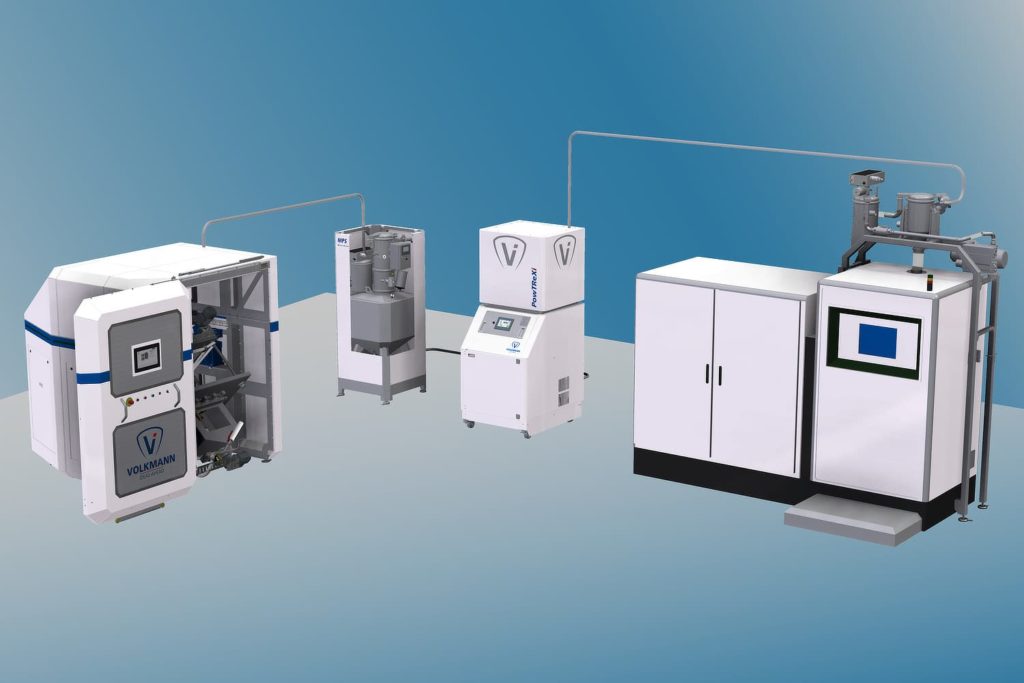
Powder handling with inert gas atmosphere
We can also offer the handling of the metal powder with the use of a protective gas such as nitrogen. Using a closed loop system the inert gas is recirculated repeatedly with a resulting economy of operating costs.
Drying of the metal powder
The quality of the metal powder or the printed component is considerably influenced by the adsorbed moisture level. This was proven during the IDAM research project in which VOLKMANN was involved as a project partner. This even applies to virgin metal powder that can adsorb moisture from the atmosphere during transport and storage.
However, by utilizing a drying process, the original powder quality can be fully restored. Such drying can be carried out easily and effectively by vacuum and can be integrated into a vacuum conveying system. When doing so the use of expensive inert gas for handling and conveying the powder can usually be dispensed with.
Our AM products at a glance
Supplementary information
The dust from many metal powders can cause a dust explosion if handled incorrectly. VOLKMANN is well known within the industry for its expertise in the safe design of equipment and systems in accordance with the ATEX directive, and this knowledge has been incorporated into our products and solutions for additive manufacturing. Read more about explosion protection and ATEX here.
Many metal powders and their associated dust are harmful to health, and this is a particular challenge in material handling; however, Volkmann implement appropriate solutions. For example, the exhaust air from vacuum conveying is cleaned with a HEPA filter as the second filter stage. Conveying under negative pressure offers the additional advantage that even in the event of a leak, no dust will escape to the outside environment.
We are enthusiastic about overcoming technical challenges and addressing new ideas. We develop customized solutions for individual client wishes by utilizing our modern technical center. Here we test the behavior of the powder and replicate plant related conditions in advance of manufacture, thereby optimizing the system design.
The IDAM research project
During the IDAM research project 1, as one of the 12 project partners, we undertook the depowdering, the reprocessing and the conveying of the metal powder. In doing so VOLKMANN achieved an important share of the project success with two completely automated and digitalized production lines at BMW and GKN Additive.
1) supplementary information about the IDAM research project:
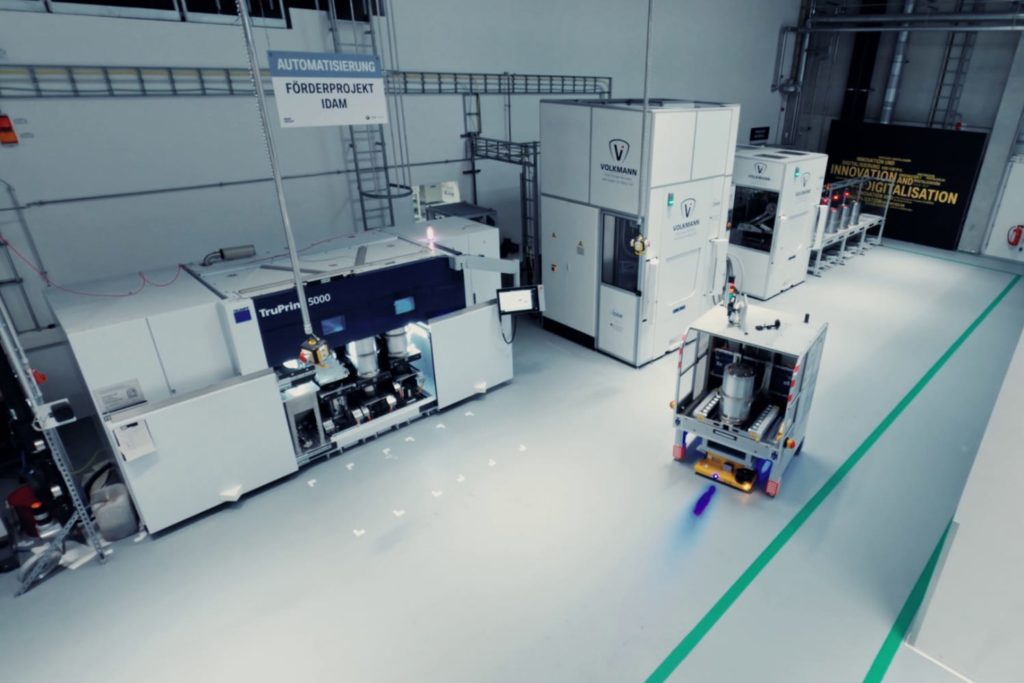
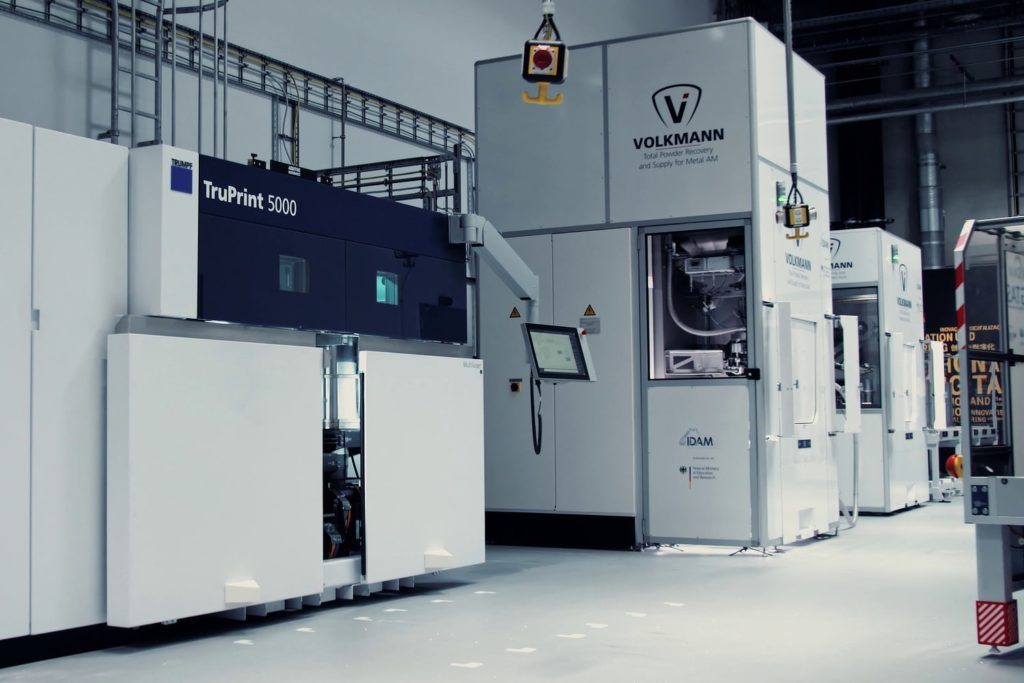
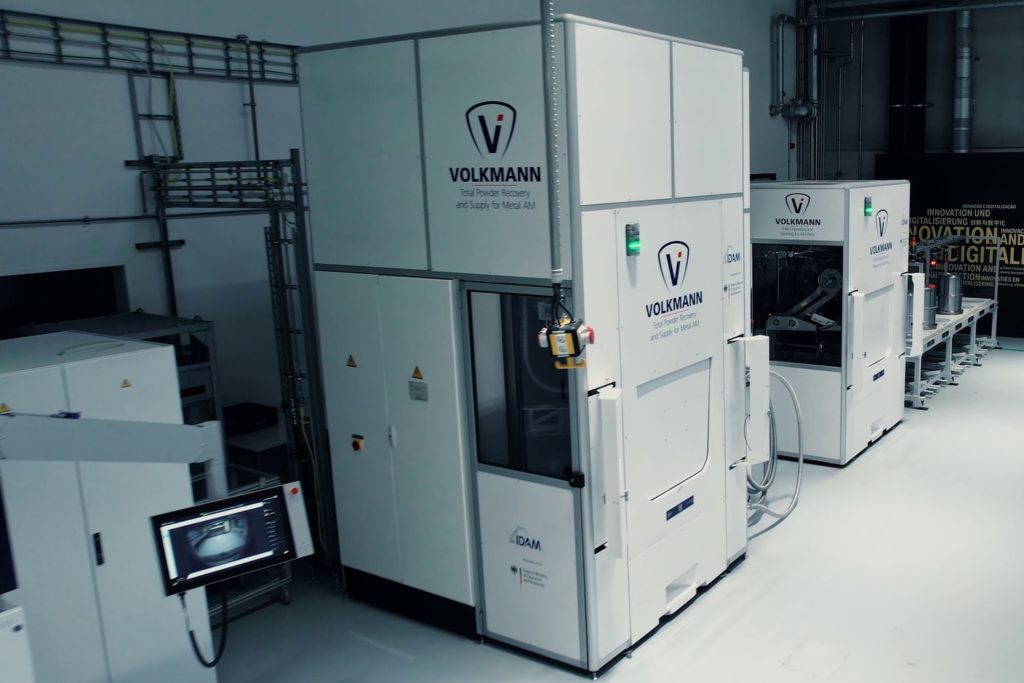
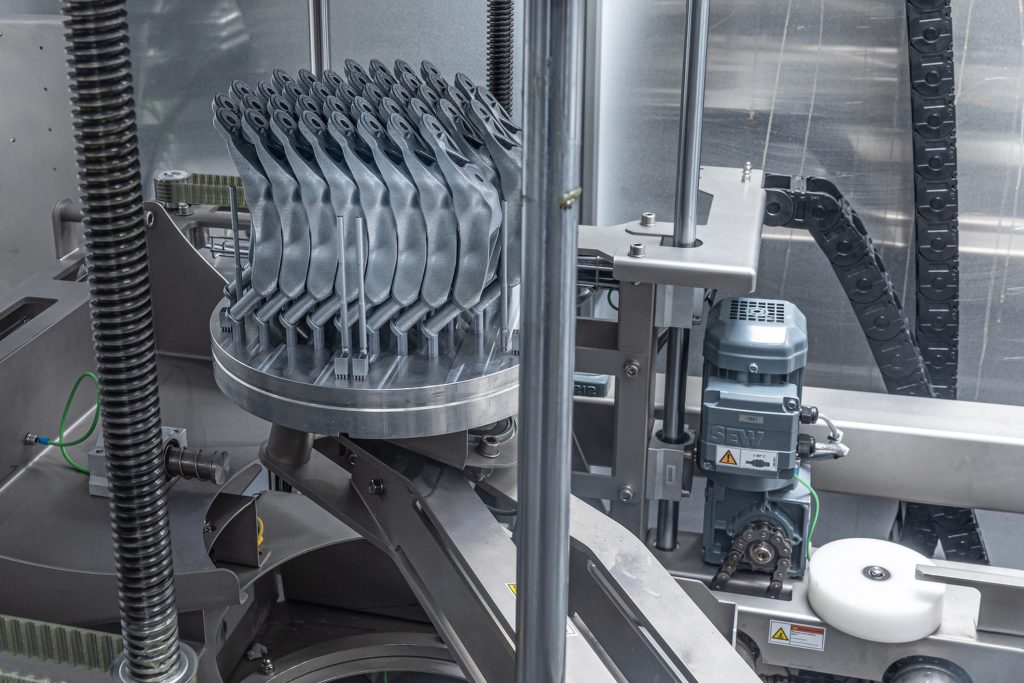
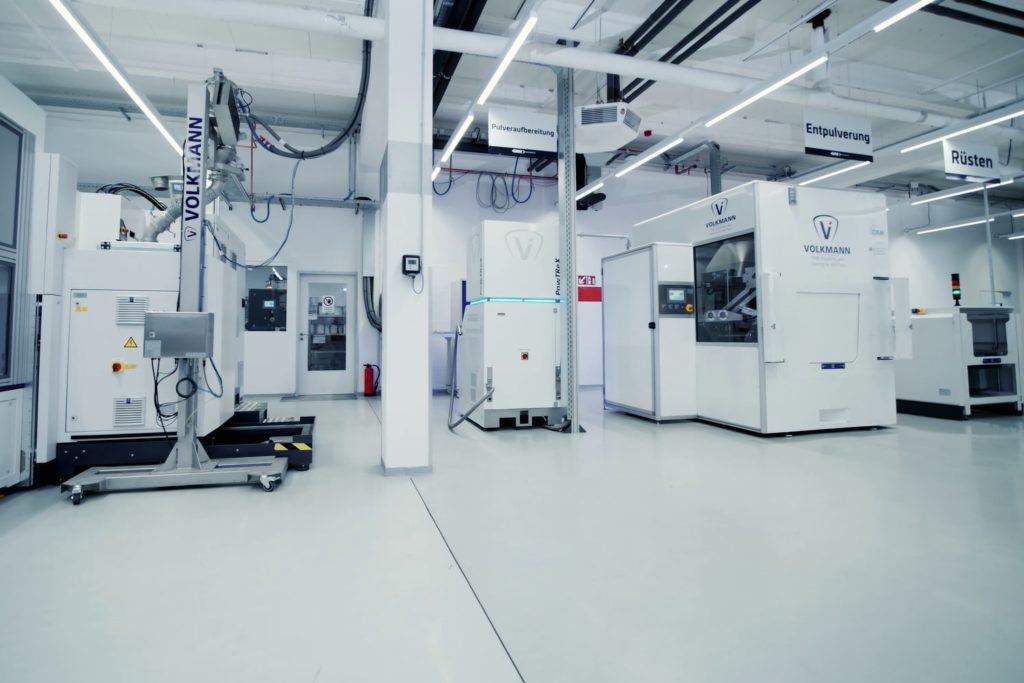
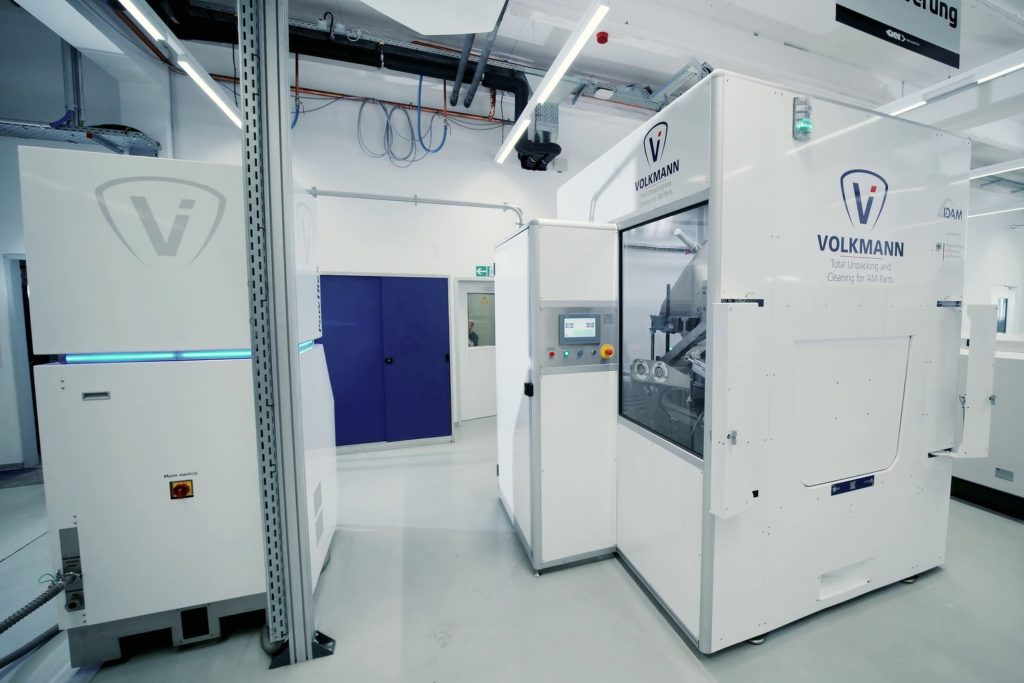
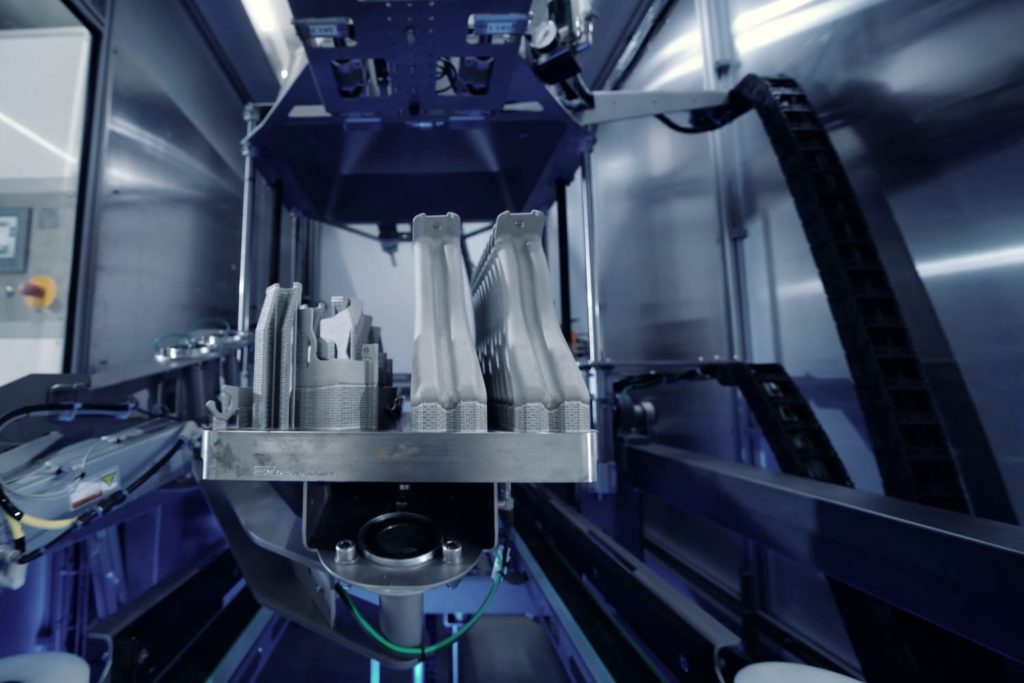
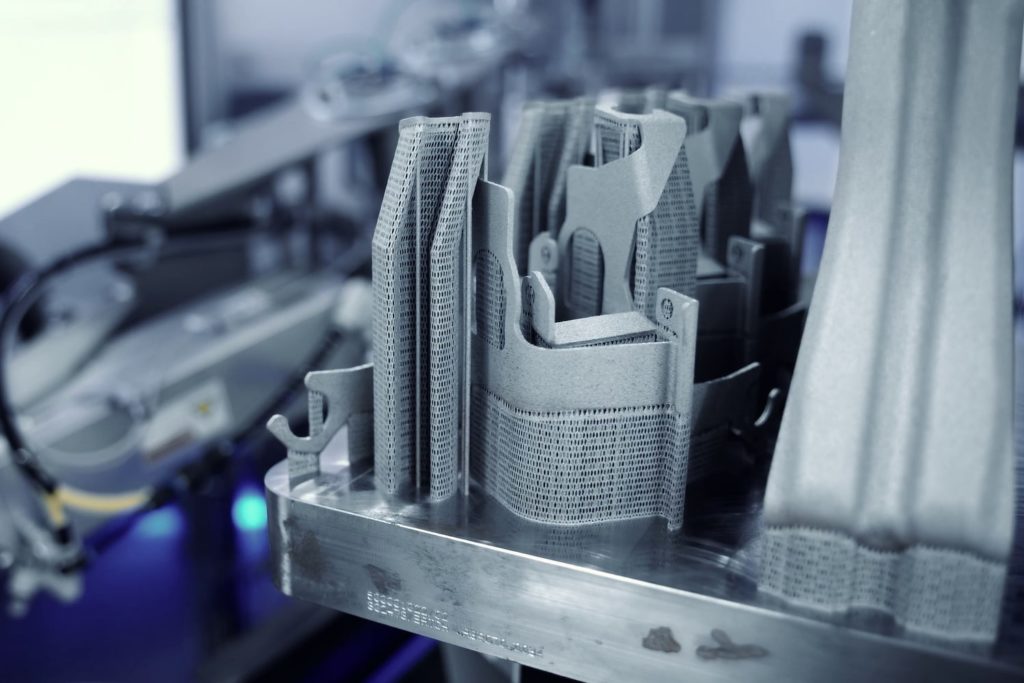
This video presents the two demonstrator lines of the IDAM research project at BMW AG and GKN Additive:
You are currently viewing a placeholder content from Youtube. To access the actual content, click the button below. Please note that doing so will share data with third-party providers.
More InformationOur articles about additive manufacturing
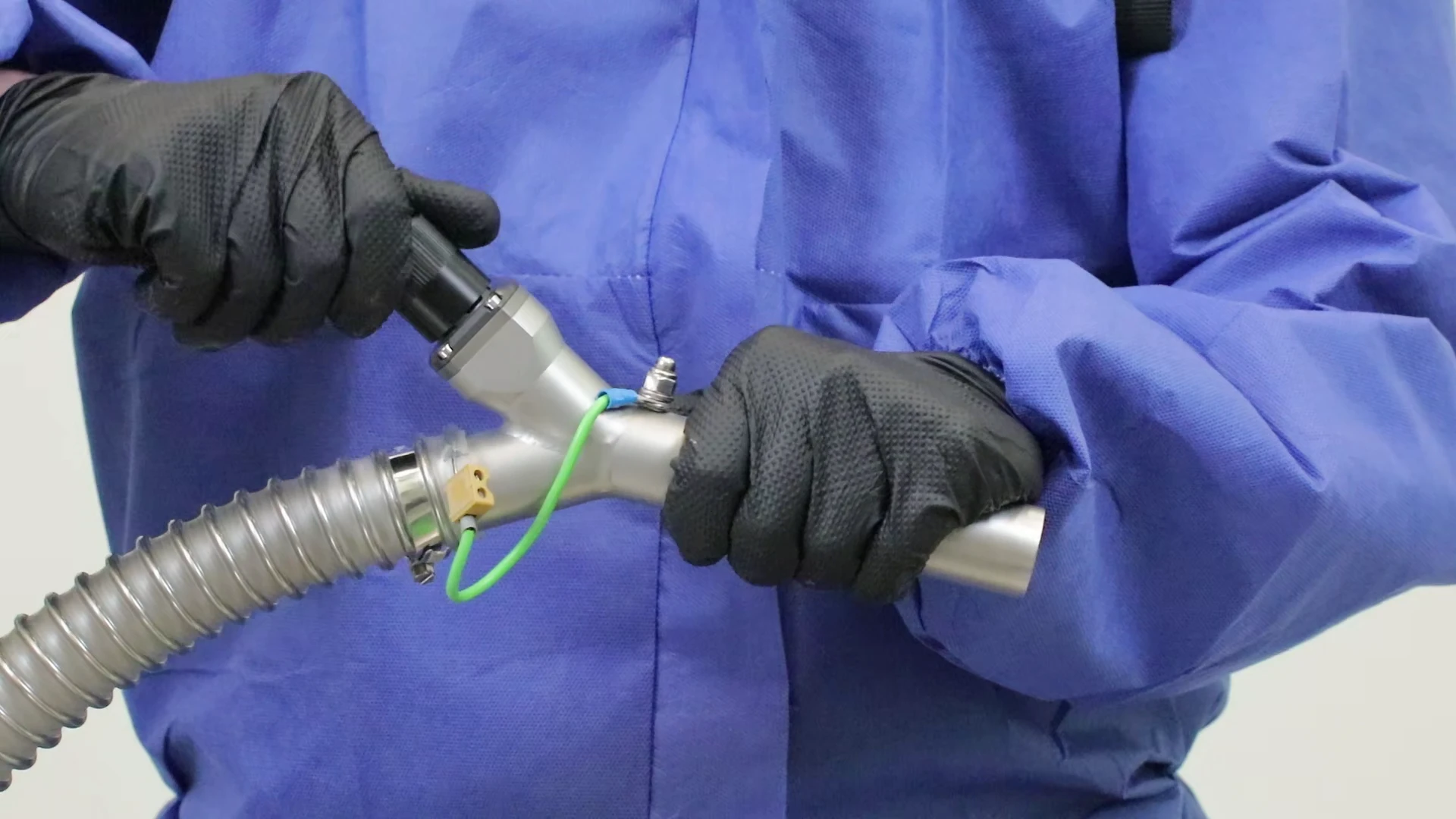
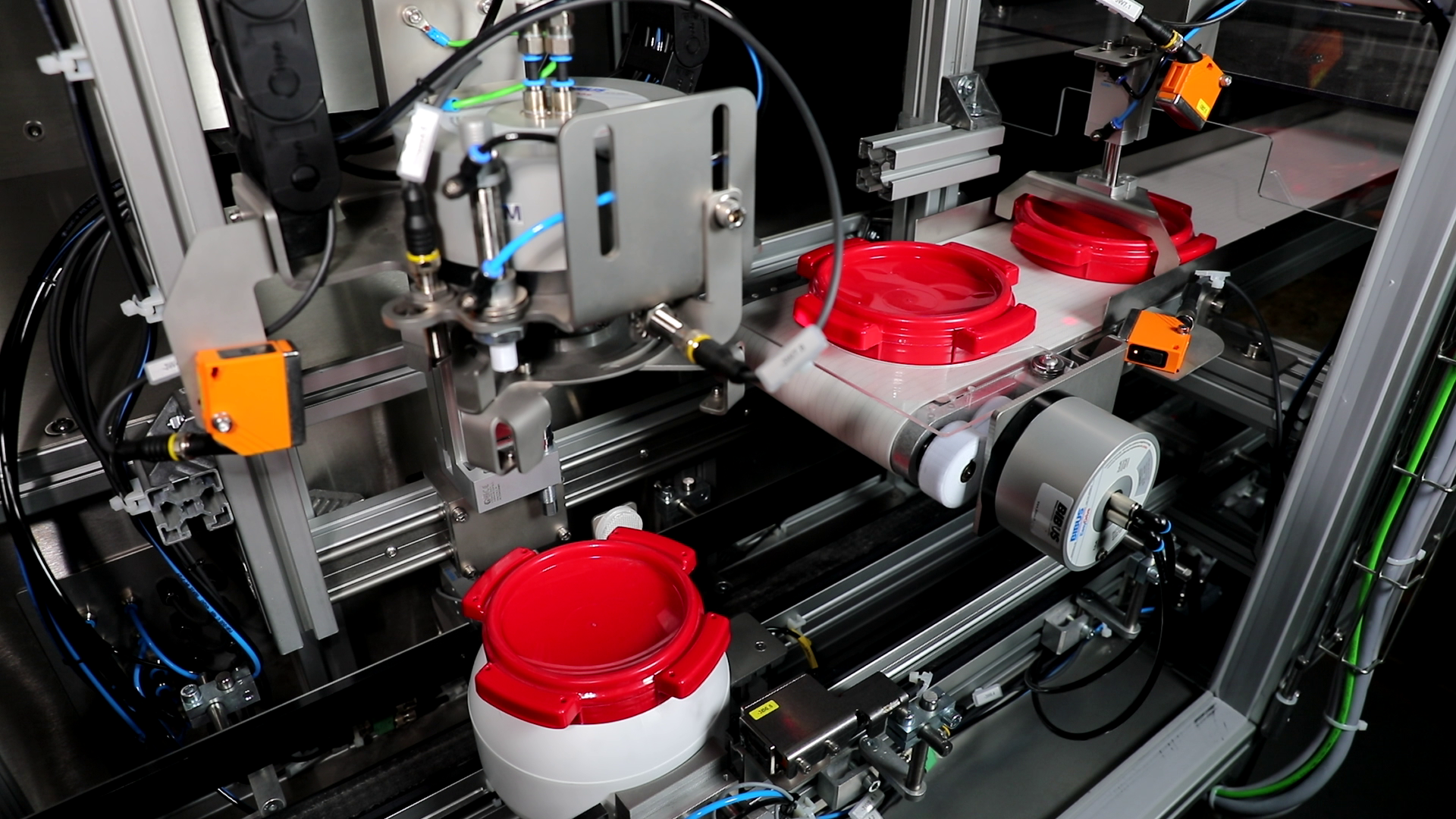
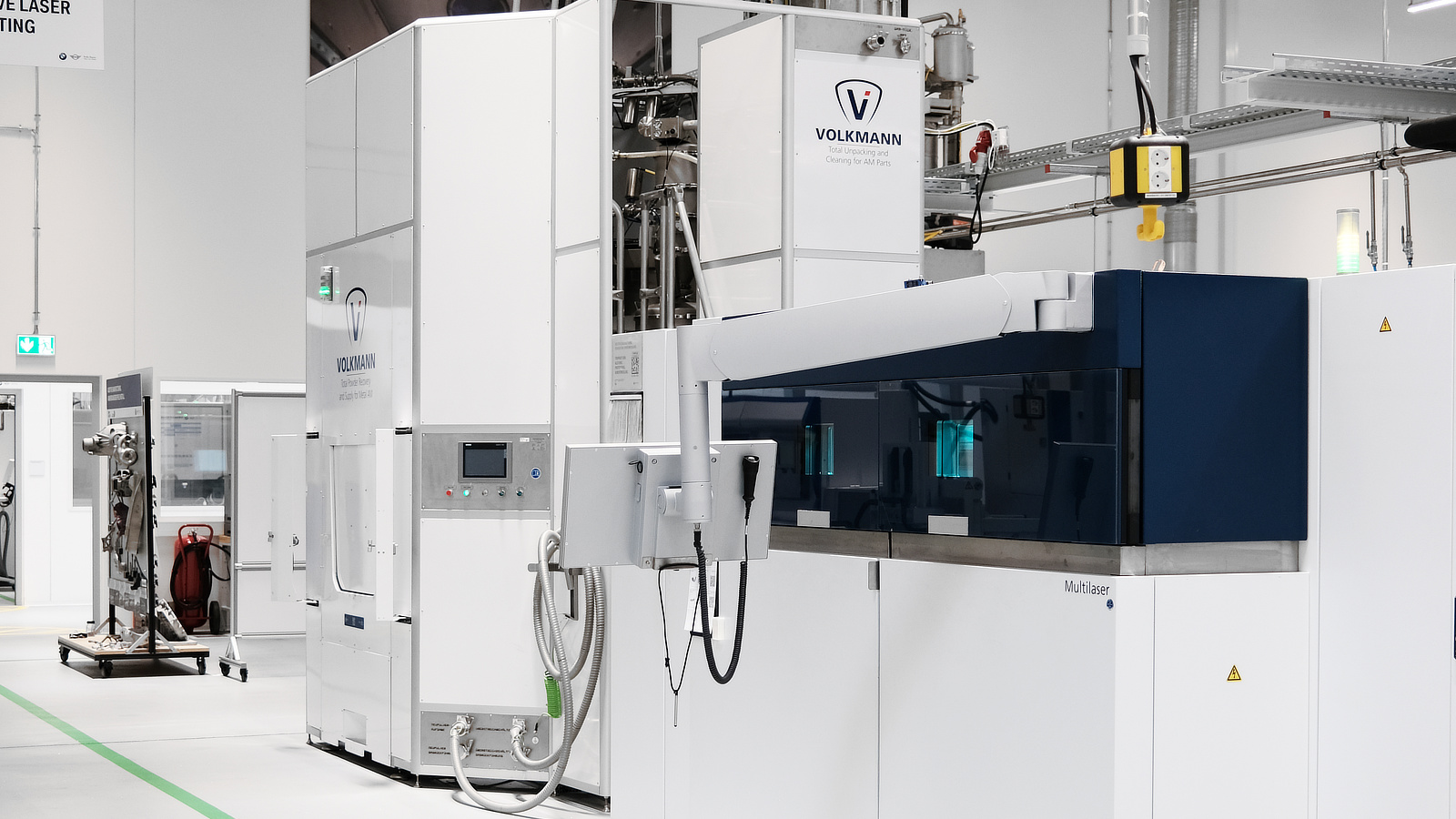
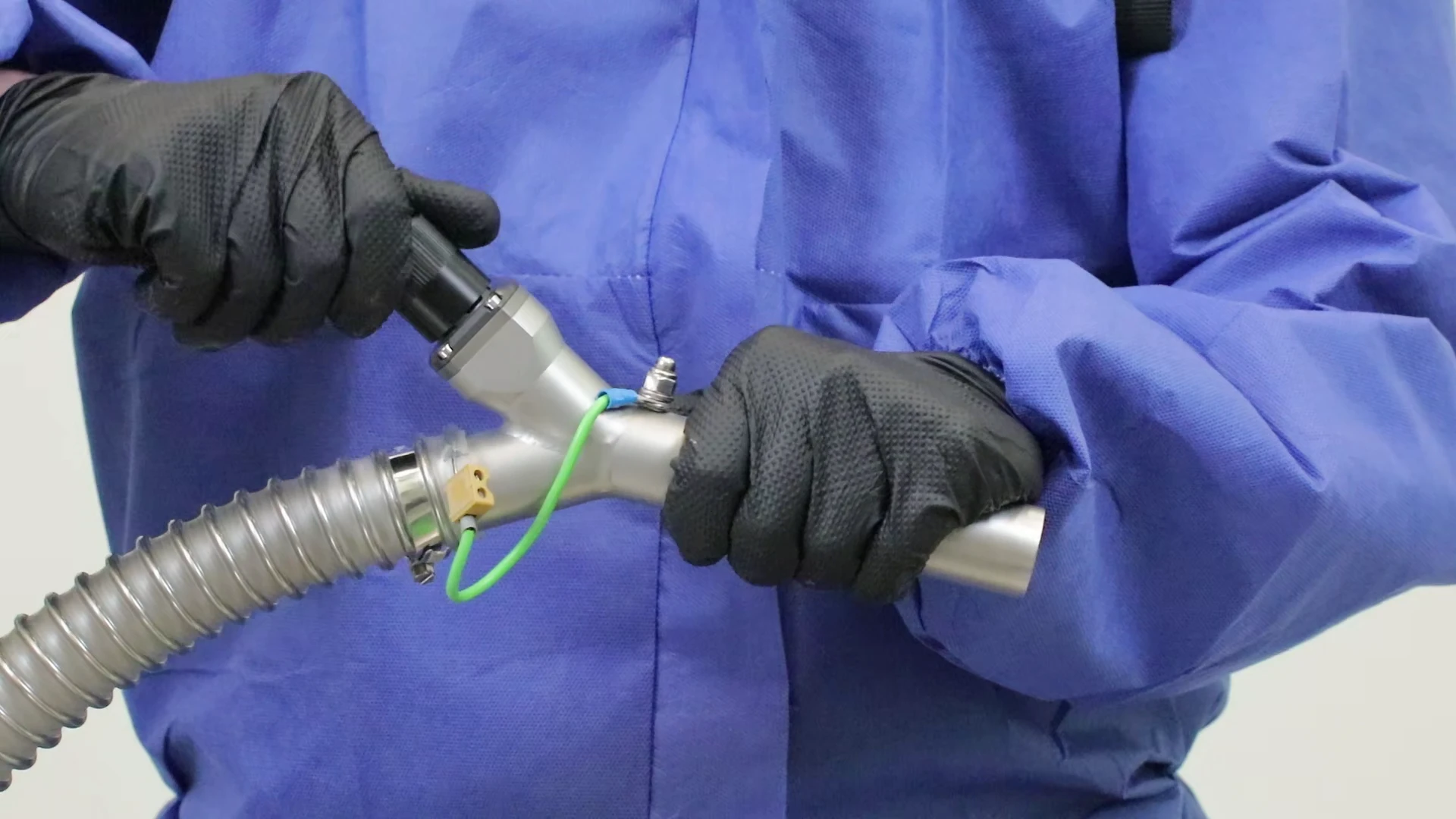
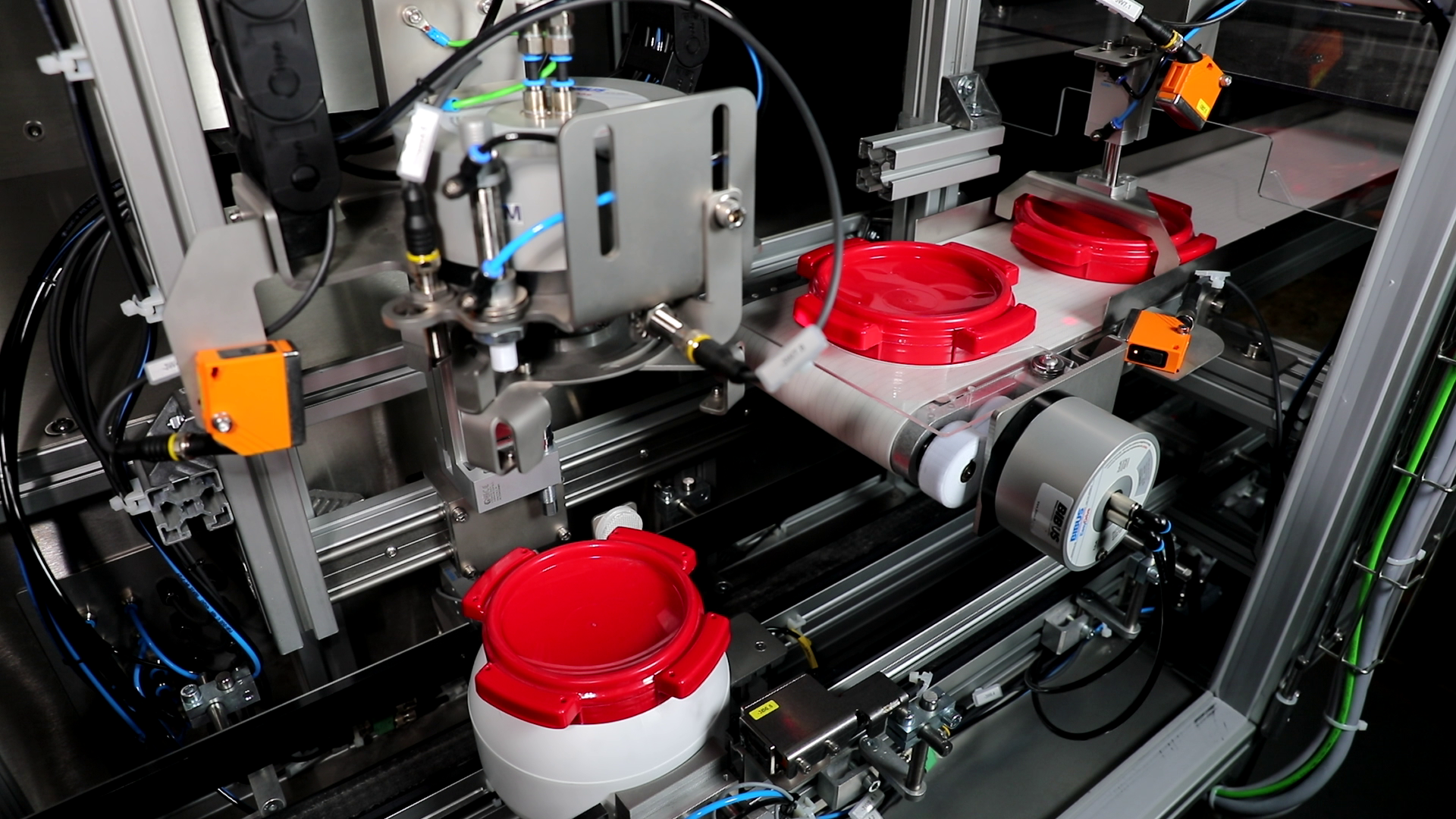
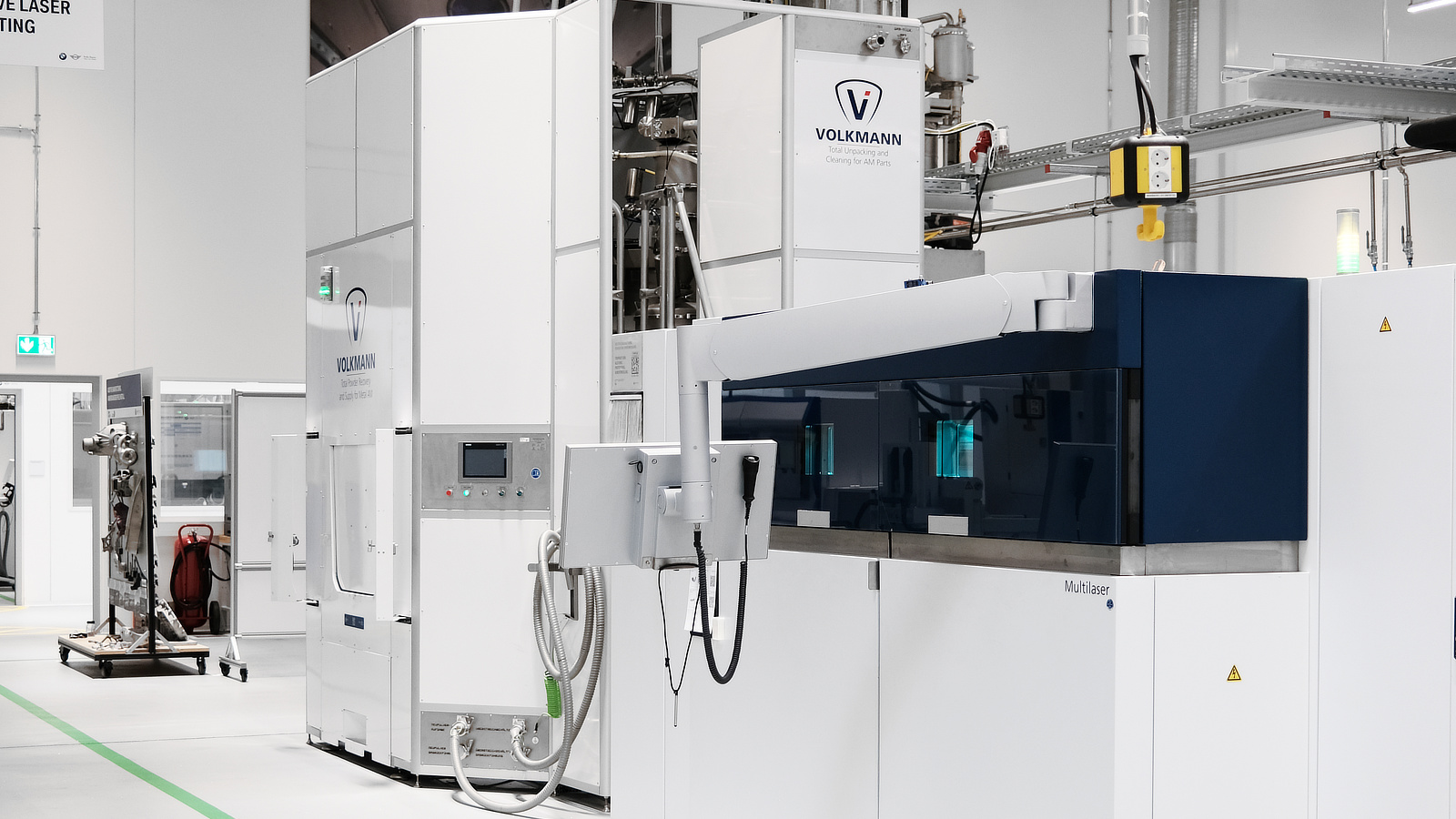